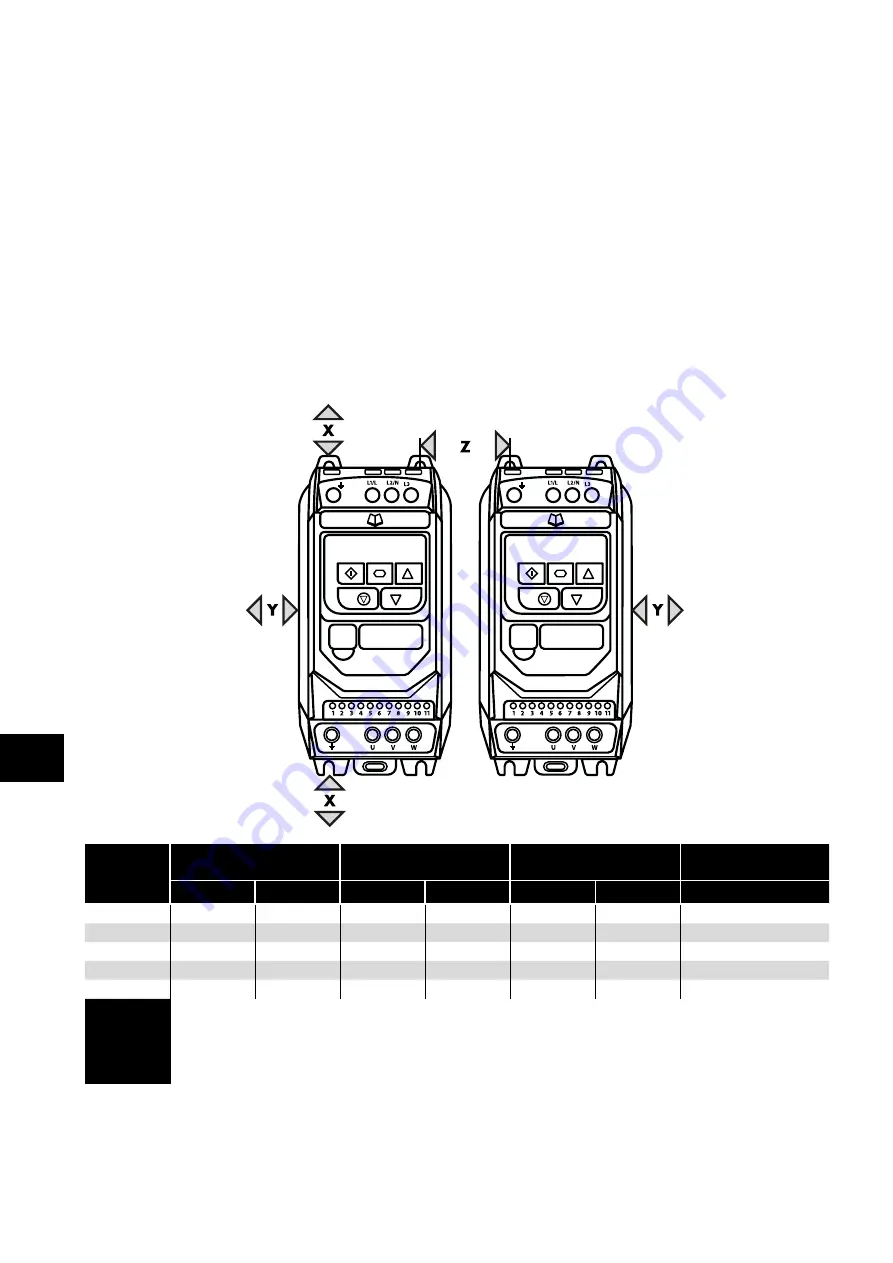
10
| Optidrive ODE-3 User Guide |
Version 1.00
www.invertekdrives.com
3
Mech
anical Installation
3.4. Guidelines for Enclosure Mounting
IP20 drives are suitable for use in pollution degree 1 environments, according to IEC-664-1. For pollution degree 2 or higher
environments, drives should be mounted in a suitable control cabinet with sufficient ingress protection to maintain a pollution
degree 1 environment around the drive.
Enclosures should be made from a thermally conductive material.
Ensure the minimum air gap clearances around the drive as shown below are observed when mounting the drive.
Where ventilated enclosures are used, there should be venting above the drive and below the drive to ensure good air circulation.
Air should be drawn in below the drive and expelled above the drive.
In any environments where the conditions require it, the enclosure must be designed to protect the Optidrive against ingress of
airborne dust, corrosive gases or liquids, conductive contaminants (such as condensation, carbon dust, and metallic particles) and
sprays or splashing water from all directions.
High moisture, salt or chemical content environments should use a suitably sealed (non-vented) enclosure.
The enclosure design and layout should ensure that the adequate ventilation paths and clearances are left to allow air to circulate
through the drive heatsink. Invertek Drives recommend the following minimum sizes for drives mounted in non-ventilated metallic
enclosures:
Drive Size
X
Above & Below
Y
Either Side
Z
Between
Recommended
airflow
mm
in
mm
in
mm
in
CFM (ft3/min)
1
50
1.97
50
1.97
33
1.30
11
2
75
2.95
50
1.97
46
1.81
22
3
100
3.94
50
1.97
52
2.05
60
4
100
3.94
50
1.97
52
2.05
120
5
200
7.87
25
0.98
70
2.76
104
NOTE
Dimension Z assumes that the drives are mounted side-by-side with no clearance.
Typical drive heat losses are 3% of operating load conditions.
Above are guidelines only and the operating ambient temperature of the drive MUST be
maintained at all times.