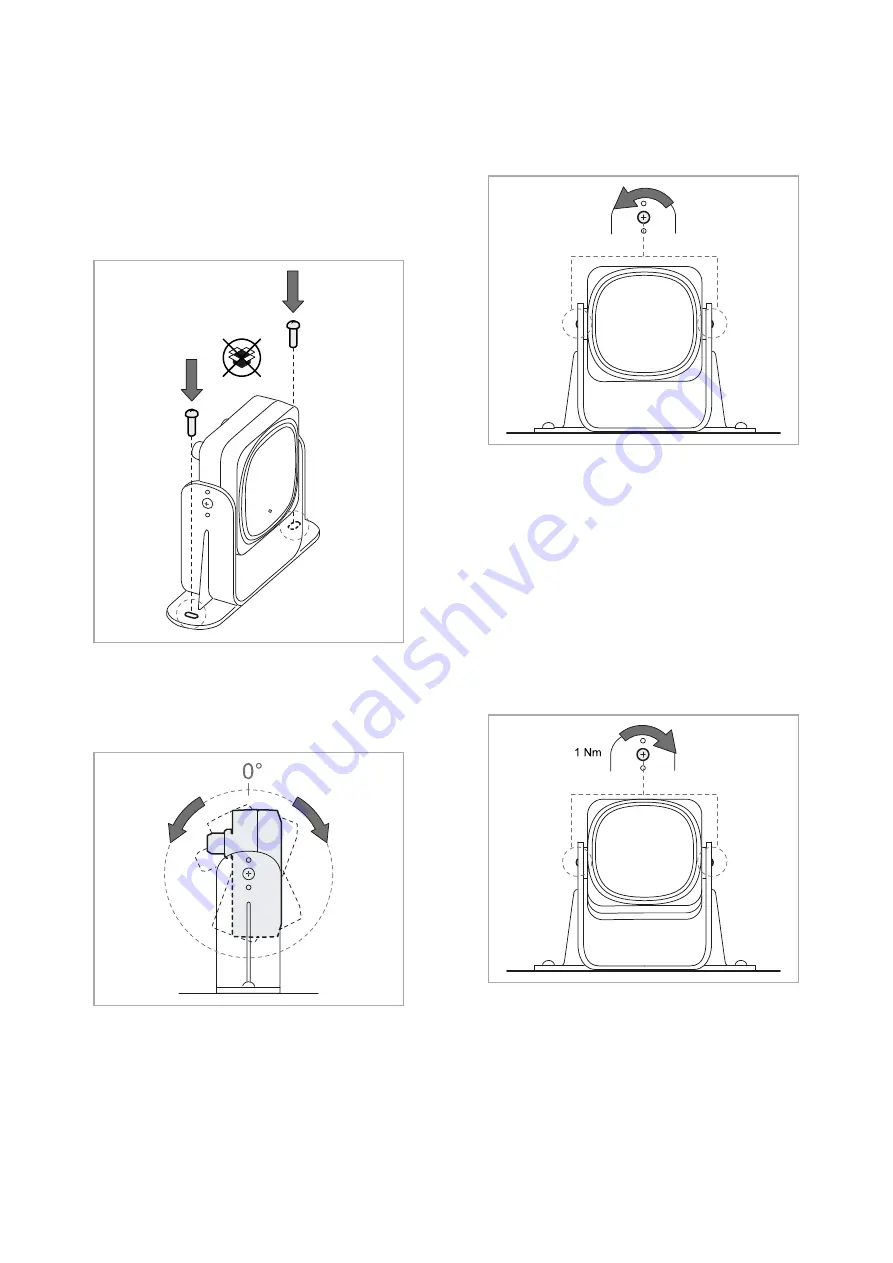
6.2.5 Install sensors on the floor
Note
: for installation with Metal protector kit (product code 90202ZAA), see the instructions supplied with the kit.
1. Position the sensor as indicated in the
configuration report and fasten the bracket
with two tamper-proof screws directly onto the
floor or another support.
NOTICE
: make sure the support does not inhibit
machinery commands.
2. Loosen the side screws to tilt the sensor.
3. Direct the sensor up to the desired inclination,
see "Sensor position" on page 52.
Note
: a notch is equal to 10° of inclination.
4. Tighten the screws.
6. Installation and use procedures
LBK System Series | Instruction manual v1.2 SET 2021| SAF-UM-LBKBus-en-v1.2 | © 2020-2021 Inxpect SpA
65