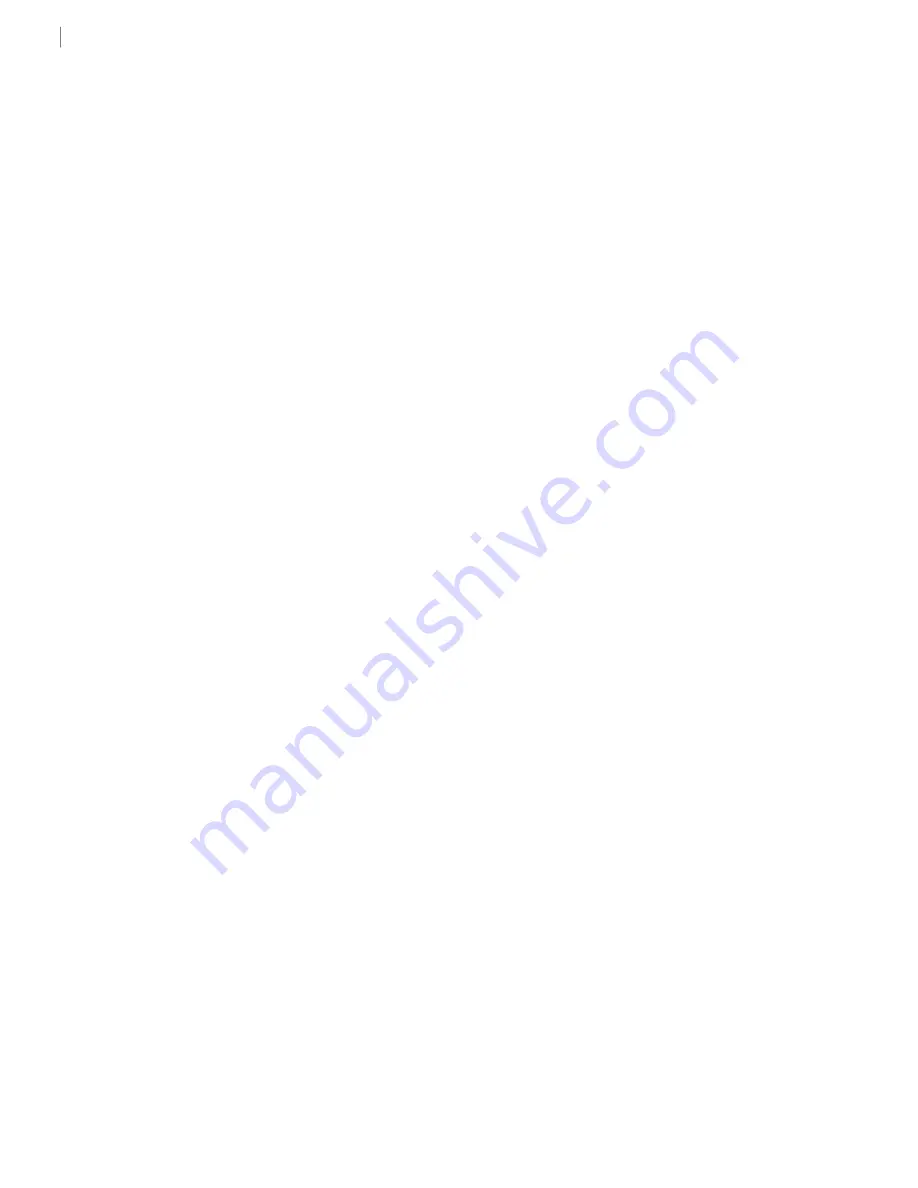
98
Ioline FlexJet Service Manual
98
Cartridge count
27
Download firmware
26
Error messages
34–35
Exit
26
Frame size
27
Get plotter data
27
Help about
26
Installation
24
Line width
27
Main Menu 25
Measurement units
28
Menu Bar
26
Menu Options
27
Quality setting
28
Reset machine ID
26
Scale
27
Screen Menu
25
Send command
26
Send plot file
26
Set key code
26
Set machine ID
26
Settings
26
Size calibration
26
Software version
27
Control panel
—
See
Keypad
Conversion
23
CorelDraw!
®
19
Covers
xvi
Cross-member
xvii
Customer service
59
Contact information
59
D
Dancer bar
Front dancer bar
42
Insertion 19
,
21
,
29
,
30
,
31
,
32
Rear (heavy) dancer bar
42
Data bits
37
Design software
22, 27, 37, 38, 41
DM/PL
19, 20, 22, 23
Draft mode
20, 28
Drive shaft
39, 43
Drive shaft marker
xviii
Location xviii
DXF
19, 20, 23
E
End covers
xvi
Error codes
Firmware update
36
Keypad errors
36
Error messages
33
F
Feed roll
xvi, 42
Feed shaft
xvi, 40
File formats
22, 23
Files
Conversion
23
Download firmware
26
File name extensions
EPS
26
PLT
26
PLX
26
Plot file adjustments
—
See
Control Center
Send plot file
26
Firmware
26, 34, 86
Software version
27
Updating
26, 35
FlexJet
Connections
37
Front close-up
xviii
Front View
xvi
Pre-wiring for expansion
26
Rear view
xvii
Settings
27
Start-up process
24
FlexJet Control Center
—
See
Control Center
FlexJet Quick Start Guide
xv, 39, 43
FlexJet User Guide
xiv, 42, xv, 38, 43, 44, 46, 49
FlexPlot
xv, 19, 22, 23, 24, 37
Installation
24
Workflow using CAD software 23
Workflow with FlexPlot 23
FlexPlot User Guide
xv, 22, 24
Flow control
37
Foot
Platen leveling foot close-up xvii
Stand leveling foot close-up xvi
Frame gap
38, 40, 46, 48, 49
Summary of Contents for FlexJet
Page 1: ...Service Manual Ioline FlexJet ...
Page 3: ...Service Manual Ioline FlexJet ...
Page 4: ......
Page 8: ......
Page 12: ......
Page 60: ...60 Ioline FlexJet Service Manual This page intentionally left blank ...
Page 90: ...90 Ioline FlexJet Service Manual This page intentionally left blank ...
Page 96: ...96 Ioline FlexJet Service Manual This page intentionally left blank ...