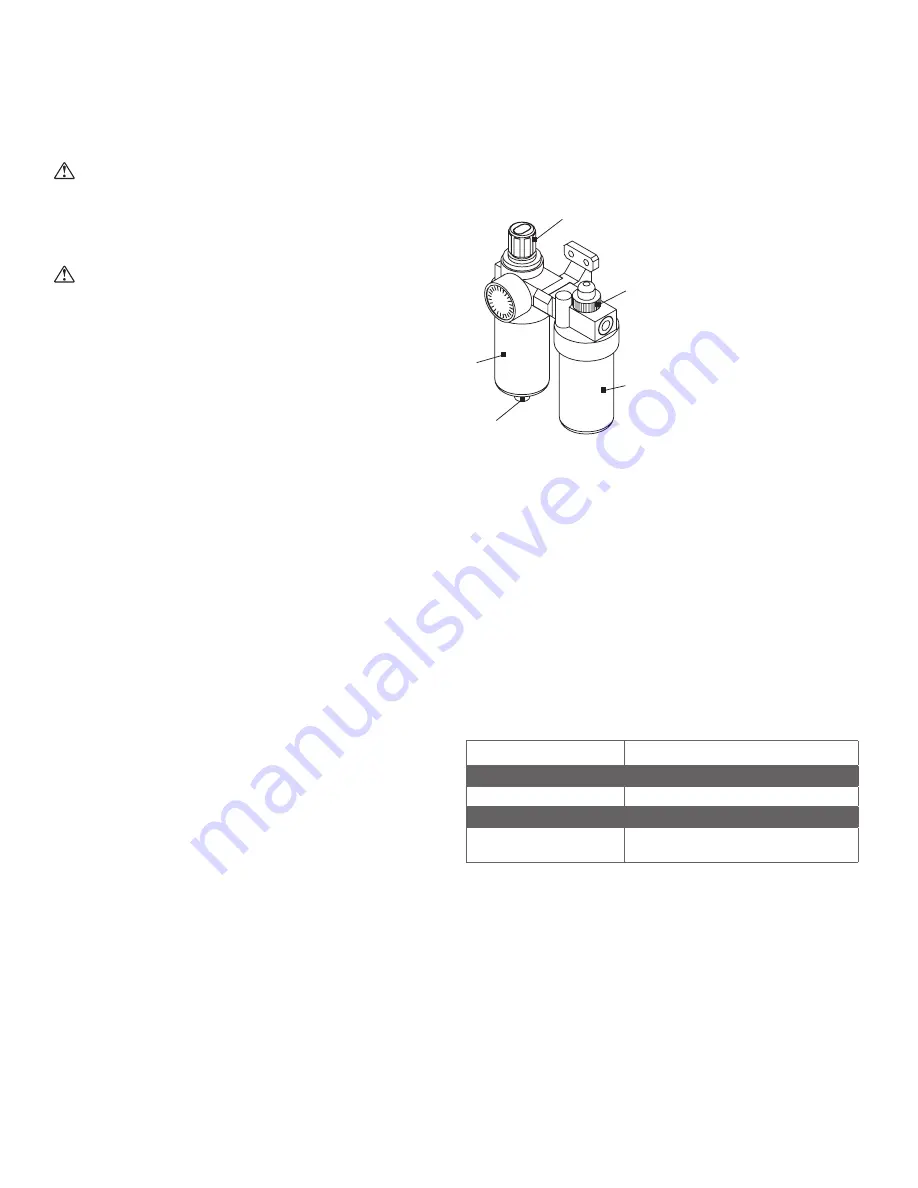
Ironwood BR23 | User Manual
19
8.0 Maintenance
WaRninG
Before performing any type of maintenance or adjustments, make
certain that the machine is disconnected from its power and air
source and completely shut off.
WaRninG
Never operate the machine until it has been properly lubricated and
all necessary maintenance work has been completed.
NOTE: After changing a setting, making an adjustment, performing
repair/maintenance work, or troubleshooting, please check that all
applicable safety functions are working properly before performing
another operation.
Clean all machinery parts and surrounding areas every day.
Keep a maintenance record and perform recommended
maintenance checks.
8.1 Lubrication
Weekly, clean and lightly oil the drill head guide bars and the
positioning screw of the boring head carriage using an ISO VG32 oil.
Every 1,000 hours of machine operation, lubricate the boring
head using a grease gun and a non-melting moly grease. Apply no
more than 6 grease-gun strokes.
Spindle bearings are permanently lubricated and require no further
lubrication.
Spindle bearings may purge grease during the first 20 hours
of operation. Wipe away any excess grease before starting the
machine.
Pneumatic System
A
E
B
D
C
Periodically fill the oil reservoir (B) with pneumatic oil. Use high-
quality pneumatic oil such as VG32 or other approved lubricant.
Drain and refill oil if there is condensation inside the reservoir (C). To
drain, press the drain knob (D).
NOTE: Reduced air flow can cause lack of lubrication. Be sure air
flow is properly adjusted to avoid mechanical damage from lack of
lubrication.
8.2 Cleaning
Blow dust from the machine frequently to avoid buildup of waste
material, dust and other debris.
8.3 Inspection
Feature
Interval/Situation
Boring head and bits
Every use
Emergency stop
Everyday – by functional test
Pneumatic system
Everyday
Electrical cabinet/system
Monthly: wiring terminals loose, insulation
deterioration, vacuum dust