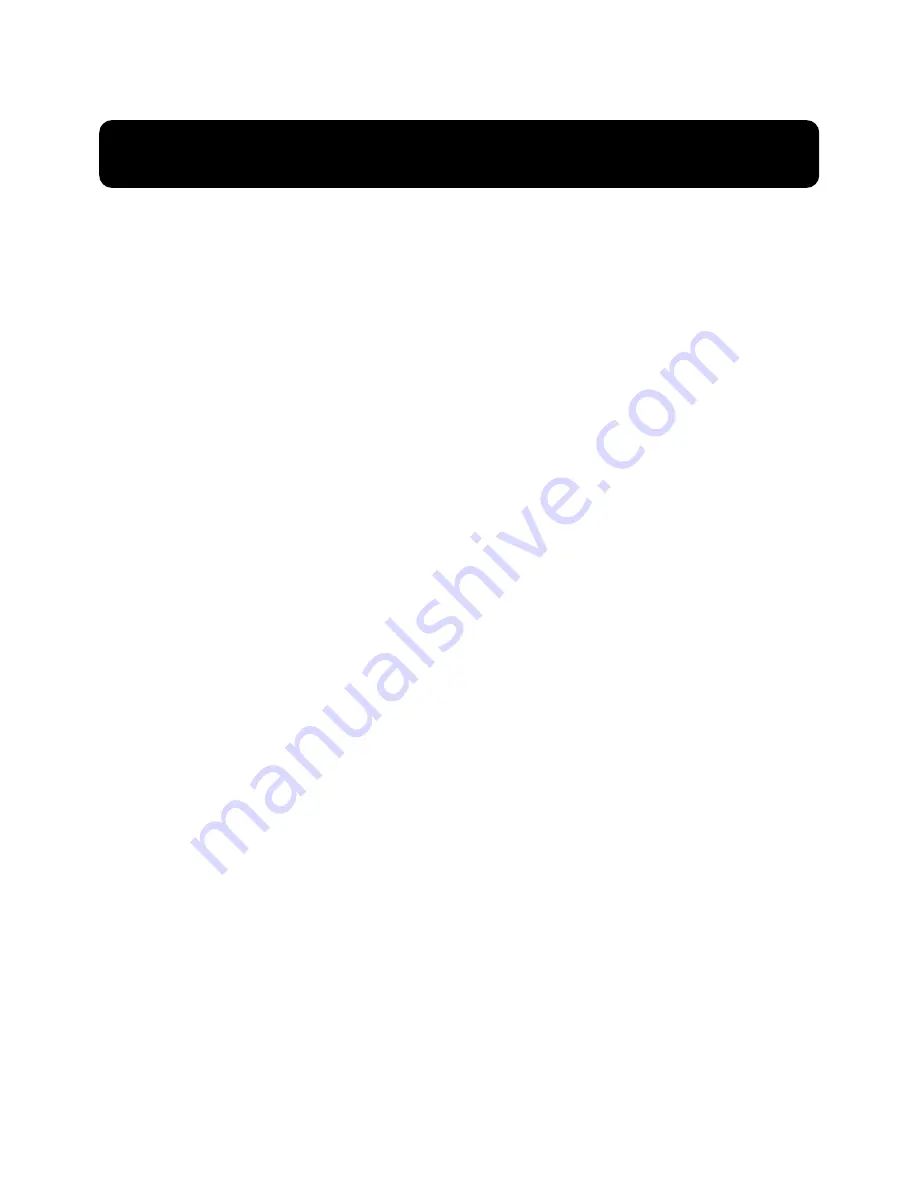
2
SERVICE MANUAL FOR SGR19 & SGR17
FOREWARD
This service manual has been prepared to provide the information and suggestions necessary for
servicing the ISEKI SGR equipped with the hydrostatic transmission. These include construction, specifica-
tions, removal and reinstallation of the components, disassembly and reassembly instructions, inspection
and adjustment instructions, troubleshooting, general precautions etc.
Figures mentioned in this manual are standard values established by ISEKI for the SGR, conse-
quently when a non-ISEKI part has been installed on the machine or adjustments and repairs have been
made in a manner other than as specified in this manual, the pertinent values mentioned herein are no longer
valid. ISEKI does not assume responsibility for problems or damage caused by a value deviation due to
maladjustment or by the use of unauthorized parts.
Servicing procedures outlined in the manual contain sufficient informa-
tion to return all component parts of a machine to new condition. In discussion of each
component part, it is assumed that a complete overhaul is being performed, conse-
quently, complete disassembly and reassembly are outlined. The machine is relied
upon to decide how far disassembly must be carried out when complete overhaul is not
required.
Study unfamiliar service procedures thoroughly and understand them clearly
before attempting disassembly. Specific data essential for proper overhaul, such as
running clearances and torque values, have been provided in interline of inspection
and reassembling procedures of each group section.
This manual was compiled from latest information available at time of
publication, However ISEKI reserves the right to make changes at any time without
notice.
Whenever the terms “left” and “right” are used, this means as viewed by
the operator when seated in the operator’s seat.
Whenever servicing the machines, pay sufficient attention to the opera-
tional safety to protect you and other persons around the machines from danger by
following carefully the instructions given in the manual. Never take chances!
Summary of Contents for SCM49
Page 1: ...S E R V I C E M A N U A L I S E K I L A W N M O W E R S LAWN MOWERS MOWER DECKS SCM48 SCM54 ...
Page 7: ...7 CHAPTER 1 INTRODUCTION 3 EXTERIOR VIEW AND DIMENSIONS 1935 mm 1965 mm 1100 mm 1265 mm ...
Page 36: ...36 SERVICE MANUAL FOR SGR19 SGR17 Fig 3 55 III 3 CYLINDER BLOCK 1 EXPLODED VIEWS ...