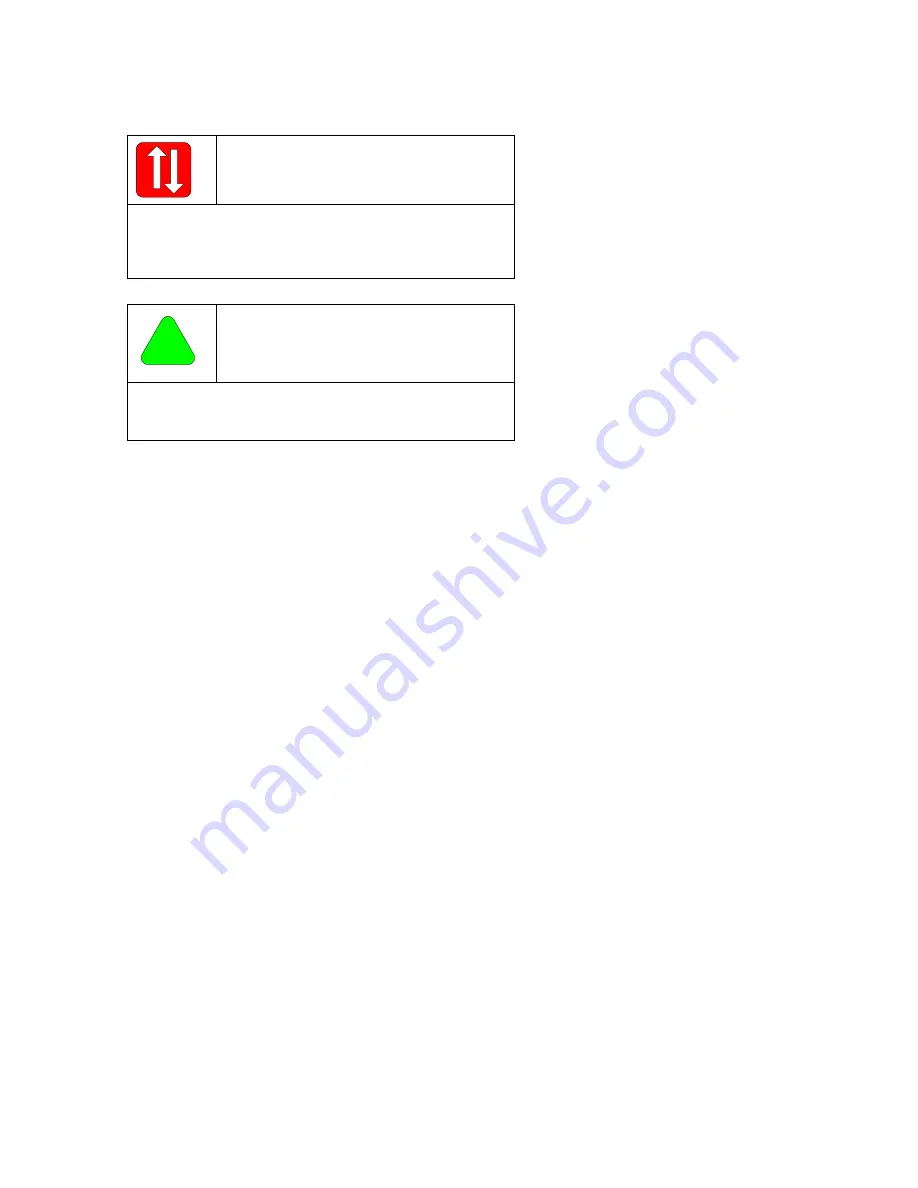
PS200 Configuration & Operation Guide
SINGLE PUMP PROCESS
Page 22
Recommended Step:
Parameter Upload
See KEYPAD USE
Save your parameters in the keypad. In the unlikely event
that the PS200 parameters are lost, the keypad can be used
to restore the configuration. It can also be used to program
sister units that use the same or similar program settings.
!
Recommended Option:
Drive Locking
See OPTIONS & FEATURES
The keypad can "locked" to prevent unauthorized personnel
from making operational changes or changes to the
parameter groups. See LOCKING in OPTIONS & FEATURES.
Summary of Contents for PumpSmart PS200
Page 1: ... PUMPSMART CONTROL SOLUTIONS PS200 Version 4 0 Configuration Operation Guide ...
Page 2: ......
Page 4: ......
Page 8: ......
Page 26: ......
Page 72: ......
Page 105: ......
Page 119: ......
Page 146: ...PS200 Configuration Operation Guide APPENDIX A 3 PARAMETER LISTING Page 143 ...
Page 147: ......
Page 158: ......