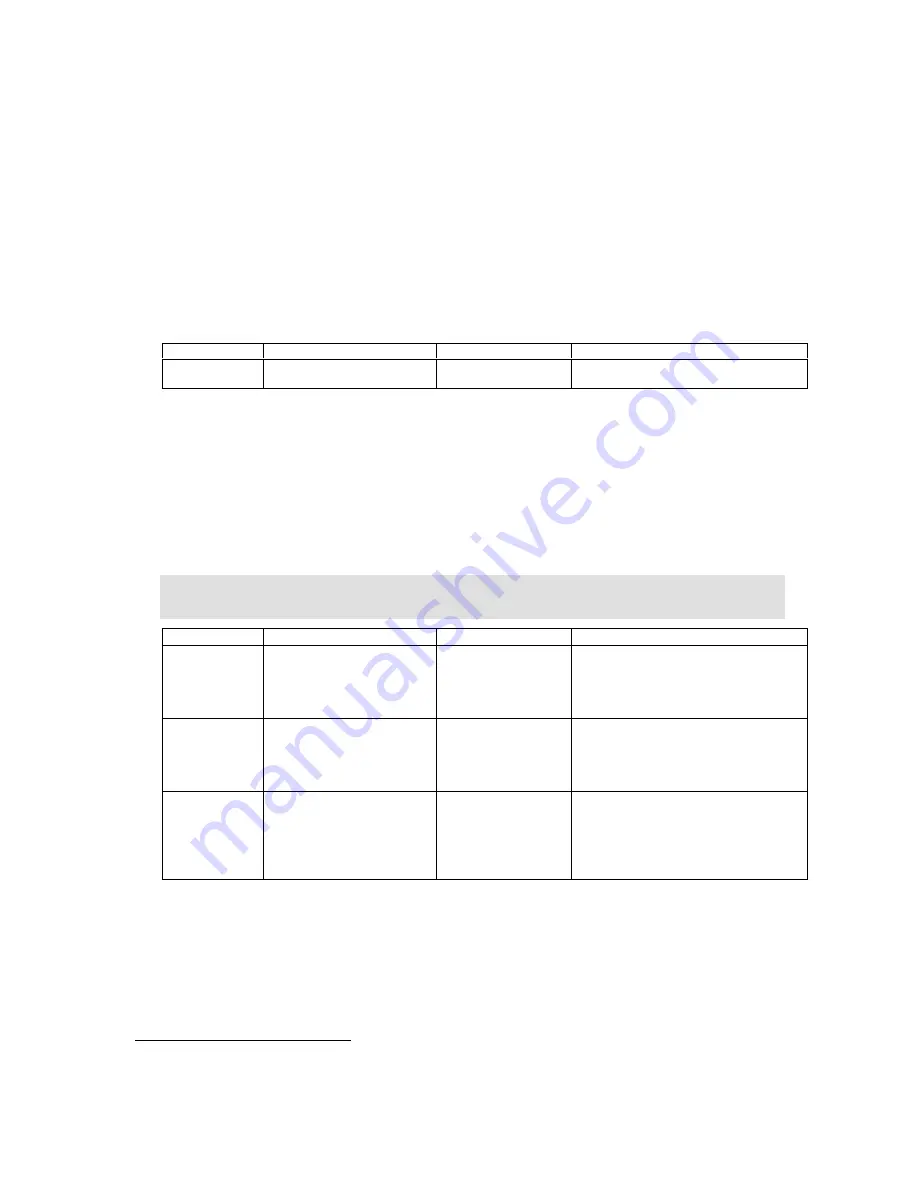
PS200 Configuration & Operation Guide
OPTIONS & FEATURES
Page 84
Permissive
The PS200 digital input DIIL has been configured as a drive permissive switch and must be closed in order for the
drive to run. There is no parameter entry available to defeat this permissive. If the switch is open, a warning “RUN
DISABLED” will appear on the keypad display.
If your operating requirements do not require drive permissive switches, DIIL may be wired as permanently closed.
Priming Delay
This feature is designed to allow self-priming pumps sufficient time to prime themselves before the PumpSmart
Pump Protection logic becomes active. The delay period is applied only if the pump is being started from a zero-
speed condition. Once the priming delay is complete, the PROTECTION DELAY (25.03) becomes active, if set.
Parameter
Name
Value/Range
Notes
14.09
PRIMING DELAY
0-6000 Seconds
0
[default]
Pump Wear Monitor PWM
1
The PS200 can detect decreases in pump performance due to wear and/or blockage of the hydraulic passageways
of the impeller and casing. When a decrease in performance is detected, PumpSmart can issue a warning so that
refurbishment of the pump can be planned appropriately. The performance monitoring is not affected by changes
in the system resistance (e.g. closing of discharge valve) or changes in suction pressure.
When the PWM option is selected, PumpSmart will perform a performance characterization of the pump by
increasing speed and monitoring the process condition over the range of possible operating conditions. The
characterization results are best when the system is in a normal operating condition. When performing a baseline
check, the pump should be at or near its normal operating conditions with system temperature relatively stable.
NOTE – Normal process control is suspended during the PWM characterization. The characterization takes
approximately 2 minutes to complete. During this process, a warning message “BASELINE RUN” will be displayed
on the keypad.
Parameter
Name
Value/Range
Notes
27.01
PMP PERF BASELINE
1
ST
BASELINE
[default]
NEW BASELINE
Selecting NEW BASELINE will result in a
new PWM characterization being
performed. Selection of this parameter
is not required for initial
characterizations.
27.02
PMP WEAR MONITOR
DISABLED
[default]
10% DEGRADED
15% DEGRADED
20% DEGRADED
25% DEGRADED
Selecting a degradation level engages
the PWM and automatically begins a
characterization.
27.23
HRS BTWN PWM CHK
0-9999
24 HRS
[default]
This parameter defines the period of
time between wear checks. During a
check, PumpSmart will increase and
decrease speed by approximately
r
5%
of process variable for several seconds
before returning to normal PI Control.
PWM Limitations – The following conditions are required for accurate PWM operation.
1.
Specific gravity changes must be less than
r
5% unless a pressure transmitter is used.
2.
Viscosity changes must be less than
r
5%.
3.
A pressure or flow transmitter that is directly related to the discharge conditions of the pump is
required. This is most common in pressure/flow operating modes. If an application does not have a
pressure/flow transmitter (e.g. Level applications), one can be provided and configured using any
available analog input.
1
US Patent No(s). 6648606 & 6564627
Summary of Contents for PumpSmart PS200
Page 1: ... PUMPSMART CONTROL SOLUTIONS PS200 Version 4 0 Configuration Operation Guide ...
Page 2: ......
Page 4: ......
Page 8: ......
Page 26: ......
Page 72: ......
Page 105: ......
Page 119: ......
Page 146: ...PS200 Configuration Operation Guide APPENDIX A 3 PARAMETER LISTING Page 143 ...
Page 147: ......
Page 158: ......