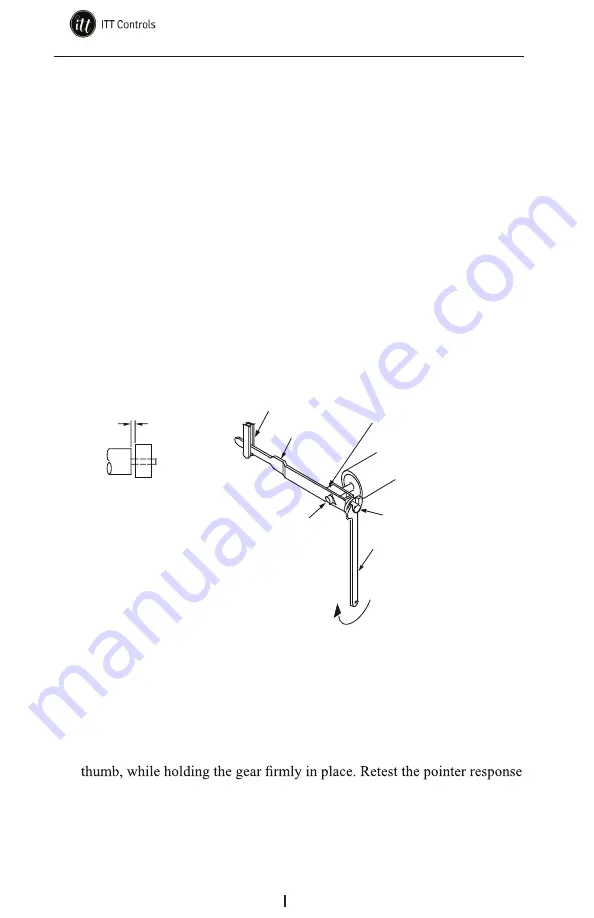
www.ittcontrols.com
contact@ittcontrols.com
16
Section 3
Model 581A Differential Pressure Switch
6. Release pressure. Set the pointer to zero, by slipping the pointer on the
hub, per
Calibration Check
, step 2,
page 12
.
7. Repeat steps 4 and 5, as necessary, to obtain the correct zero/full-scale.
8. Apply 50% DP. If the pointer indicates 50%, proceed to step 9. If the
pointer does not indicate 50% scale, adjust linearity as follows.
a. Loosen the drive arm screw (Figure 3.5) and move the arm to shift
the pointer in the direction of the error a distance of about 10 times
the linearity error.
b. To prevent interference, check to see that the drive arm clears the
end of torque-tube housing by approximately 0.030 in. before re-
tightening the drive arm screw.
c. While supporting the block/shaft, tighten the clamp screw until it is
snug to the shaft.
d. Still supporting the block/shaft, tighten the clamp screw an addition-
al 1/3 to 1/2 turn. (This screw can normally turn one full revolution
before breaking.)
e. Perform the Drive Arm Tightness Test described on
page 17
.
1/8” WRENCH
(PN 9A-0163-0044C)
CLAMP SCREW
DRIVE ARM
LINK
SINTERED
CLAMP BLOCK
TO TIGHTEN
.03 (approx)
M199
SHAFT
Figure 3.5—Drive arm to torque tube connection
9. Release pressure and reset the pointer to zero. Check the span. If the gear
in the movement reaches a limit of travel as a result of linearity adjust-
ment (step 8), slip the range arm along the gear approximately 5 degrees
from the normal 37.5 degree angle to approximately 43 degrees (see
step 3). To slip the range arm, apply pressure to the range arm with the
at 50%, 0%, and 100% of full-scale differential pressure, and adjust the
linkage until the readings are acceptable.
10. Apply 0%, 25%, 50%, 75%, 100%, 75%, 50%, 25%, and 0% of full-scale
differential pressure consecutively to the instrument without overshoot.