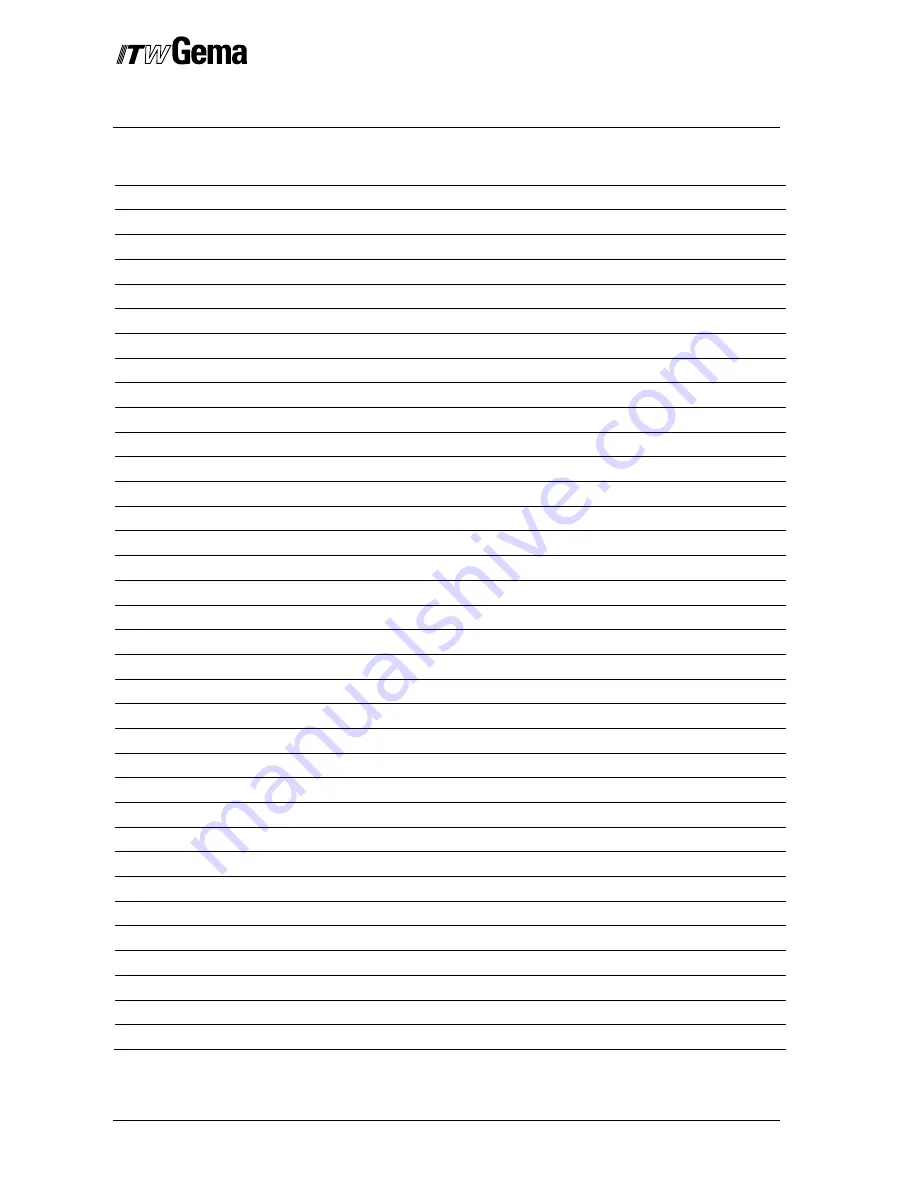
V
05/10
32
Spare parts list
OptiFlex B manual coating equipment
OptiFlex B manual coating equipment - spare parts list
1 Wheel
shaft
1000 453
2
Rubber wheel - Ø 200 mm
260 592
3
Lock washer - Ø 26 mm
1000 944
4
Swivel wheel - Ø 50 mm
260 606
5 Spacing
ring
375 624
6
Rubber damper- Ø 20x25 mm, M6/2a 43sh
246 000
7
Fluidizing/suction unit (see corresponding spare parts list)
8 Stop
plate
1000 513
9
Countersunk Allen screw - M6x40 mm
1002 953
10
Countersunk Allen screw - M6x20 mm
1002 992
11 Handle
bar
1002 623
12
CG07 gun control unit - complete (see corresponding user manual)
13 Hose
holder
1000 699
14
Hexagon shakeproof nut - M6
244 430
Cable connection fitting for vibrator cable - M16/1/6-10.5 mm, brass (not shown)
265 780
17
Cable plug - 4 pins, male
206 466
18
Countersunk Allen screw - M6x30 mm
1002 952
19
Grounding cable - complete
301 140
20
Plastic hose - Ø 8/6 mm
103 756
*
21
Vibrator motor - 220-240 VAC, 50 Hz
1001 748
Vibrator motor - 120 VAC
389 382
22
IG02-V Injector - complete (see corresponding user manual)
23 Gun
retainer
1003 076
24
Spare parts set - MB02, consisting of:
1002 015
Insert sleeve PTFE
377 724
Injector plug gauge
393 380
Fluidizing pad - 1/8"a
237 264
O-ring - Ø 16x2 mm
231 517
Fuse - 4 AT
262 897
Fuse - 2 AT
221 872
Fuse - 0.1 AT
229 520
Cable tie - L=100x2.5 mm
200 719
25
Ribbed cylinder screw - M10x20 mm
260 584
26
Hexagon ribbed cylinder screw - M8x16 mm
261 793
27
Short instruction sheet OptiStar CG07
1002 060
28
Program table sheet OptiStar CG07
1002 063