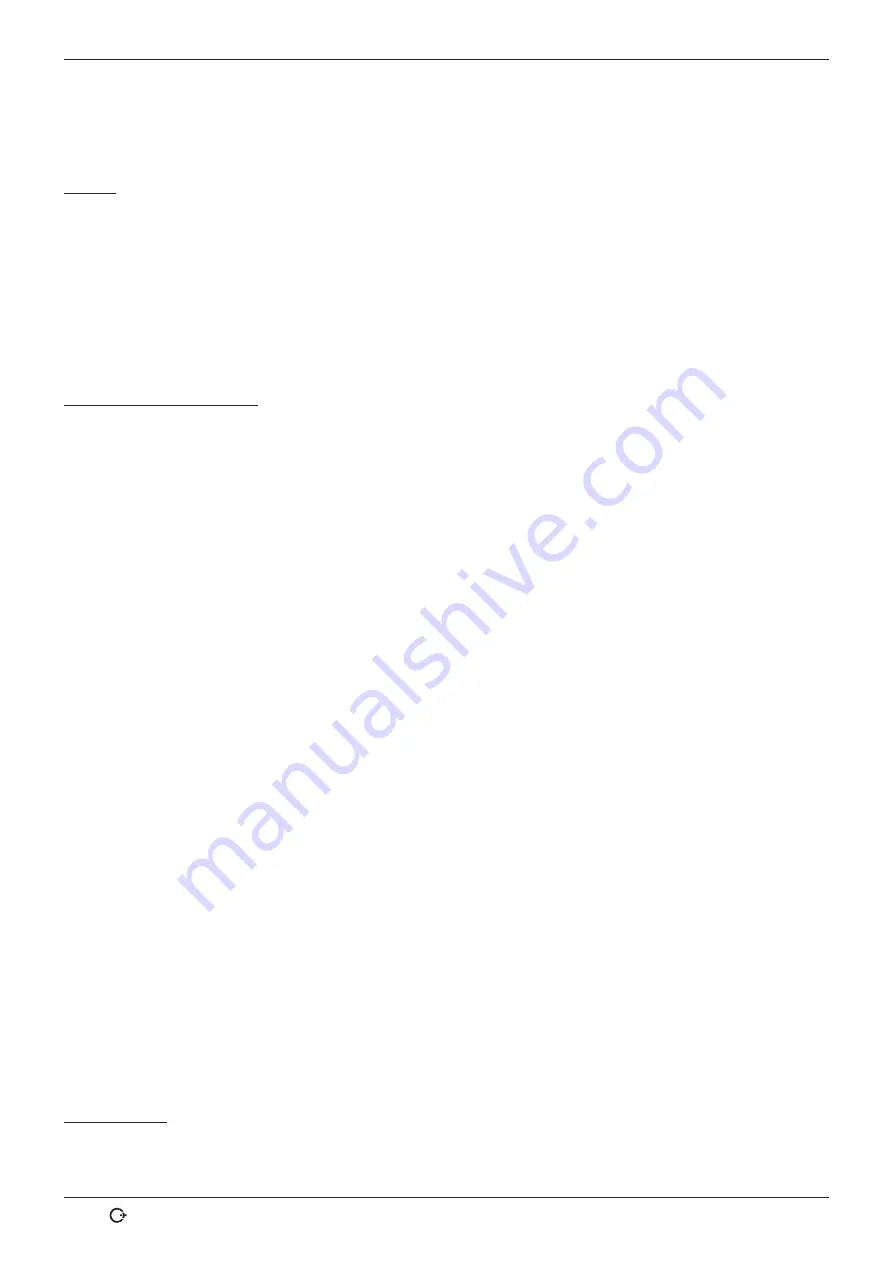
Service and troubleshooting
ORBIMAT CA
| Operating instructions
68
orbitalum tools
GmbH, D-78224 Singen, www.orbitalum.com, Tel. +49 (0) 77 31 792-0
(09.03.15) OW_ORBIMAT_CA_BA_871060202_04_EN
If the sulfur content is reduced further (approx. 0.005% or lower), the so-called "convection streams" in the melt pool
(in simplified terms) tend to flow more horizontally and on the surface. This leads to widening of the seam without
penetration.
Remedy
X
Carry out a material analysis for confirmation.
X
Change material if appropriate (it may be sufficient to just change the batch).
X
Weld with filler wire so that a correspondingly higher sulfur content arises in the melting pool thanks to the wire.
9.2.4
Uneven seam/hole formation at the end of welding
Do the weld seams look as if the torch "moved sideways" in an uncontrolled fashion?
Does the seam not remain centered over the joint, instead pulling to one side or moving "back and forth"?
Possible causes and remedies
• When welding pipe and molded part: "Marangoni effect".
The sulphur content tends to be high with materials for machining. The effect is seen on one side of the pipe joint
with the result of a seam which is heavily asymmetrical to the joint. The root inside the pipe is then often formed
fully outside and next to the pipe joint.
• If the seam regularly wanders off to the side only in one or two places when welding, the corresponding different
material composition in the base material and in the seam is responsible for the effect with a longitudinal pipe seam.
X
Shorten arc gap somewhat.
• Gas quantity set too high (weld gas or forming gas):
If an excessive gas quantity is set for small cassette heads (especially OW12), turbulence occurs in the pocket,
which can lead to an extremely irregular arc. The same applies if too much forming gas is used and it comes out at
the weld joint at relatively high pressure.
X
Regulate gas quantity.
• Excessively high forming gas pressure:
Heavy outward swelling of the seam with a type of "hollow groove" inside the pipe. Hole formation also often oc-
curs at the end of welding if the excessive pressure of the gas can only be "relieved" over the liquid melt pool. With
cassette weld heads in particular, liquid metal dripping in the head can cause considerable consequential damage.
X
Regulate forming gas pressure.
• Worn electrode without proper grinding:
The "attachment" point of the arc often "dances" back and forth on the electrode. With a poor-quality electrode,
lateral migration of the arc from the electrode can be observed now and then. The reason for this can be that the
alloy components in the base material are not evenly distributed.
X
Grind electrode properly.
9.2.5
Ignition problems
The ignition generator generates ignition pulses with a voltage of up to 8,000 V. These ignition pulses can be a consid-
erable source of disruption (especially for computer-based control). The ignition pulses are introduced to the electrode
with high-voltage insulation via the hose assembly. Upon ignition, a current flow of potentially several hundred am-
peres can arise in the weld circuit and be correspondingly disruptive (magnetic fields around the conductor and other
high-frequency fields). The machine controller is shielded from these disruptive fields. If problems are occurring with
the arc ignition, malfunctioning of the computer or a corresponding defect in the system cannot be ruled out.
Information on possible electrical fault sources: see chap. 9.3, p. 69: "List of error messages".
Possible causes
• Poor electrode quality, worn or scaled electrode.
• Poor ground contact (open head to ground terminal).