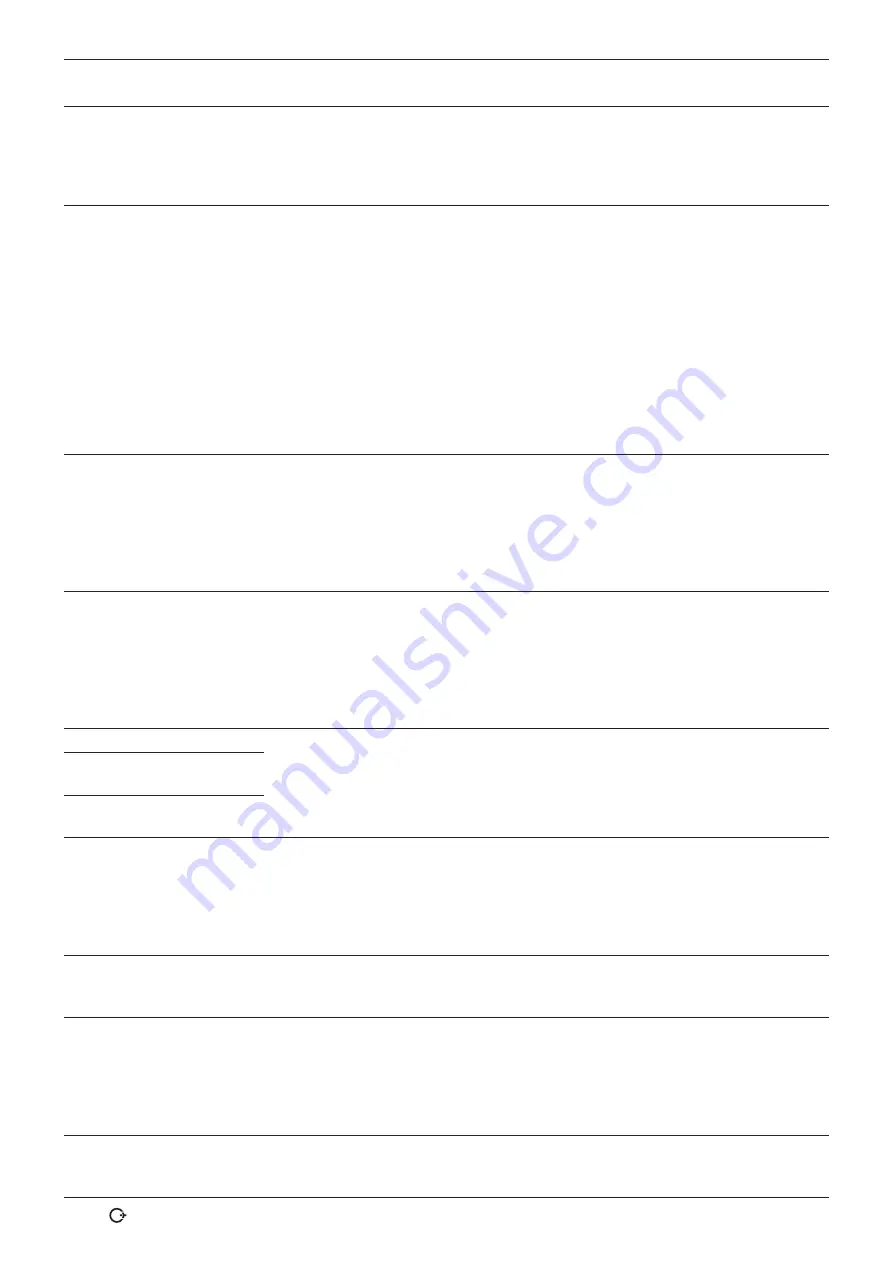
Service and troubleshooting
ORBIMAT CA
| Operating instructions
72
orbitalum tools
GmbH, D-78224 Singen, www.orbitalum.com, Tel. +49 (0) 77 31 792-0
(09.03.15) OW_ORBIMAT_CA_BA_871060202_04_EN
35
An error entry was created in the error log. The new error entry appears in the display
in English. The error log can be read out for service purposes.
View error log:
X
Enter the letter sequence ERR on the external keyboard.
[
Do
not
delete error log, as this information is required for service purposes.
36
File with inverter char-
acteristic cannot be
opened!
Default values are
used.
File with characteristics cannot be read. Current adjustment of the machine ineffective.
A file generated during current adjustment is stored on the CF card of the machine:
During calibration, a digital adjustment is carried out, where the differences between
the setpoint and actual values and the measured values of a calibrated measuring unit
can be recorded point by point and saved in a file.
If the file is not readable, the error coefficients are given the default value (1).
This makes the current adjustment carried out by Orbitalum ineffective.
X
For applications which provide data monitoring and actual value recording, stop
working with the machine.
X
Contact Orbitalum to restore the calibration data.
37
Auto programming
failed!
The auto programming
file may be missing or
corrupt.
Auto programming error.
Causes:
• The combination of pipe diameter and wall thickness lie outside the value range of
auto programming (e.g. wall thicknesses over 4 mm)
X
Use other parameters.
• Data of the database on the internal CF card not present or not readable.
X
Contact Orbitalum to restore the data.
38
External storage me-
dium not found!
The card reader may
not have a card in-
serted
Access to external memory card not possible.
X
Check whether the memory card is detected by the system (diskette symbol in the
display).
X
Reset the card reader: Disengage card reader, remove it from the slot and insert it
again.
X
Check whether the memory card is defective or has an unreadable format.
X
Contact Orbitalum service if the problem cannot be resolved.
39
Error when saving log
Software conflicts due to damaged files or files with unreadable contents.
The message is followed by the error in "plain text" (see messages 18 through 28) or
as a two-digit number.
40
Procedure file cannot
be opened!
41
Log file cannot
be opened!
42
Some currents are set
too high.
They cannot be
achieved with a 115 V
mains voltage!
(OM 165 CA only)
OM 165 CA only.
Machine connected to mains network of less than 200 V AC. The maximum weld cur-
rent is limited to 100 A. Procedure with higher weld current has been started.
43
An error occurred while
reading the file
FAILURES.TXT!
After entering ERR on the external keyboard: Internal error log ("Failures.txt" file)
is not present or is damaged.
44
No weld head con-
nected!
Procedure started, no weld head connected to the machine.
Weld head is connected?
• Weld head not encoded
• Voltage supply to weld head defective. The operating buttons in the weld head are
not working.
X
Contact Orbitalum service.