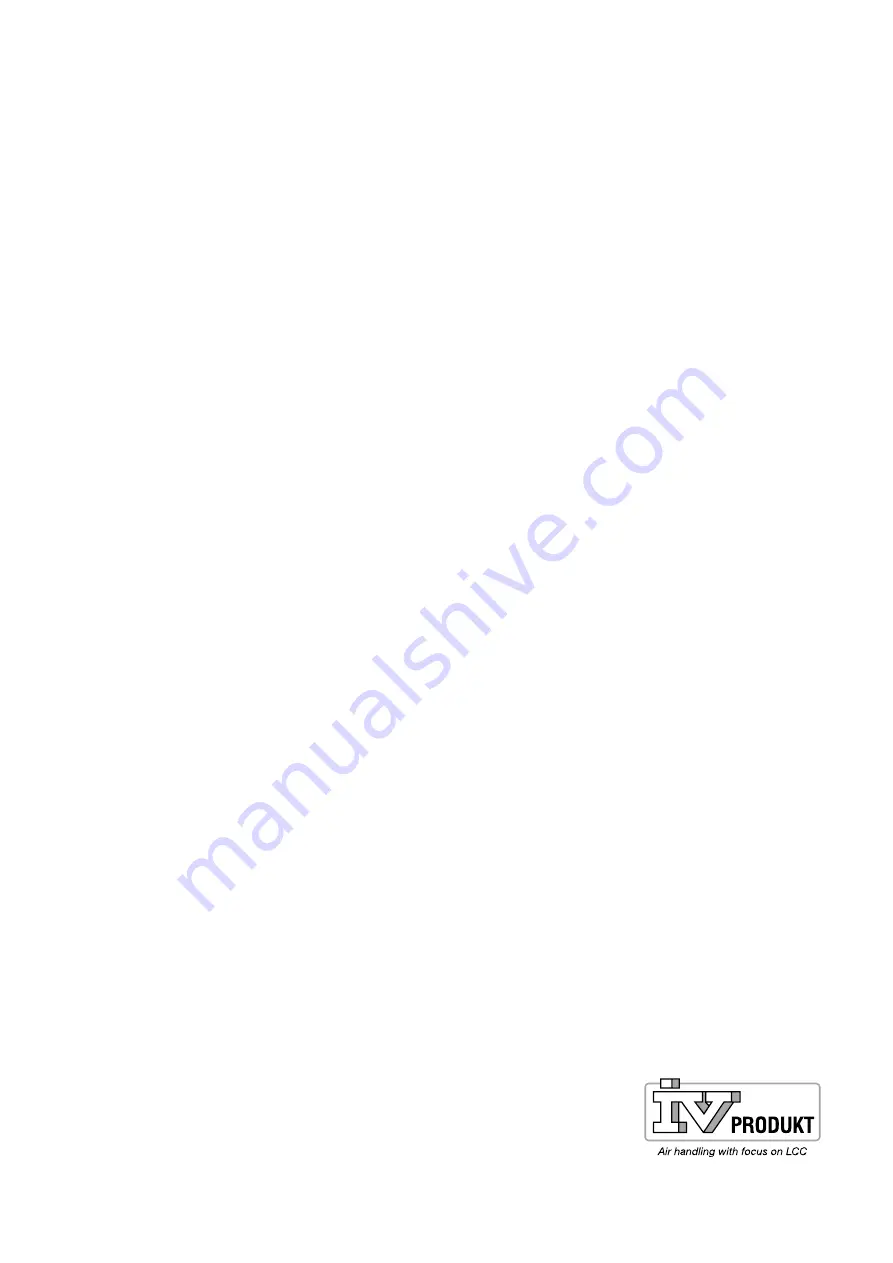
Table of Contents, cntd
5.2 Actions in case of standstill
.............................................................................................
5.4 Cooling Status – Cooling unit, size 04
.....................................................................
5.5 Cooling Status – Cooling unit, size 06-12
.............................................................
5.6 Cooling Status – Cooling unit, size 16-21
.............................................................
6.3 Rotary heat exchanger (code ATRR)
.........................................................................
6.4 Counter-flow exchanger (code ATMM)
...................................................................
6.5 Air heater water (code ATEV)
...........................................................................................
6.6 Air heater Electric (code ATEE, ATET-EV)
...............................................................
6.7 Air cooler water (code ATET-VK)
...................................................................................
6.9 Damper (code ATET-UM, ETET-UM, ETET-TR, ATET-09)
6.10 Sound attenuator (code ETET-LD)
.............................................................................
.................................................................................................
7 Alarm management and troubleshooting
7.1 Cooling unit – sizes 04 and 16-21
...............................................................................
....................................................................................................