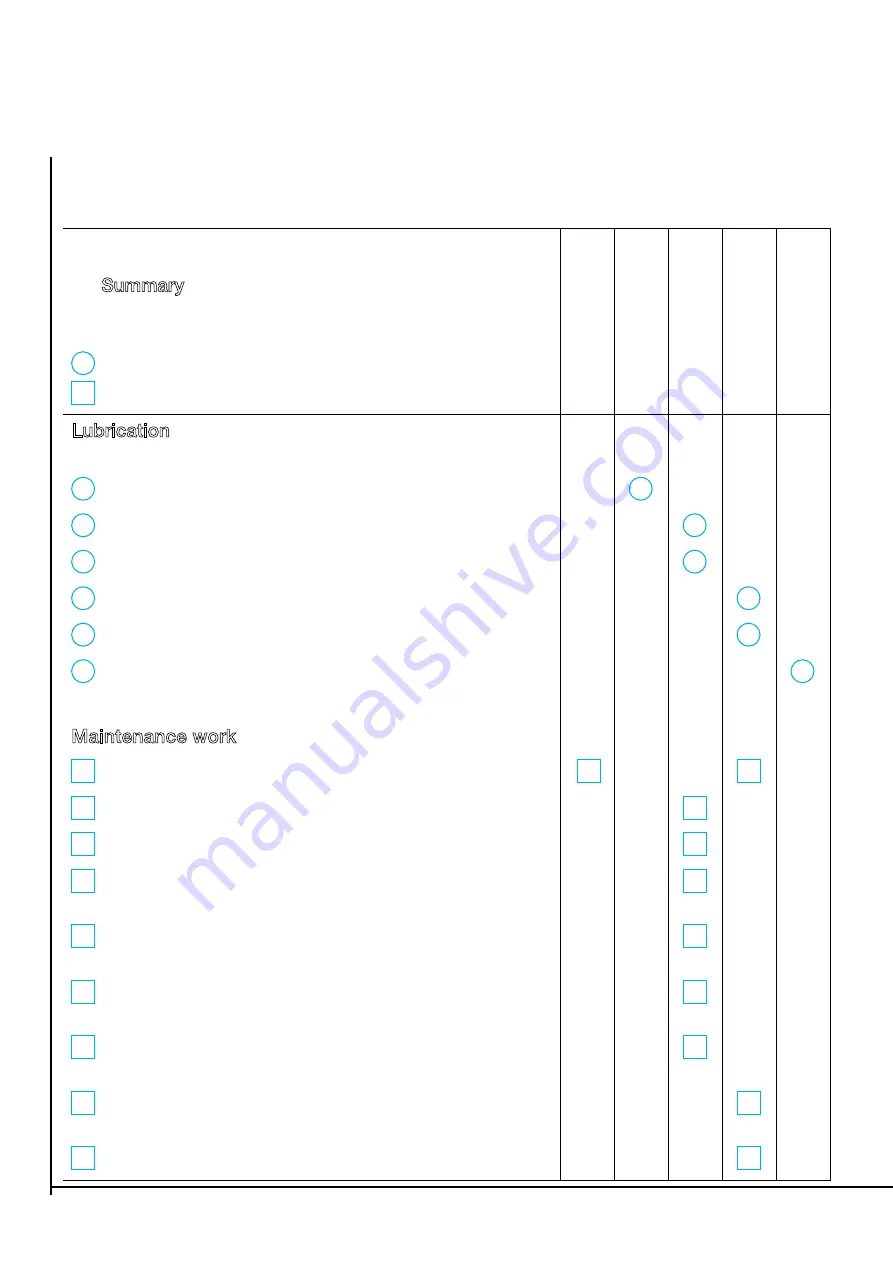
www.metsjo.se
Ver. 2011-10
16
7
BPW trailer axle
with butterfly cam brakes
BPW trailer axle
with flat cam brakes
BPW trailing steering axle
BPW trailer axle
with wedge�type brake
English
6
Lubrication and maintenance works
Summary
Detailed description on pages 8 � 18
Lubrication
Maintenance works
Lubrication
with BPW special longlife grease (ECO�Li 91)
1
Steering pivot bearings, top and bottom
2
Locking cylinder ends on steering axles
3
Outer and inner brake camshaft bearings
4
Slack adjuster
5
ECO�Master automatic slack adjuster
6
Change grease in wheel hub bearings,
check taper roller bearings for wear
Maintenance work
1
Check that wheel nuts are tight, retighten if necessary.
2
Check hubs for bearing play, adjust if necessary.
3
Check brake linings.
4
Check the brake adjustment on the brake lever,
adjust if necessary.
5
Check the brake adjustment on the slack adjuster,
adjust if necessary.
6
Check brake adjustment on wedge�type brakes,
adjust if necessary.
7
Check brake adjustment on Backmat cam brakes,
adjust if necessary.
8
Check brake adjustment on the automatic
slack adjuster, adjust if necessary.
9
Check the operation of the automatic slack adjuster.
After the first laden jour
ney
Every 40 hours in operation
Every 200 hours in operation
Every 500 hours in operation (annually)
BPW trailer axles
Every 1000 hours in operation (annually)