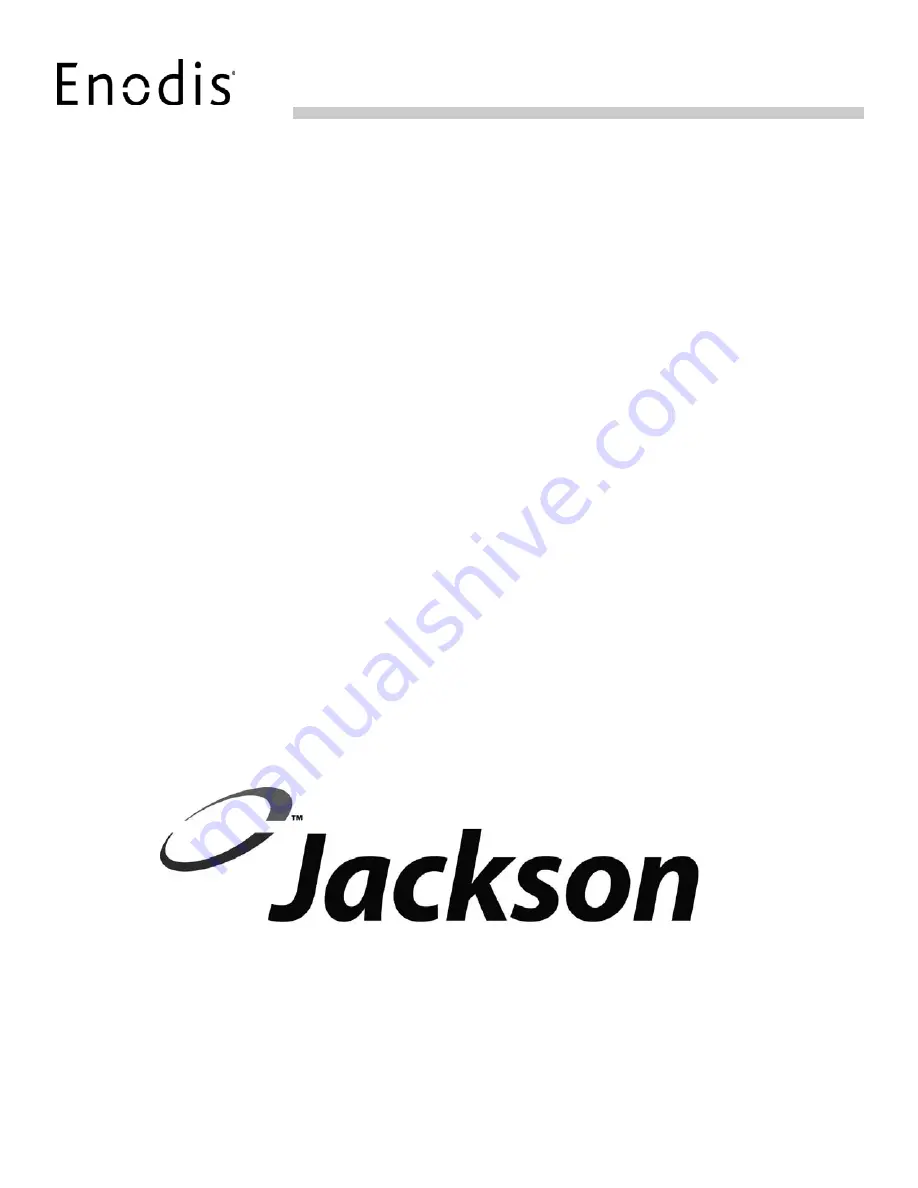
INSTALLATION/OPERATION &
TECHNICAL MANUAL
FOR JACKSON MODELS:
Jackson MSC LLC.
P.O. Box 1060
Barbourville, KY. 40906
(606) 523-9795
Fax: (606) 523-9196
www.jacksonmsc.com
AJ-44 RACK CONVEYOR DISHMACHINE SERIES
September 29, 2007
P/N 07610-001-76-22 (Revision H)
AJ-44CE
AJ-44CEL
AJ-44CGP
AJ-44CS
AJ-44CSL
AJ-66CE
AJ-66CEL
AJ-66CGP
AJ-66CS
AJ-66CSL
AJ-80CE
AJ-80CEL
AJ-80CS
AJ-80CSL