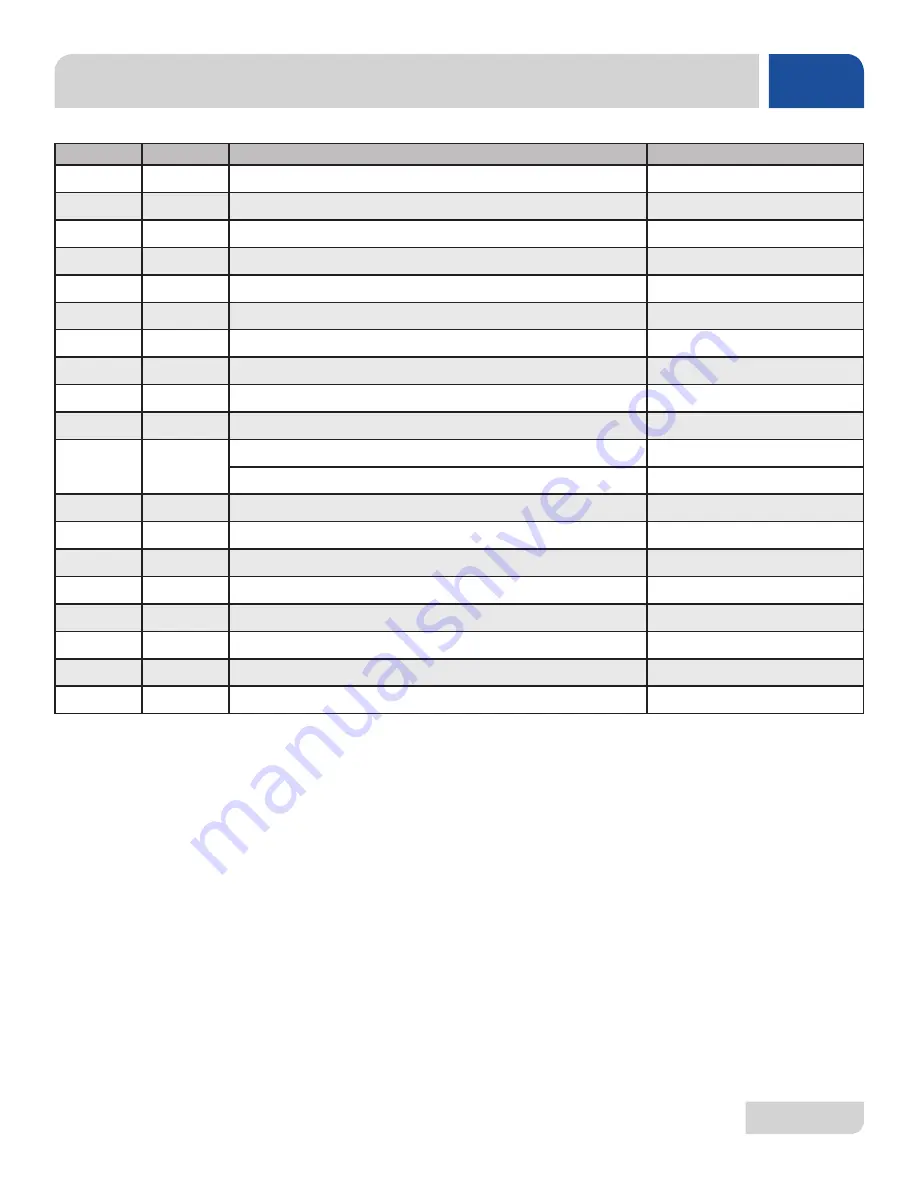
44
07610-003-62-15-Q
PARTS
CONVEYOR & DRIVE SYSTEM
ITEM
QTY
DESCRIPTION
PART NUMBER
1
1
Cylinder
05700-003-49-10
2
1
Rack
09330-003-45-66
3
3
Guide Block
09330-003-51-17
4
1
Strainer Weldment
05700-003-59-93
5
1
Drain Defelctor, Wash
05700-003-48-99
6
1
Plate, Skid
09330-003-58-52
7
1
Drive Gear
09330-003-58-32
8
1
Washer
05330-003-41-75
9
1
Extension Spring
05340-003-41-83
10
1
Gear Motor Box
05700-003-48-87
11*
1
Gear Motor (Delta 1200)
06105-003-44-23
Gear Motor (Delta 115)
06105-004-26-30
12
1
Gear Motor Box Cover
05700-003-48-57
13
2
Lock Nut, 6-32
05310-373-03-00
14
1
Switch Mounting Bracket
05700-003-60-13
15
1
Liquidtite Fitting
05975-011-49-03
16
1
Limit Switch
05930-303-38-00
17
2
Limit Switch Mounting Screws
05305-171-10-00
18
1
Activator Weldment
05700-003-58-50
19
1
Limit Switch Actuator
05700-003-58-54
Summary of Contents for DELTA 115
Page 2: ......
Page 6: ......
Page 53: ...46 07610 003 62 15 Q SCHEMATICS DELTA 115 ...
Page 54: ...47 07610 003 62 15 Q SCHEMATICS DELTA 1200 ...
Page 55: ......