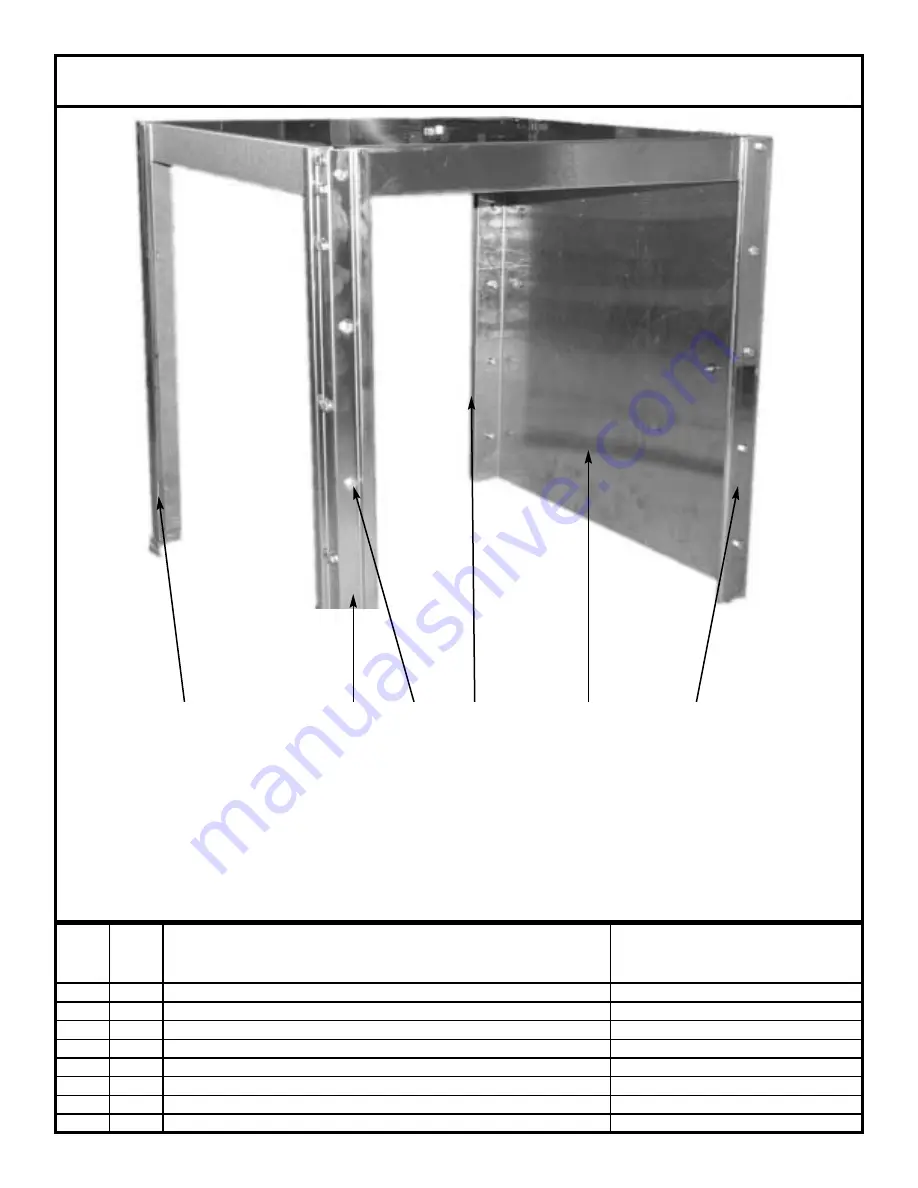
HOOD ASSEMBLY
24
ITEM
QTY
DESCRIPTION
MFG NO.
01
1
Double Door Guide, Left Front
5700-021-33-20
02
1
Double Door Guide, Right Front
5700-021-33-19
03
28
Screw, 1/4"- 20 x 1/2"
5305-274-02-00
03
28
Washer, s/s 1/4" ID
5311-174-01-00
03
28
Locknut, 1/4"- 20 s/s Hex w/Nylon Insert
5310-374-01-00
04
1
Door Guide, Left Rear
5700-021-84-71
05
1
Hood Weldment
5700-002-18-76
06
1
Door Guide, Right Rear
5700-021-84-70
02
03
05
01
04
06