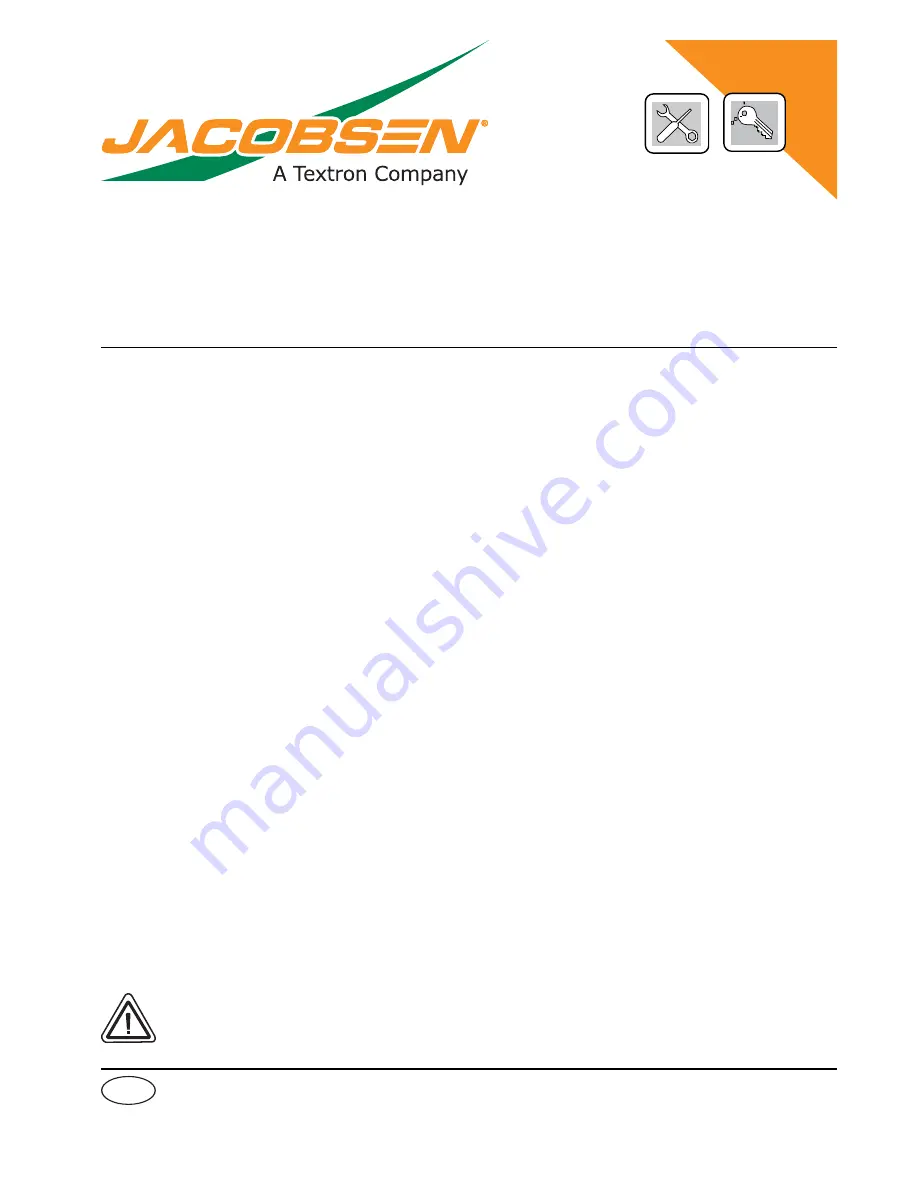
Safety, Operation & Maintenance Manual
WARNING: If incorrectly used this machine can cause
severe injury. Those who use and maintain this machine
should be trained in its proper use, warned of its dangers and
should read the entire manual before attempting to set up,
operate, adjust or service the machine.
GB
United
Kingdom
RJL 100 February 2010
Series: EJ - 26" Cutting Units - Engine type: Kubota D1105-E - Product code: TR30001
Series: FG - 26" Cutting Units - Engine type: Kubota D1105-E - Product code: TR30002
Jacobsen TR3
24731G-GB (rev.4)
Summary of Contents for TR3 EJ Series
Page 2: ...2010 Ransomes Jacobsen Limited All Rights Reserved...
Page 33: ...en 33 JACOBSEN TR3 SAFETY OPERATORS MAINTENANCE MANUAL 7 OPERATION...
Page 35: ...en 35 JACOBSEN TR3 SAFETY OPERATORS MAINTENANCE MANUAL 8 MAINTENANCE LUBRICATION...
Page 73: ...en 73 JACOBSEN TR3 SAFETY OPERATORS MAINTENANCE MANUAL 11 TROUBLESHOOTING...
Page 74: ...en 74 JACOBSEN TR3 SAFETY OPERATORS MAINTENANCE MANUAL 12 1 HYDRAULIC CIRCUIT 12 SCHEMATICS...
Page 84: ......
Page 85: ......