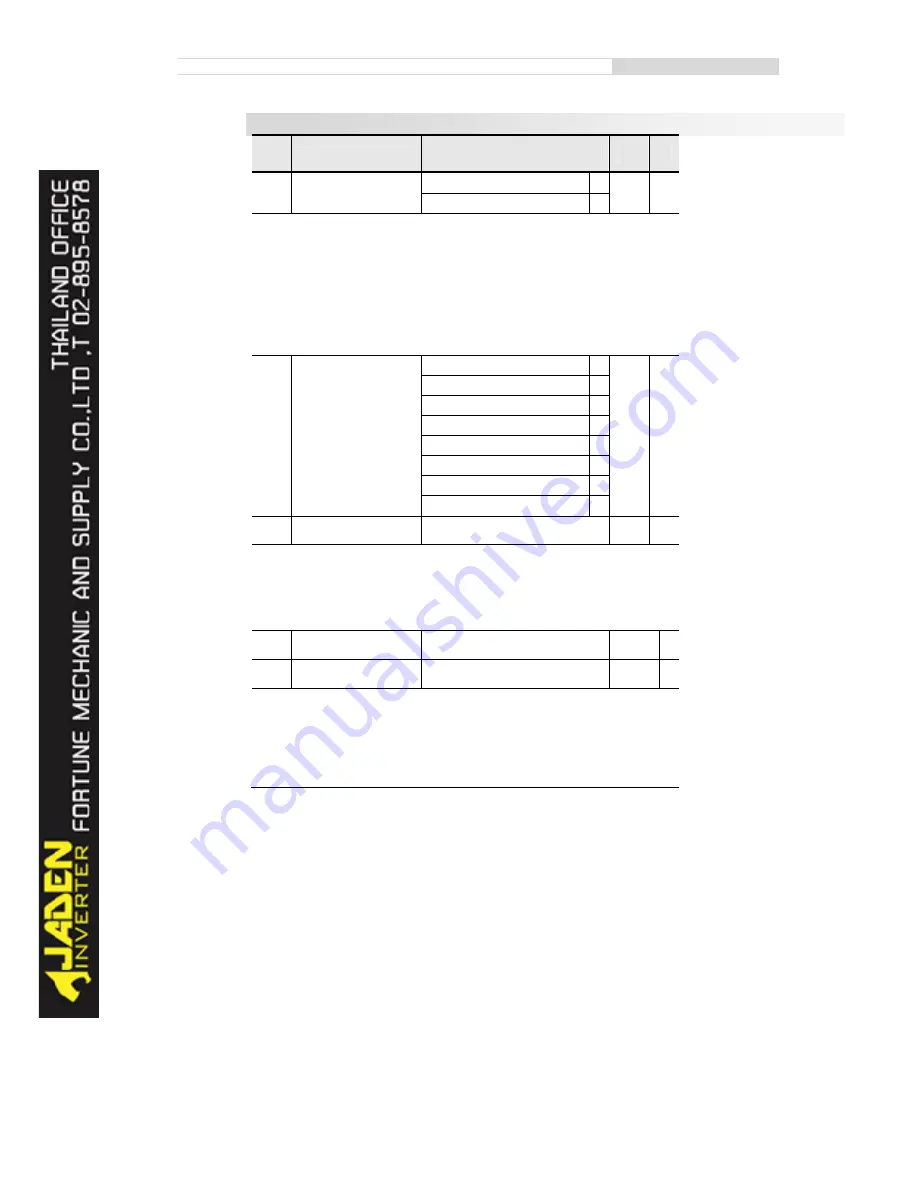
-119-
4.18 Torque control parameters:B0.00-B0.08
Code
Description
Setting range
Default
Restric
tions
B0.00
Speed/Torque control
selection
Speed control
0
0
★
Torque control
1
It is used to select the Inverter's control mode: speed control or torque control.
The DLB1 provides DI terminals with two torque related functions, function 29 (Torque control
prohibited) and function 46 (Speed control/Torque control switchover). The two DI terminals need
to be used together with B0.00 to implement speed control/torque control switchover.
If the DI terminal allocated with function 46 (Speed control/Torque control switchover) is OFF,
the control mode is determined by B0.00. If the DI terminal allocated with function 46 is ON, the
control mode is reverse to the value of B0.00.
However, if the DI terminal with function 29 (Torque control prohibited) is ON, the Inverter is
fixed to run in the speed control mode.
B0.01
Torque setting source in
torque control
Digital setting(B0.03)
0
0
★
AI1
1
AI2
2
AI3( keyboard potentiometer)
3
Pulse
4
Communication setting
5
MIN(AI1, AI2)
6
MAX(AI1, AI2)
7
B0.03
Torque digital setting in
torque control
-200.0%~200.0%
150%
☆
B0.01 is used to set the torque setting source. There are a total of eight torque setting sources.
The torque setting is a relative value. 100.0% corresponds to the Inverter's rated torque. The
setting range is -200.0% to 200.0%, indicating the Inverter's maximum torque is twice of the
Inverter's rated torque.
If the torque setting is positive, the Inverter rotates in forward direction. If the torque setting is
negative, the Inverter rotates in reverse direction.
B0.05
Forward maximum
frequency in torque control
0.00Hz~ maximum frequency(P0.10)
50.00Hz
☆
B0.06
Reverse maximum
frequency in torque control
0.00Hz~ maximum frequency(P0.10)
50.00Hz
☆
These two parameters are used to set the maximum frequency in forward or reverse rotation in
torque control mode.
In torque control, if the load torque is smaller than the motor output torque, the motor's
rotational speed will rise continuously. To avoid runaway of the mechanical system, the motor
maximum rotating speed must be limited in torque control.
You can implement continuous change of the maximum frequency in torque control
dynamically by controlling the frequency upper limit.
Summary of Contents for DLB1-0D40S2G
Page 11: ...11 Graph 1 722 30KW product outline dimensions Graph 1 837 55KW product outline dimensions...
Page 12: ...12 Graph 1 875 110KW product outline dimensions Graph 1 9 132 160KW product outline dimensions...
Page 14: ...14 2 Wirings 2 1 Standard wiring diagrams Graph 2 8 0 4 18 5KW inverter wiring diagram...
Page 15: ...15 Graph 2 922 400KW inverter wiring diagram...
Page 159: ...159...