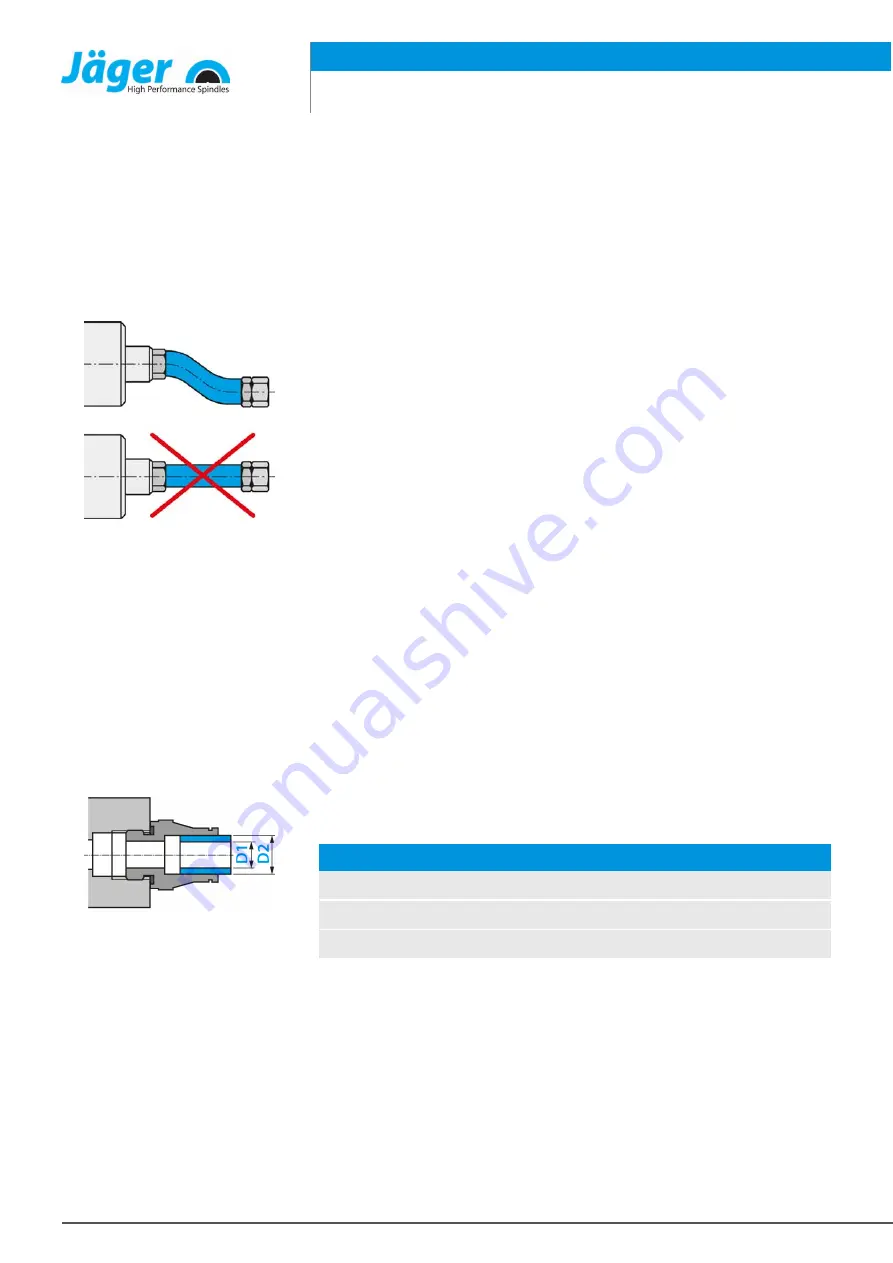
Installation
Item no. 10301166, Revision 03
24 ( 40 )
8
Installation
Before installation:
Ü
Check the HF spindle for damage and ensure that it is complete.
If the HF spindle has been stored for a long period:
Ü
Carry out all steps in the Commissioning after storage section.
8.1
Installing the HF spindle
Connect media and cables with a
flexible connection.
Complete the following steps in sequence to install the HF spindle:
Ü
Remove the sealing plugs that protect the connections against damage
and contamination during transportation.
Ü
Instead of these sealing plugs, install the appropriate hose fittings.
Ü
Install the corresponding hoses in the hose fittings
Ü
Make sure that the connections are flexible and free of strain.
Ü
Seal all connections for compressed air axially in relation to the tightening
direction.
Ü
If the HF spindle is equipped with sealing air:
Ä
Make sure that no air flow can occur in the bearing area.
Ä
Always use sealed cable boxes when connecting electrical lines.
Ü
Mount the HF spindle on the machine.
Ü
Connect the hoses to the connection of the respective media.
Ü
Remove the protective cap that protects the shaft against damage and
contamination during transportation.
Ü
Connect the connector of the operating connection lines to the relevant
connection of the HF spindle and to the frequency converter.
Ü
Lock the connectors.
8.2
Diameter of media supply line
Ü
The nominal size of the media supply lines can be found in the following
table:
DN
Medium
D1
D2
2.8
Compressed air
2.8 mm
7
/
64
"
4 mm
5
/
32
"
4
Compressed air
4 mm
5
/
32
"
6 mm
15
/
64
"
6
Compressed air
6 mm
15
/
64
"
8 mm
5
/
16
"