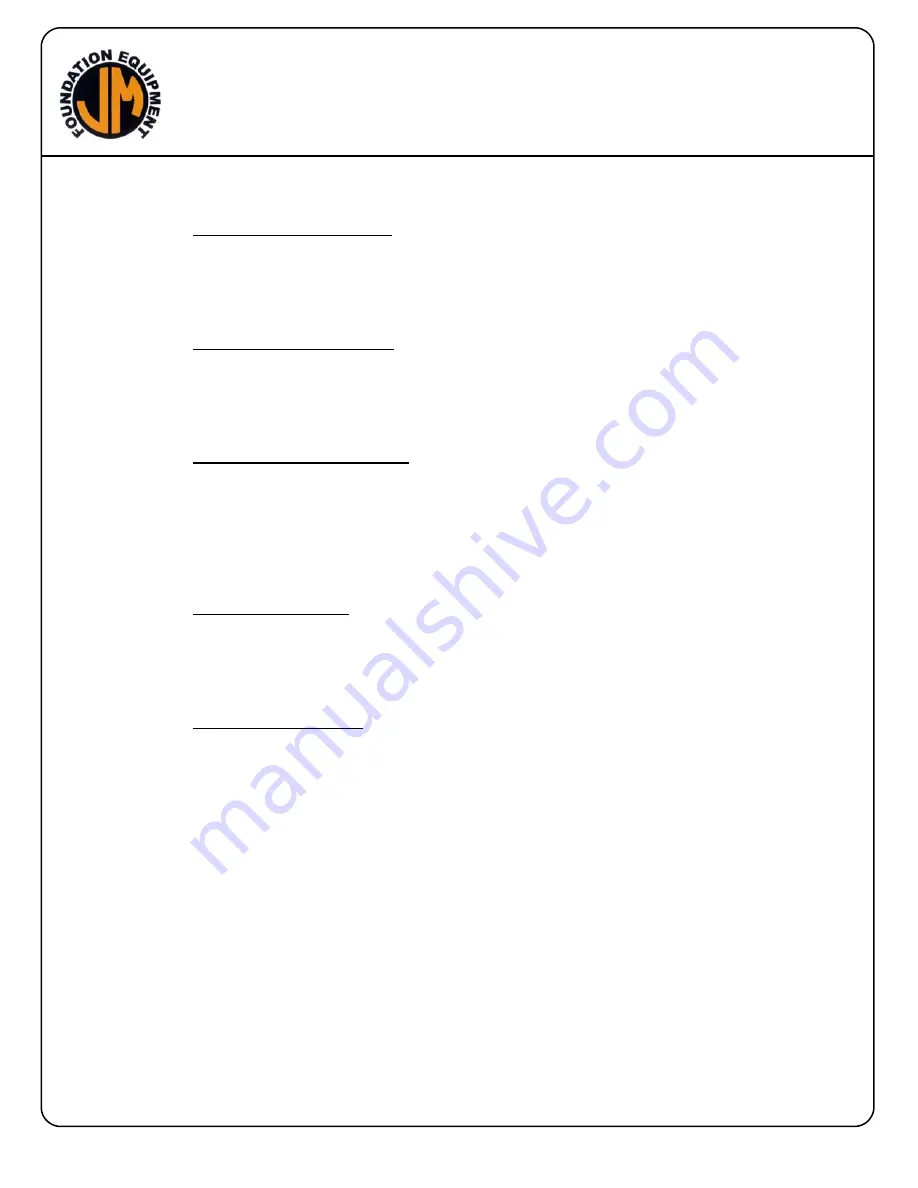
MODEL 220
HYDRAULIC
IMPACT HAMMER
III. OPERATING
INSTRUCTIONS
F.
STARTING
THE
HAMMER
After choosing the desired stroke setting, the hammer is started by turning the
FORWARD-REVERSE switch to the FORWARD position. The hammer will
continue to run as long as the switch is in the FORWARD position.
G.
STOPPING
THE
HAMMER
The hammer is stopped by turning the FORWARD-REVERSE switch from the
FORWARD position to the neutral position. The hammer may be stopped at any
point in its cycle.
H.
SINGLE
BLOW
OPERATION
The hammer can be made to deliver a single blow or a short series of blows using
the FORWARD-REVERSE switch. To deliver a single blow, start the hammer as
described above and as the ram begins to descend, turn the FORWARD-
REVERSE switch back to the neutral position. The ram will fall, delivering a single
blow. The hammer may be stopped after delivering any number of blows.
I.
EMERGENCY
STOP
When the diesel engine is running, pressing the EMERGENCY STOP button on the
pendant, energizes the coil on the SHUTDOWN RESET. The Sutdown Reset
opens and the engine and the hammer are stoppped.
J. ENGINE SHUT DOWN
Stop the hammer. Allow the diesel engine to run for 5 minutes at 1500 RPM.
Reduce engine rpm to 1000 RPM for 30 seconds. Stop the engine by turning the
ENGINE START switch to OFF. The MAIN SWITCH on the control panel should be
OFF.
III-6
Summary of Contents for 220
Page 2: ...MODEL 220 HYDRAULIC IMPACT HAMMER ...
Page 4: ...MODEL 220 HYDRAULIC IMPACT HAMMER ...
Page 24: ...MODEL 220 HYDRAULIC IMPACT HAMMER ...
Page 48: ...MODEL 220 HYDRAULIC IMPACT HAMMER ...
Page 52: ...MODEL 220 HYDRAULIC IMPACT HAMMER ...
Page 54: ...MODEL 220 HYDRAULIC IMPACT HAMMER V HYDRAULIC CIRCUITRY HYDRAULIC SCHEMATIC V 4 ...
Page 59: ...MODEL 220 HYDRAULIC IMPACT HAMMER VI ELECTRICAL CIRCUITRY ELECTRICAL LAYOUT VI 4 ...
Page 60: ...MODEL 220 HYDRAULIC IMPACT HAMMER VI ELECTRICAL CIRCUITRY ELECTRICAL SCHEMATIC VI 5 ...
Page 65: ......
Page 66: ......
Page 67: ......
Page 68: ......
Page 69: ......
Page 70: ......
Page 71: ......
Page 72: ......
Page 75: ......
Page 76: ......
Page 78: ......
Page 80: ......