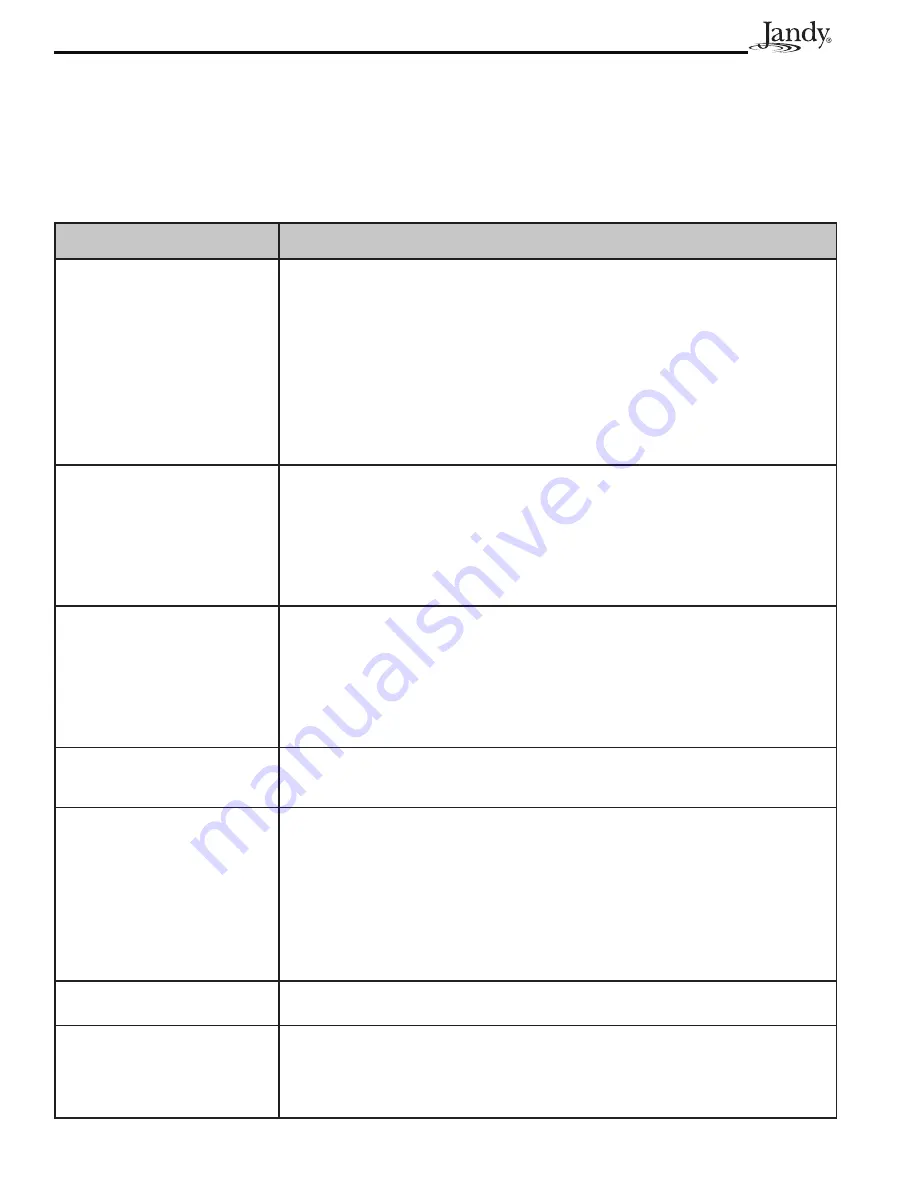
Page 14
FloPro Series Pumps Installation and Operation Manual
Section 6. Troubleshooting and Repair
Zodiac Pool Systems, Inc. strongly recommends that you call a qualified service technician to perform any repairs
on the filter/pump system. To locate a qualified technician, check your local yellow pages or visit
www.jandy.com
and
click on “Product Support.”
6.1 Troubleshooting
Symptom
Possible Problem/Solution
The cleaning/circulating system is
not operating correctly.
Verify that skimmer baskets, pump basket and other screens are clean. Clean as
necessary.
Check filter and clean as necessary.
Check valve positions. Adjust as necessary.
NOTE
Multiple pieces of equipment operating at one time (for example, waterfalls, spa
jets, and surface returns) may affect the cleaning system and prevent it from working
properly.
Check the cleaning system manual to ensure that the system is adjusted according to the
manufacturer's recommendations.
Bubbles present in the pump
basket.
Air in system. Check the pool or spa water level to ensure that it is at the proper level and
that air is not being drawn into the suction piping. If the water is at the normal level, turn off
the pump. Turn the lid’s locking ring counter-clockwise until ‘START’ aligns with the ports.
Carefully remove the lid and check for debris around the lid o-ring seat, as debris will cause
air to leak into the system. Clean the lid o-ring and place on the lid. Replace the lid with
locking ring on the pump housing. Align ‘START’ with the ports and turn the lid’s locking
ring clockwise until ‘LOCKED’ aligns with the ports.
Hand-tighten
the lid to make an air
tight seal.
Do not use any tools to tighten the lid
. Turn the pump back on.
Air leaks are still present.
Check the suction side piping union. While the pump is running, try to tighten the union. If
this does not stop the air leak, turn off the pump. Loosen both unions and slide the pump
out of the way. Remove, clean and re-install both union o-rings.
Reposition the pump next to the piping and secure the union nuts to the pump. With clean
union o-rings, hand-tightening of the unions should create a seal. If the unions still do not
seal, gently tighten with a large pair of tongue-and-groove pliers.
Do not over-tighten
.
There is no air in the system, but
the pressure is still low.
It is possible that debris is caught in the pump impeller. The pump impeller moves the
water, and the vanes in the impeller can become blocked with debris. See
Section 6.2,
Service Technician Maintenance, 6.2.1, Blocked Impeller,
for more information.
There is no debris blocking the
impeller
and
the pressure is still
low.
The pump impeller and diffuser are showing signs of normal wear. Have a qualified service
technician check the impeller and diffuser and replace as necessary.
If the pump is part of a relatively new installation, it could be an electrical problem. Contact
a qualified service technician. Have the technician check for loose electrical connections
and check the voltage at the pump motor while it is in operation. The voltage must be within
10% of the motor’s data plate rating. If the voltage is not within 10%, contact a qualified
electrician and/or the local power service provider.
The pump seal is leaking air. Have a qualified service technician replace the seal.
The pump is leaking water between
the motor and pump body.
This is caused by a damaged or failed mechanical seal. Replace the seal. See
Section 6.2,
Service Technician Maintenance, 6.2.4, Mechanical Seal Replacement
.
The pump gets hot and shuts off
periodically.
Ensure that there is adequate room around the motor to circulate air and keep the motor
cool. Have a qualified electrician check for loose connections and check the voltage at the
pump motor while it is in operation. The voltage must be within 10% of the motor's data
plate rating. If the voltage is not within 10%, contact a qualified electrician and/or the local
power service provider.
Summary of Contents for FHPM FloPro Series
Page 2: ......