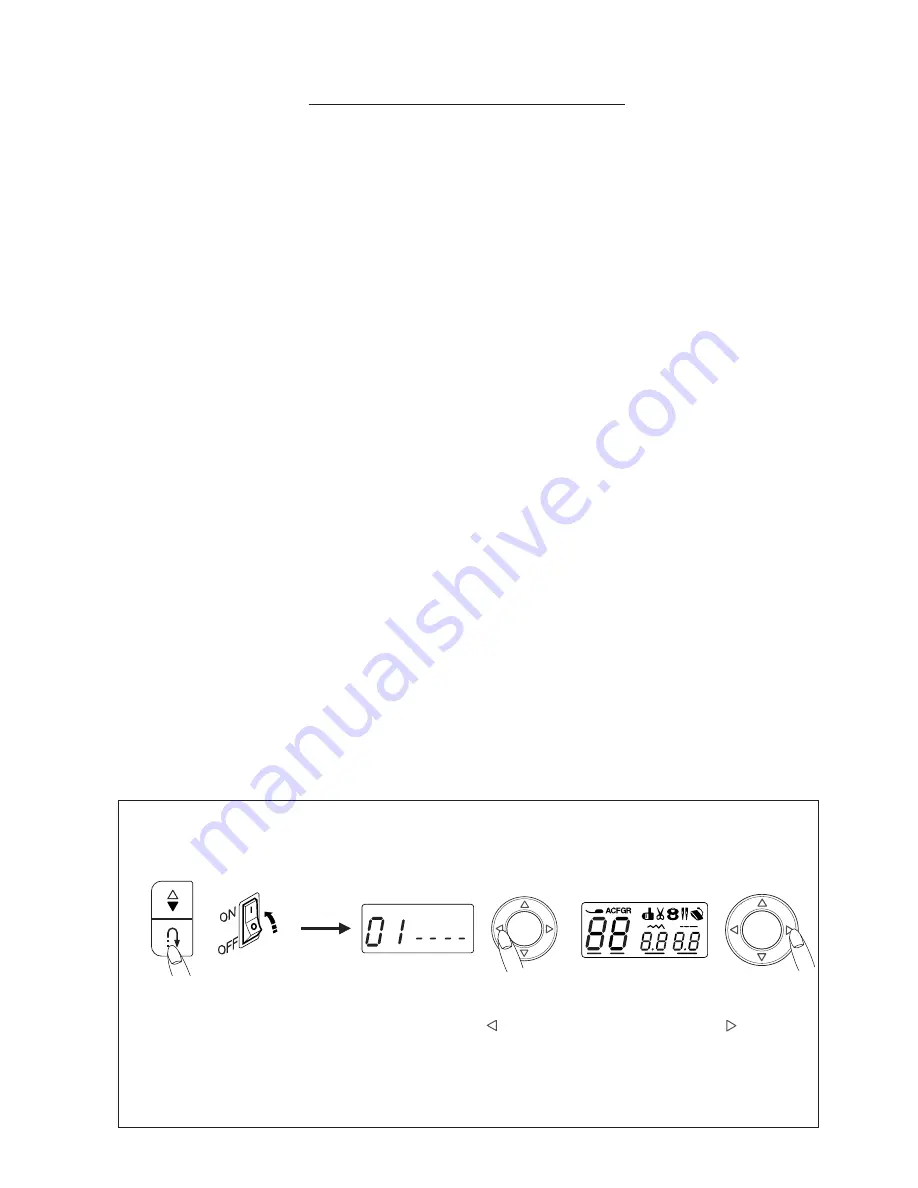
21
SELF DIAGNOSTIC TESTS
Preparation:
1. Turn the power switch off.
2. Move the bobbin winder spindle to the left.
3. Remove the presser foot and raise the presser foot lifter.
4. Turn the hand wheel toward you to raise the needle to its highest position.
Notes:
• Be careful: the sewing machine may start running in its own while in test mode.
• Turn off the power switch before replacing any parts.
• Repeat the diagnostic test until the problem has been resolved.
• You can skip steps in the diagnostic procedure and go directly to the test you want to perform.
(Enter self-diagnostic mode, then select the step number of the diagnostic test you require by
pressing the reverse button)
To begin:
Turn on the switch, if any of the following problems occur, take the recommended actions in the order
they are shown.
1. The machine does not respond when the power switch is turned on:
• Check each connector connection
• Replace the machine socket
• Replace the Switching regulator.
• Replace the A-board
2. The sewing machine lamp does not light up:
• Replace the light bulb
• Replace the A-board
To enter self-diagnostic mode:
Turn the power switch on while
pressing the Reverse button.
Press the Ring button (left) mark.
The LCD display indicates "01".
Press the Ring button (right)
mark to enter the self-diagnostic
mode.
No.1
No.2
No.3
If you do not press the next button within 1.5 sec, the machine will revert to normal sewing mode.
Should this occur, start over again from step No.1.
Summary of Contents for NH40
Page 1: ...SERVICE MANUAL MODEL NH40...