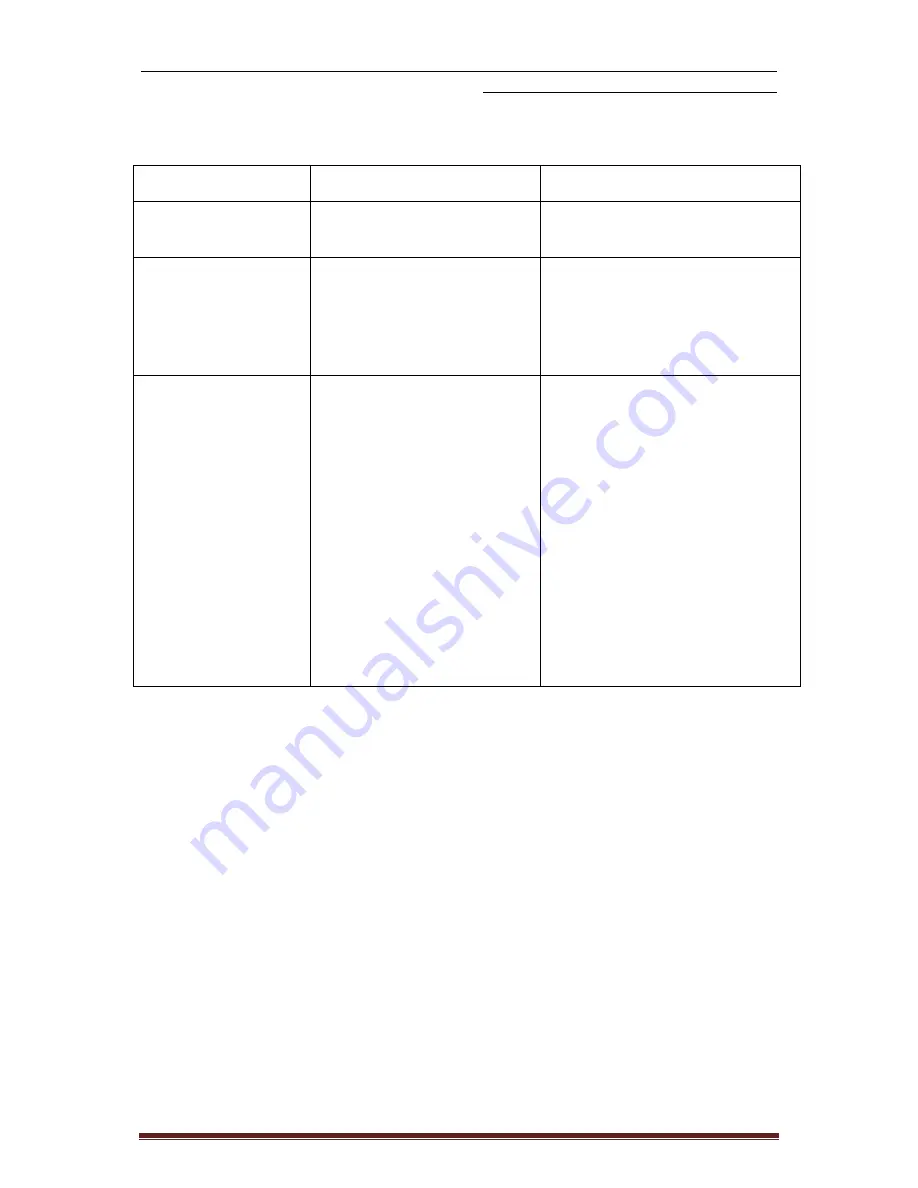
JAVELIN MACHINERY (AUSTRALIA)
J800 /J900 OPERATION MANUAL
(incl. Troubleshooting Machine Problems)
JULY 2016
Page 19
MANDREL SUPPORT ARM
PROBLEM/EFFECT
CAUSE
REMEDIES
Mandrel vibrates
Worn pivot bearings or shaft
on mandrel support arm.
Replace bearings and housings.
Sideways movement
between mandrel
support arm and
mandrel support
bearing.
Bearing loose in bearing
housings.
Loosen grub screws in bearings
and tap bearing outwards in
bearing housing - lock grub screws.
Replace housings and bearings.
Knife not slitting
through core and/or
knife cutting into
mandrel at one end of
machine.
Mandrel support not aligned
parallel to knife carriage.
•
Raise mandrel support.
•
Traverse carriage to extreme
right.
•
Adjust forward knife stop so
that the knife just touches
mandrel.
•
Traverse knife to the extreme
left and move knife forward to
mandrel.
•
Loosen grub screws locking
mandrel support arm to
bearings and move arm side-
ways so that knife touches the
mandrel fractionally harder than
at other end of machine (0.1mm
or 0.004”).
•
Lock grub screws and re-check.