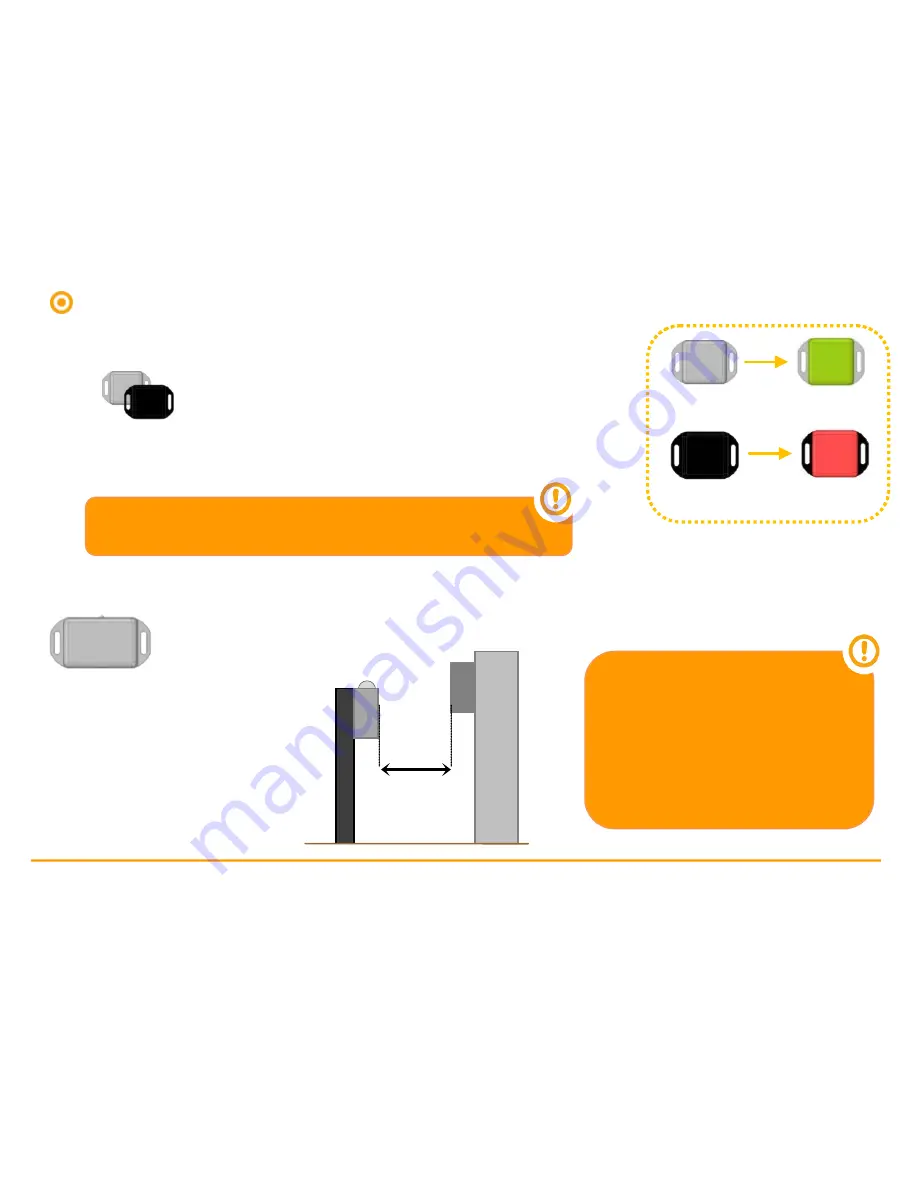
CAPTIVE SYSTEM
jcm
technologies
14
1-2 cm
Grey magnet
Green colour
on drawings
Red colour
on drawings
Black magnet
Red colour on
drawings
3.3.
CAP MAGIN
MAGNETS:
at the gate.
Grey magnet should be installed to activate the NO-TOUCH sensor when the gate
starts the close movement. Black magnet switches off the NO-TOUCH sensor in
order to allow the gate to closing
.
GREY – BLACK magnets position depends on the direction of the gate. CAP MAGIN LED must be GREEN while gate is
closing/opening, RED when gate is totally closed/opened.
CAP MAGIN:
install onto a support near the magnets and at the same height.
GA
TE
SU
PP
OR
T
M
AGN
ET
M
AGIN
In case the gate is not totally
opened/closed, a safety time of
5 minutes is added to avoid
battery consumption.
Maximum NO TOUCH
activation time = 5 minutes
Depending on the gate direction, BLACK magnet is the one
who actives the NO-TOUCH sensor.