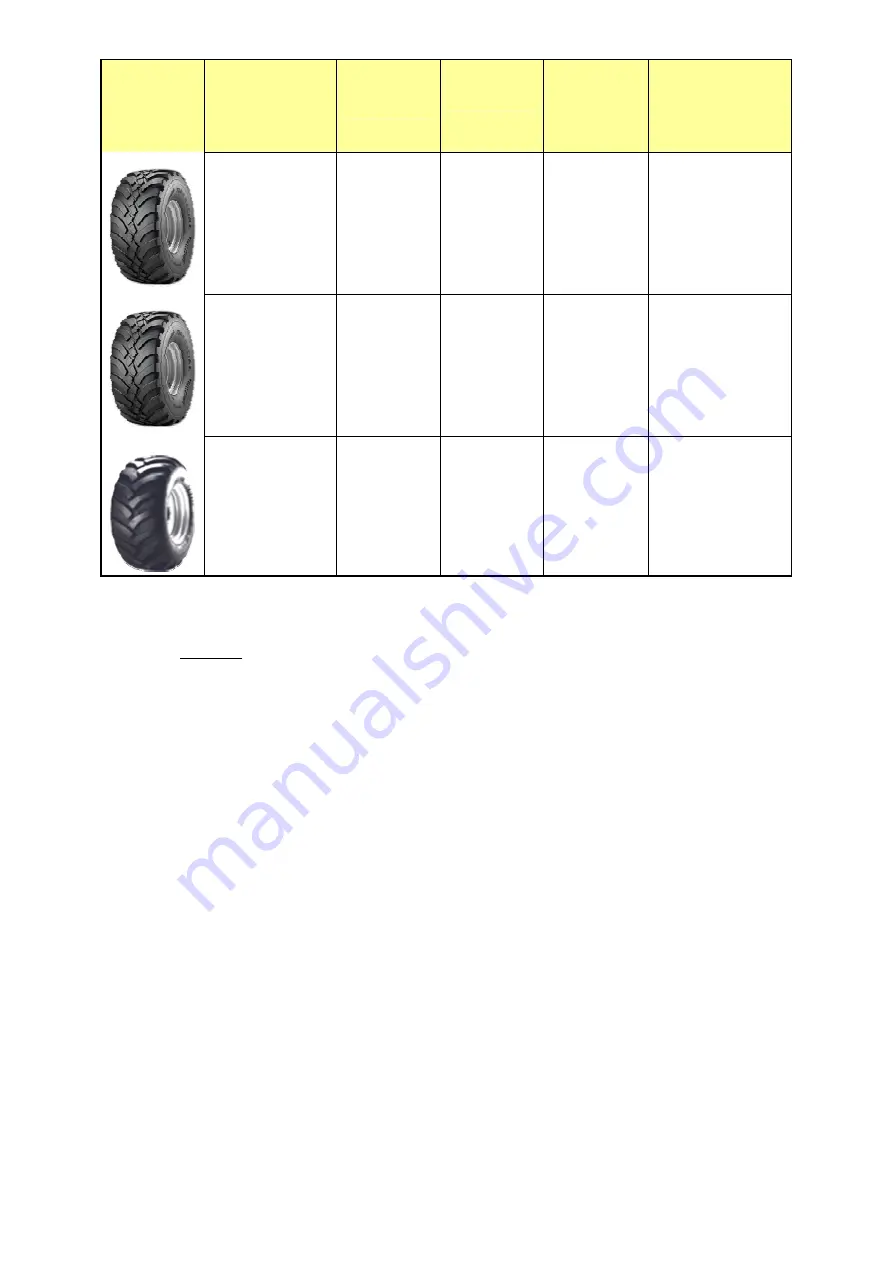
22
3-
Braking.
Regularly check:
The surface condition of cables
The tightness of the cable clamps
The cable tension
The thickness of the drum brake lining
6).
Hydraulic hoses.
1-
See page 15 (Section: Maintenance and repair).
2-
Regularly check the state of the hydraulic hoses, especially sections in contact with
the equipment.
3-
Control that there are no leaks from the hydraulic connectors.
4-
Retighten the hydraulic connectors if required after the first few hours of operation.
7).
Speed of moving floor’s hydraulic motor.
(Included in the hydraulic moving floor option)
1-
The speed of the moving floor’s hydraulic motor is electrically controlled. The
first
electric button
marked
0 (- +)
located at the bottom of the electric control unit,
enables to adjust the speed of the moving floor depending on the load in the body
and in certain cases of certain difficult products: (ex: compact manure, etc.).
Profile
Dimensions
Diameter
(unloaded)
Tyre width
(unloaded)
Load per
wheel in kg
(mini –
maxi)
Inflation
pressure in bars
(40km/h)
mini - maxi
600/55R 26,5
(Standard)
1,34 m
0,63 m
2495 - 7100
0,8 - 4
680/55R 26.5
(Option for
Tandem / Bogie
/ Tridem)
1,4 m
0,67m
2995 - 6900
0,8 – 3,2
600/60 X 26.5
(Option for
Tandem &
Bogie)
1,5 m
0.60m
1570 - 3650
0,5 – 2,4