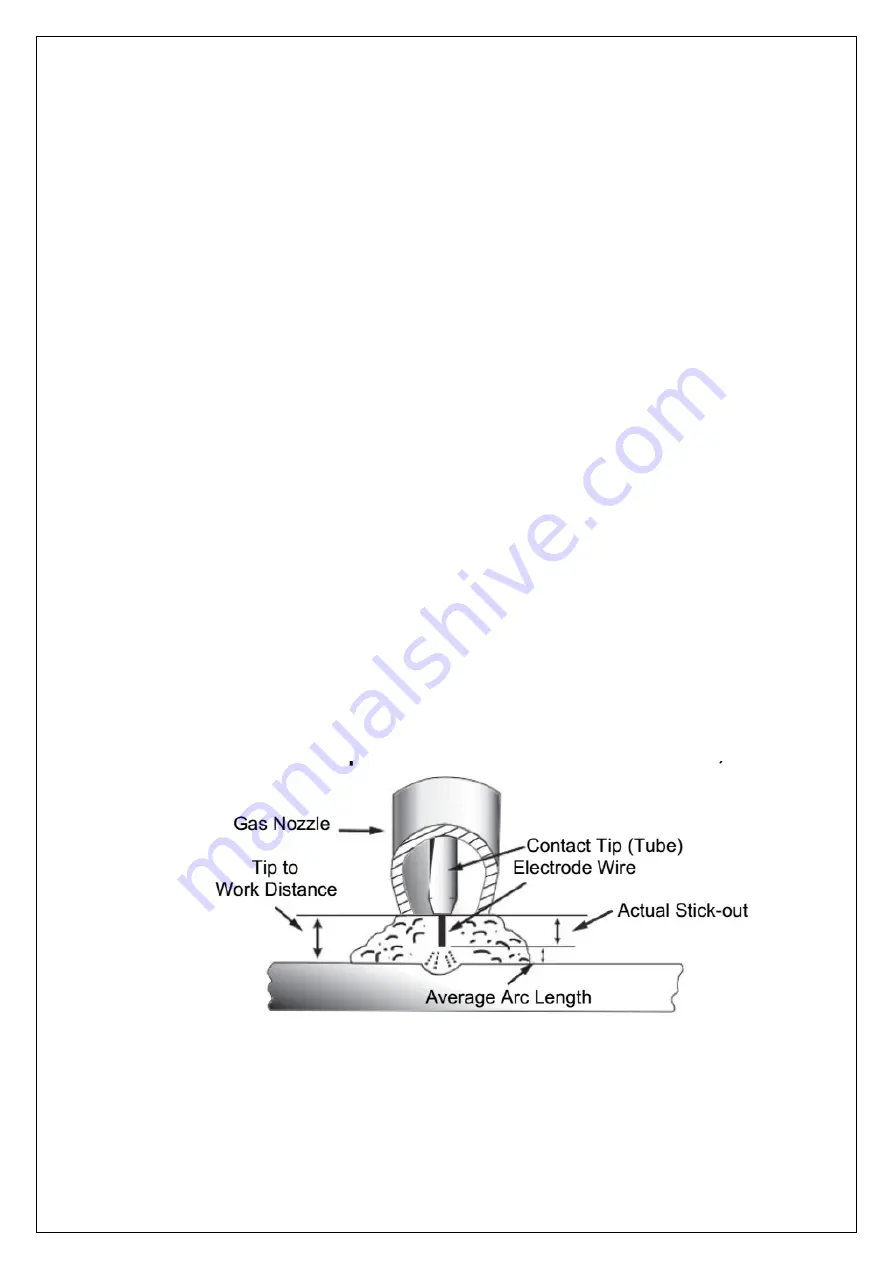
18
Distance from the MIG Torch Nozzle to the Work Piece
The electrode wire stick out from the MIG Torch nozzle should be between 10mm to 20.0mm. This distance
may vary
depending on the type of joint that is being welded
Travel Speed
The speed at which the molten pool travels influences the width of the weld and penetration of the welding run
MIG Welding (GMAW) Variables
Most of
the welding
done by all processes
is on
carbon
steel. The
items below
describe
the
welding.
variables in short
‐
arc welding of 24gauge (0.024”, 0.6mm) to
¼” (6.4mm) mild sheet or plate. The applied techniques
and end results in the GMAW process are controlled by these variables.
Preselected Variables
Preselected variables depend upon the type of material being welded, the thickness of the material, the welding position,
the deposition rate and the mechanical properties. These variables are:
Type of electrode wire
Size of electrode wire
Type of gas (not applicable to self
‐
shielding wires FCAW)
Gas flow rate (not applicable to self
‐
shielding wires FCAW)
Primary Adjustable Variables
These control the process after preselected variables have been found. They control the penetration, bead width, bead
height, arc stability, deposition rate and weld soundness. They are:
Arc Voltage
Welding current (wire feed speed)
Travel speed
Secondary Adjustable Variables
These variables cause changes in primary adjustable variables which in turn cause the desired change in the bead
formation. They are:
1.Stick
‐
out (distance between the end of the contact tube (tip) and the end of the electrode wire). Maintain at about
10mm stick
‐
out
2. Wire Feed Speed. Increase in wire feed speed increases weld current, Decrease in wire feed speed decreases weld
current
3. Nozzle Angle. This refers to the position of the welding gun in relation to the joint. The transverse angle is usually one
half the included angle between plates forming the joint. The longitudinal angle is the angle between the center line of
the welding gun and a line perpendicular to the axis of the weld. The longitudinal angle is generally called the Nozzle
Angle and can be either trailing (pulling) or leading
(pushing). Whether the operator is left handed or right handed has to be considered to realize the effects
of each angle in relation to the direction of travel.