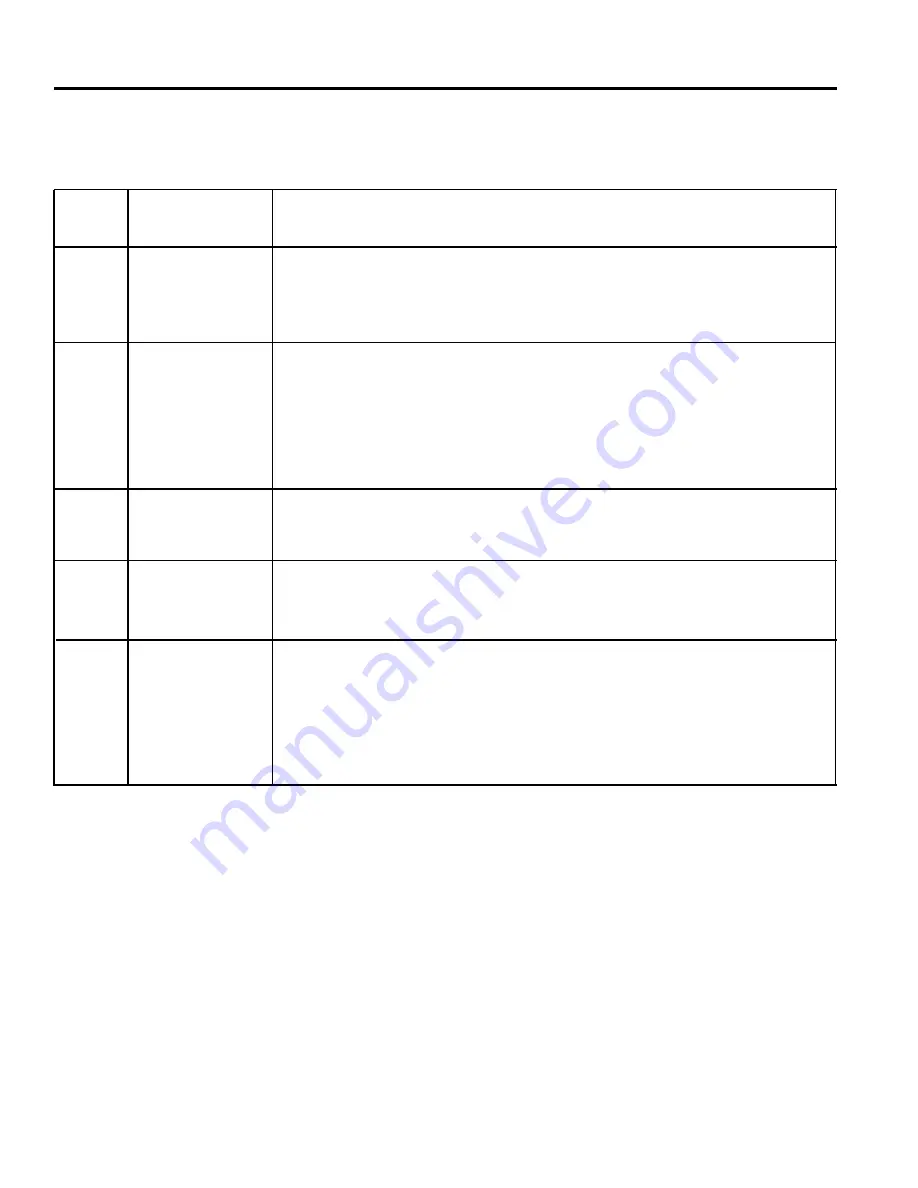
ERROR CODES
NOTE: . .“Beeps” .occur .when .the .Error .Code .appears .on .the .Main .Display
ERROR
CODE
DESCRIPTION
PROBABLE CAUSE
INVALID .ENTRY .
ERROR: . .STAGE, .
HEAT .RATE .and .
TEMP .lights .flash
Occurs . when . the . HEAT .RATE . is . set . to . COOL . but . the . TEMP . of . that . stage . is .
higher .than .the .TEMP .of .the .prior .stage .(should .be .heating) . . .This .will .occur .
when .a .program .is .already .running .and .a .parameter .was .edited .in .process .
Er .1
Occurs .when .the .temperature .on .the .display .is .outside .the .allowable .range .
at .the .time .the .user .pressed .the .ENTER ./ .REVIEW .keys .simultaneously .to .set .
the .Infinity .calibration .temperature .to .1500
°
F . . .If .this .occurs .and .is .not .an .
operator .error, .it .indicates .that .there .is .a .problem .with .the .thermocouple .or .
the .PC .board . . .Press .ENTER ./ .REVIEW .to .turn .off .the .error .indication .and .
continue .with .the .program . . .Press .START ./ .STOP .to .end .the .program .
TABLET
TEMPERATURE
CALIBRATION
ERROR
Er .2
ELECTRONICS .
MALFUNCTION
Er .3
Occurs .when .PC .board .hardware .malfunctions .
OPEN .
THERMOCOUPLE
Occurs .if .the .thermocouple .is .open .or .the .connecting .wire(s) .are .broken .or .
disconnected .from .the .terminal .board .
Er .4
REVERSED
THERMOCOUPLE
Occurs .if .the .thermocouple .extension .wires .have .been .connected .backwards .
to .the .terminals .on .the .printed .circuit .board . . .The .error .will .be .detected .5 .
minutes .after .heating .program .started . . .This .error .will .also .occur .if .the
program .is .started .and .the .chamber .door .is .kept .open .for .5 .minutes .or .the .
triac .is .defective, .the .heater .plates .are .defective .or .there .is .a .problem .with .
the .main .PC .board .
Er .5
17