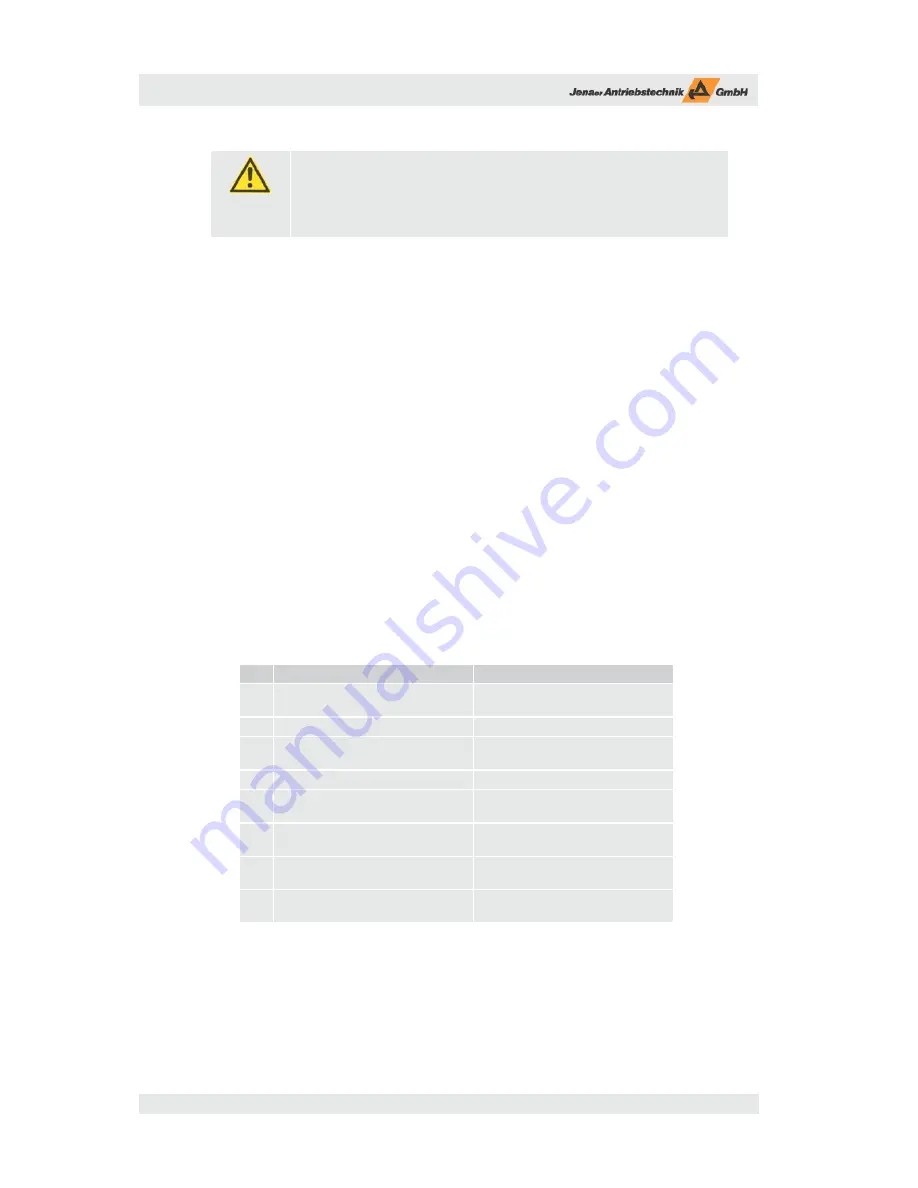
Installation and Operating Instructions ECOVARIO®114 D
30
Subject to change without notice!
The STO function may only be activated by an automatic control or by manual activation
if the motor is no longer rotating and the servo amplifer has been switched to „inactive“
(24 V are not applied to „Enable“ input). Drives with a suspended load must have an additio-
nal safe mechanical blocking. Via the safety PLC the monitoring contact ASOut bridges the
safety equipment of the machine (e.g. safety position switches at safety doors). The safety
area is now protected from indeliberate restart of the device.
Relevant aspects of safety
See also the prescribed use of the servo amplifi er ECOVARIO® 114 D described in chap. 2.6 and the opera-
ting conditions mentioned there.
As Fig. 6.19 shows the STO function is implemented by two channels. If a single error occurs, the function
still remains operative via the other channel.
If the restart lock is active, all driver transistors are in high resistance state. If a current in the motor is pro-
duced by damaged driver transistors the high-pole servo motors as well as the 2-phase servo motors cannot
start because the necessary rotating fi eld is not created. In the worst case, however, a short hitch can occur
at the motor shaft (movement of max. 1/2 pole pair of the motor).
If the internal semiconductor switch is damaged or a cable is broken the safety equipment switches off the
drive because in this case the bridging of the safety equipment is not eff ective.
If the restart lock is activated by an automatic control, the control signal must be monitored to make sure
that the restart lock cannot be activated if the motor is rotating.
Commissioning and checking the STO function
During commissioning of the machine, aft er changing components or restructuring the wiring the function
of the safety equipment including the STO function must always be checked as described in table 6.12. Th is
check is also necessary aft er modifi cations of the parameters of aft er a download of a new fi rmware. If none
of the mentoined cases applies, the function of the safety equipment has to be checked at least once a year.
Per axis proceed as follows:
Table 6.12: Checking the functions of the safety equipment
Step Measure
Check
1
Make sure that during the check the dri-
ve can run and stop unrestrictedly
2
Stop drive controlled (target velocity=0)
3
Disable drive (remove Enable signal)
Measure the signal level at the Ready si-
gnal: has to be inactive (0 V).
4
Activate the holding brake, if any
5
Remove the +24 V voltage at STO IN, i.e.
activate the STO function
6
Open safety equipment (e.g. safety door)
without interfering with the safety area.
Line contactor must stay „on“.
7
Pull off mating connector X8 from the
respective servo amplifier.
Line contactor must drop.
8
Plug in mating connector X8. Switch on
line contactor.
Provided that the checks are carried out regularly as described above, the example circuit below meets the
requirements of performance level d according to EN ISO 13849-1.