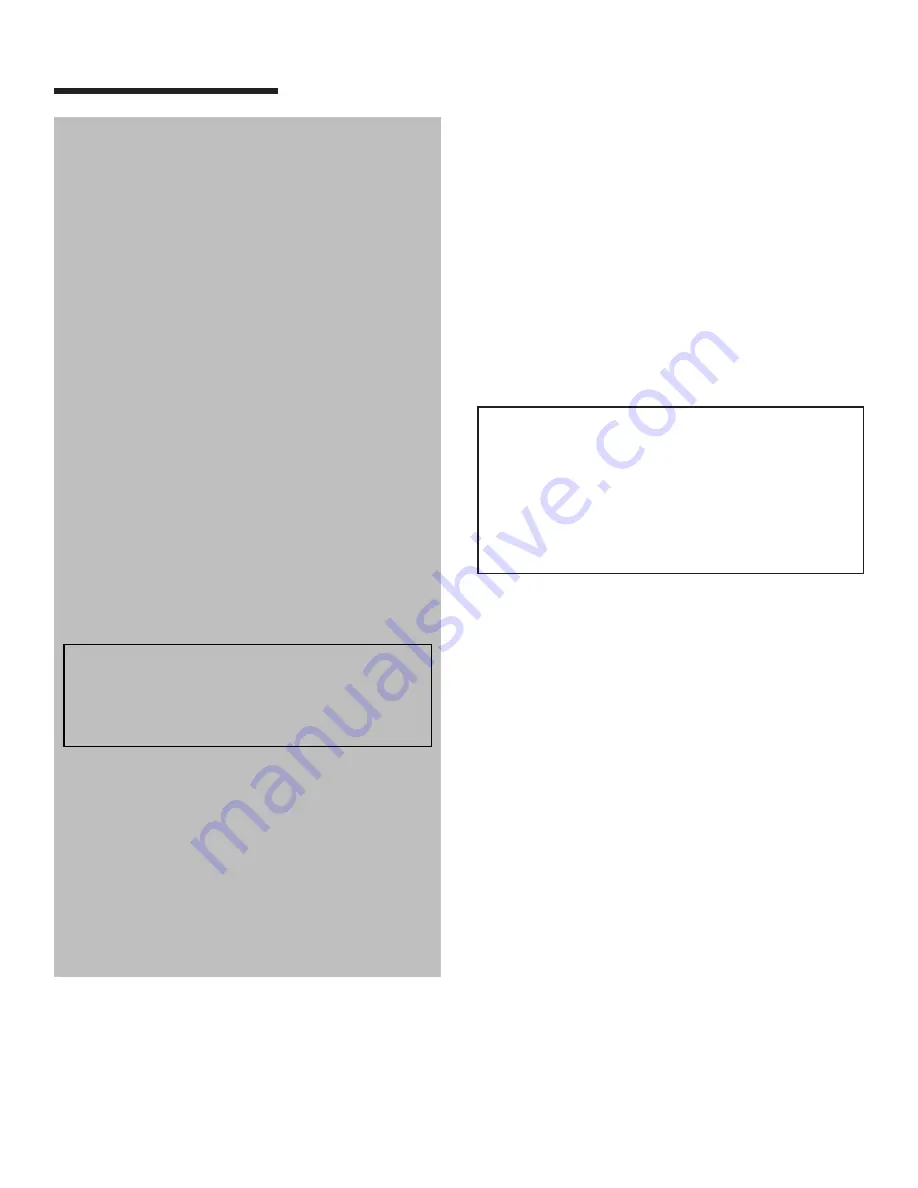
17
Warranty
What is Not Covered By These Warranties:
1. Conditions and damages resulting from any of the
following:
a. Improper installation, delivery, or maintenance.
b. Any repair, modification, alteration, or adjustment not
authorized by the manufacturer or an authorized
servicer.
c. Misuse, abuse, accidents, or unreasonable use.
d. Incorrect electric current, voltage, or supply.
e. Improper setting of any control.
2. Warranties are void if the original serial numbers have
been removed, altered or cannot be readily determined.
3. Light bulbs.
4. Products purchased for commercial or industrial use.
5. The cost of service or service call to:
a. Correct installation errors.
b. Instruct the user on the proper use of the product.
c. Transport the appliance to the servicer.
6. Consequential or incidental damages sustained by any
person as a result of any breach of these warranties.
Some states do not allow the exclusion or limitation of
consequential or incidental damages, so the above may not
apply.
User’s guides, service manuals and parts information are available from Maytag Services
SM
, Jenn-Air Customer Assistance.
Jenn-Air • 403 West Fourth Street North • P.O. Box 39 • Newton, Iowa 50208
NOTE:
When writing or calling about a service problem,
please include the following information:
– Your name, address and telephone number;
– Model number, serial number and revision number;
– Name and address of your dealer and the date the
appliance was bought;
– A clear description of the problem you are having;
– Proof of purchase (sales receipt).
To receive warranty service:
To locate an authorized service company in your area
contact the Jenn-Air dealer from whom your appliance was
purchased; or call Maytag Services
SM
, Jenn-Air Customer
Assistance at the number listed below. Should you not
receive satisfactory warranty service, please call or write:
Maytag Services
SM
Attn: Jenn-Air CAIR
®
Center
P.O. Box 2370
Cleveland, TN 37320-2370
U.S.A. and Canada . . . . . . . . . . . . . . .1-800-JENNAIR
(1-800-536-6247)
U.S.A. customers using
TTY for deaf, hearing impaired
or speech impaired . . . . . . . . . . . . . .1-800-688-2080
Full One Year Warranty
For
one (1) year
from the original retail purchase date,
any part which fails in normal home use will be repaired
or replaced free of charge.
Limited Warranties - Major Refrigeration
Components
Second Through Fifth Years -
After the first year from
the original purchase date through the end of the fifth
year, the manufacturer will repair or replace, at its option,
free of charge for parts and labor (only), any part of the
sealed refrigeration system (consisting of the compressor,
evaporator, condenser, dryer and connecting tubing)
which fail in normal home use. All other costs, including
mileage, transportation, trip charge and diagnostic
charge, if required, shall be the responsibility of the
owner.
Limited Warranties - Other Parts
Second Year -
Parts other than major refrigeration
components which fail in normal home use during the
second year following the original retail purchase date
will be repaired or provided free of charge for the part
itself, with the owner paying all other costs, including
labor, mileage, transportation, trip charge and diagnostic
charge, if required.
LIMITATIONS OF LIABILITY
The warrantor shall not be liable for any incidental or
consequential damages, including food loss. Some states
do not allow the exclusion or limitation of consequential
damages, so the above limitation or exclusion may not
apply to you.
The specific warranties expressed above are the
ONLY
warranties provided by the manufacturer. These warranties
give you specific legal rights, and you may also have other
rights which vary from state to state.
NOTE:
The full warranty and the limited warranties
apply when the refrigeration product is located in the
U.S.A. or Canada. Products located elsewhere are
covered by the limited warranties only including parts
that fail during the first year.