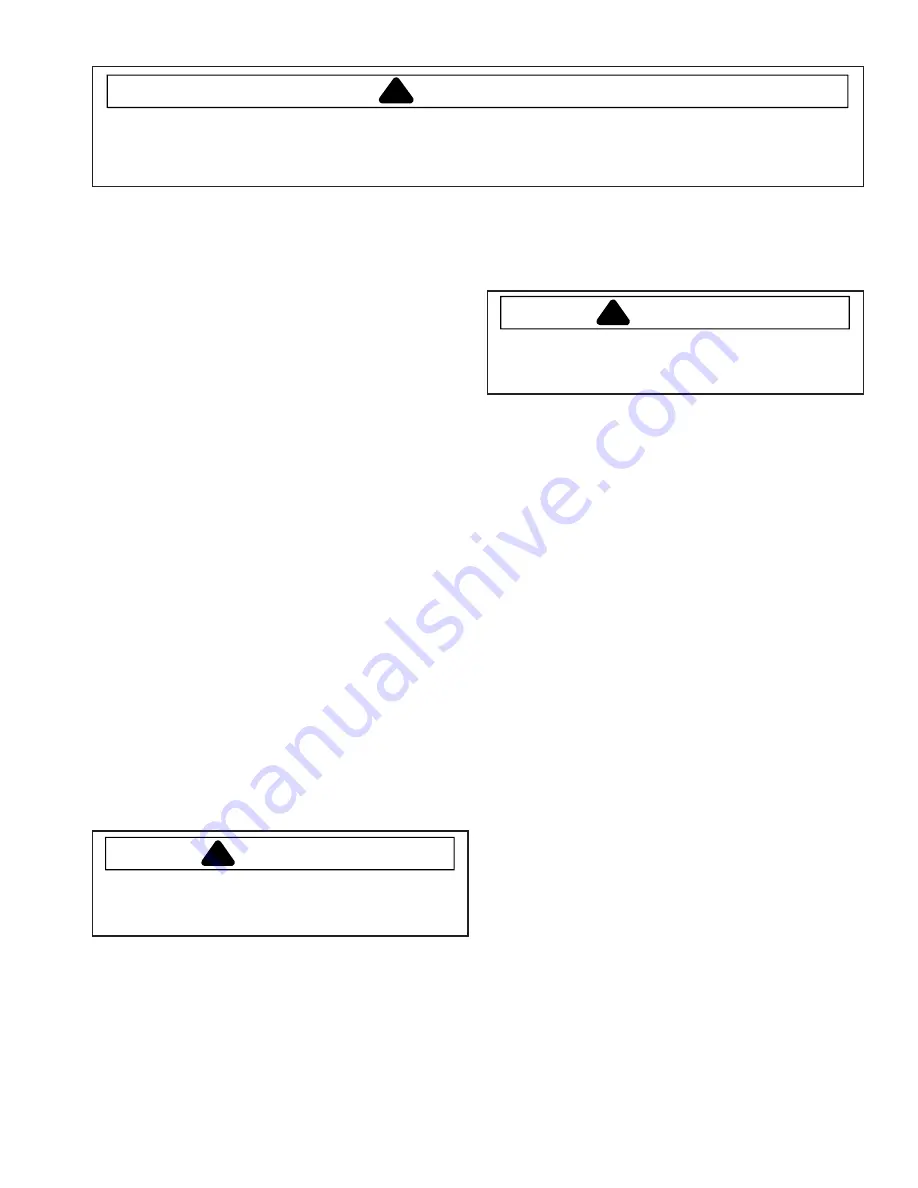
9
16021730 Rev. 0
Service Procedures
!
WARNING
To avoid risk of electrical shock, personal injury, or death, disconnect electrical power source to unit, unless test
procedures require power to be connected. Discharge capacitor through a 10,000 ohm resistor before attempting
to service. Ensure all ground wires are connected before certifying unit as repaired and/or operational.
Testing for Restrictions
To determine if a restriction exists:
1. Attach gauge and manifold between suction and
discharge sides of sealed system.
2. Turn unit on and allow pressure on each side to
stabilize. Inspect condenser side of system. Tubing on
condenser should be warm and temperature should be
equal throughout (no sudden drops at any point along
tubing).
If temperature of condenser tubing is consistent
throughout, go to step 4.
If temperature of condenser tubing drops suddenly at
any point, tubing is restricted at point of temperature
drop (if restriction is severe, frost may form at point
of restriction and extend down in direction of
refrigerant flow in system). Go to step 5.
3. Visually check system for kinks in refrigeration line
which is causing restriction. Correct kink and repeat
step 2.
4. Turn unit off and time how long it takes high and low
pressure gauges to equalize:
If pressure equalization takes longer than 10
minutes, a restriction exists in the capillary tube or
drier filter. Go to step 5.
If pressure equalization takes less than 10 minutes,
system is not restricted. Check for other possible
causes of malfunction.
5. Recover refrigerant in sealed system.
NOTE
: Before opening any refrigeration system, capture
refrigerant in system for safe disposal.
6. Remove power from unit.
CAUTION
!
To avoid risk of personal injury or property damage,
take necessary precautions against high
temperatures required for brazing.
7. Remove and replace restricted device.
8. Evacuate sealed system.
9. Charge system to specification.
NOTE
: Do not use captured or recycled refrigerant in
Maytag units. Captured or recycled refrigerant
voids any Maytag and/or compressor
manufacturer's warranty.
NOTE
: Charge system with exact amount of refrigerant.
Refer to unit nameplate for correct refrigerant
charge. Inaccurately charged system will cause
future problems.
Evacuation and Charging
CAUTION
!
To avoid risk of fire, sealed refrigeration system must
be air free. To avoid risk of air contamination, follow
evacuation procedures exactly.
NOTE
: Before opening any refrigeration system, EPA
regulations require refrigerant in system to be
captured for safe disposal.
Proper evacuation of sealed refrigeration system is an
important service procedure. Usable life and operational
efficiency greatly depends upon how completely air,
moisture and other non-condensables are evacuated
from sealed system.
Air in sealed system causes high condensing
temperature and pressure, resulting in increased power
requirements and reduced performance.
Moisture in sealed system chemically reacts with
refrigerant and oil to form corrosive hydrofluoric and
hydrochloric acids. These acids attack motor windings
and parts, causing premature breakdown.
Before opening system, evaporator coil must be at
ambient temperature to minimize moisture infiltration
into system.
Evacuation
To evacuate sealed refrigeration system:
1. Connect vacuum pump, vacuum tight manifold set with
high vacuum hoses, thermocouple vacuum gauge and
charging cylinder as shown in illustration.
Evacuation should be done through I.D. opening of
tubes not through line piercing valve.
2. Connect low side line to compressor process tube.
3. Connect high side line to drier/process tube.
4. Evacuate both simultaneously. With valve C and F
closed, open all other valves and start vacuum pump.