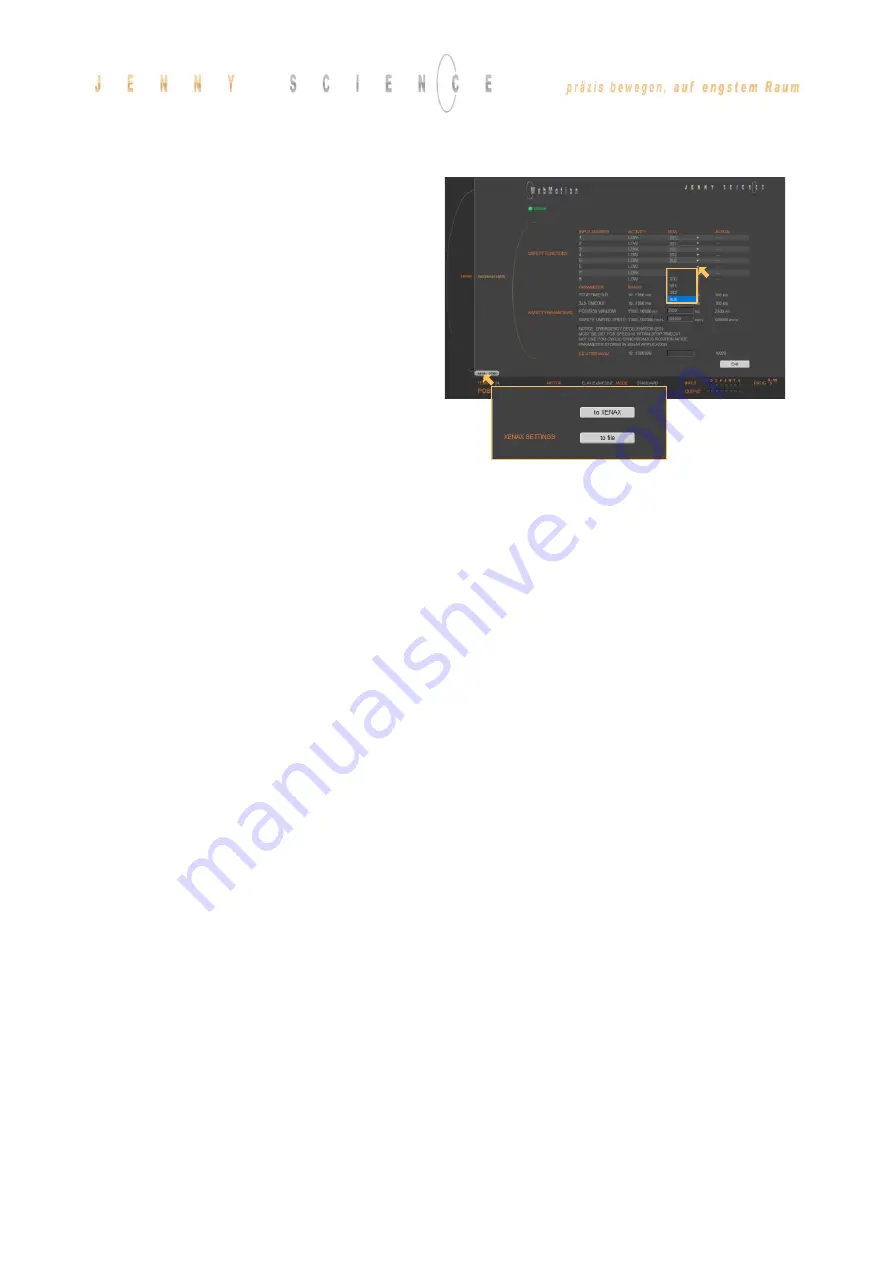
19
Actual
Current safety parameters of XENAX
®
servo
controller with SMU.
New
This is where new safety parameters can be selected
from the drop down menu. They are activated in
XENAX® servo controller by pressing „save“.
save
to XENAX
®:
The modified safety parameters are being sent to
XENAX
®
/ SMU. The active parameters are visible in
the column XENAX
®
.
to File:
The safety parameters on the SMU are saved into a
file.
open
Safety parameters can also be loaded from a pc file.
In order to be activated on the XENAX® servo
controller, the parameters have to be saved by
pressing on the
save
→
to XENAX
.
ED x 1000
The Parameter
ED „Emergency Deceleration“ muss be
set as big, that STOP and SLS Timeout can be hold by
stopping.
By pressing „
EXIT
“
you exit functional safety and get
back to WebMotion®.
Note:
The Signal of an active safety function has to be
operated by a higher level control system.