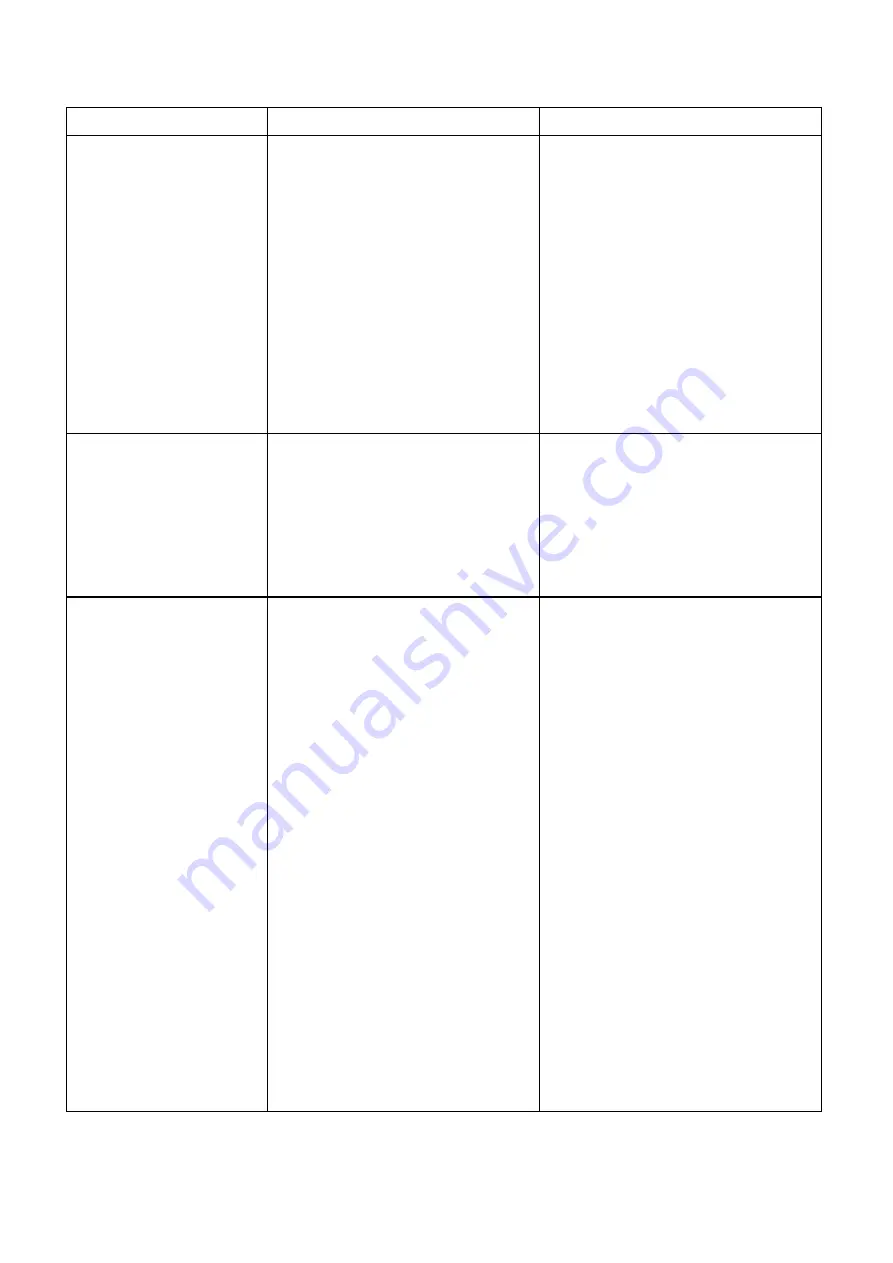
40
TROUBLE SHOOTING
TROUBLE
PROBABLE CAUSES
REMEDY
1 .Oil level In headstock Is too low or
Replenish or discharge the oil to the
too much.
proper level.
2.Quality and viscosity of oil is wrong.
Replace the oil with recommended type.
3.Oil is too dirty.
Replace the oil..
4.Oil hole in bearing is obstructed by
Remove the dirt from the oil hole
dirt.
5. Bearing obstructed by dirty.
Clean the bearing and renew oil.
6.Badly worn bearing.
Replace bearing.
7. Bearing is not in proper position.
Dismantle and reassemble it.
8. Bent or sprung main spindle.
Straighten or replace it.
Overheat of headstock bearings
9.Too much end thrust.
Adjust thrust nut.
1.Plug of drain not tight.
Resealing and tighten.
2.Case cracking.
Repaired by special welding.
Oil leakage
3.Leakage from overflow.
Tighten cover screws.
4.Packing or gasket damaged.
Replace packing or gasket.
5.Leakage from overflow on spindle
Less oil flow to bearing or enlarge oil
bearing housing.
return flow.
1. Badly worn bearing.
Replace bearing.
2. Lost levelling.
Recheck levelling & tighten.
3. Badly worn V belts.
Replace V belts.
4. Loose belt tension.
Adjust belt tension.
5. Badly worn gear.
Replace gear.
6. Bent or sprung shaft.
Straighten or replace shaft.
7. Pulley lossened
Tighten pulley set screw.
8. Clamp of workpiece in loose status.
Tighten clamp.
9. Bearing thrust too loose.
Tighten end thrust nut.
Excess noise or vibration
10. Headstock not tighten on bed.
Tighten fixed screws.
of machine
11. Excess clearance between the
Adjust the gib and tighten back
carriage and bed.
clamp.
12. Excess clearance in cross or
Adjust taper gib.
compound slide.
13. Cutting tool failure.
Replace correct cutting tool or regrind it
14. Tool holder not tight enough.
Tighten again check for debris..
15. Weak tool shank or too long.
Replace with rigid tool or reset.
16. Unbalance of workpiece while high
Balance workpiece or reduce spindle
speed running.
speed.