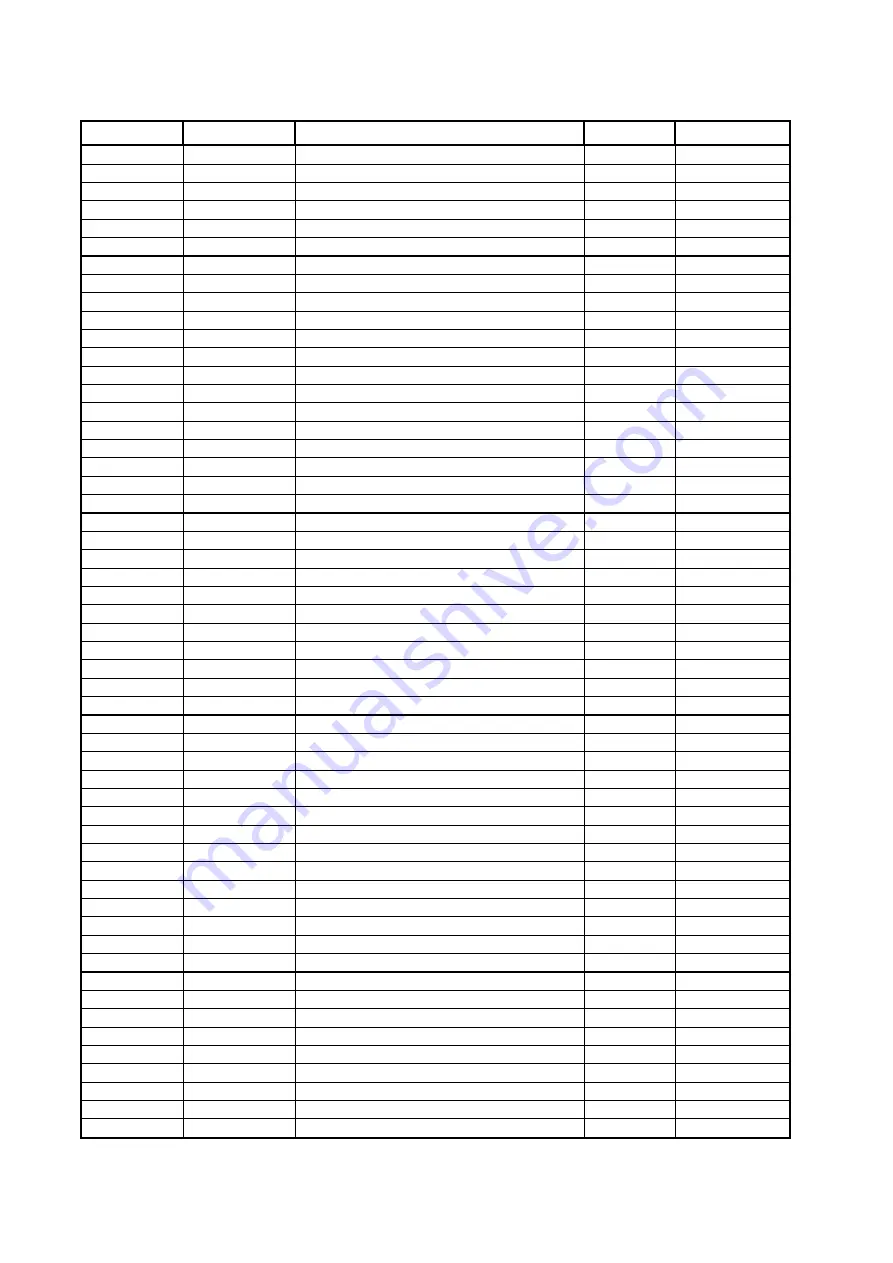
6.7 Spare parts list of lathe bed
Index NO
Parts NO.
Description
Size
Qty
201
BD11LB-201
Bush
1
202
BD11LB-202
Tailstock spindle
1
203
BD11LB-203
Key DIN 6885 - A 3 x 3 x 10
1
204
BD11LB-204
Clamping handle
1
205
BD11LB-205
Handle seat
1
206
BD11LB-206
Clamping lever
1
207
BD11LB-207
Threaded pin - M5 x 12
1
208
BD11LB-208
Lubricating nipple
1
209
BD11LB-209
Washer
1
210
BD11LB-210
Clamping piece spindle sleeve
1
211
BD11LB-211
Clamping piece spindle sleeve
1
212
BD11LB-212
Threaded pin - M5 x 12
2
213
BD11LB-213
Lubricating nipple
1
214
BD11LB-214
Piece of centering of spindle sleeve
1
215
BD11LB-215
Tailstock marking
1
216
BD11LB-216
Handlewheel
1
217
BD11LB-217
Nut
1
218
BD11LB-218
Spiral spring
1
219
BD11LB-219
Scales ring
1
220
BD11LB-220
Handle
1
221
BD11LB-221
Socket head screw DIN 912-M5X16
2
222
BD11LB-222
Washer DIN 6340-12
1
223
BD11LB-223
Tailstock
1
224
BD11LB-224
Tailstock base
1
225
BD11LB-225
Set Screw M8X45
2
226
BD11LB-226
Clamping plate
1
227
BD11LB-227
Hex cap bolt
1
228
BD11LB-228
Adjustment device
1
229
BD11LB-229
Threaded pin ISO 4028 - M6 x 16
1
230
BD11LB-230
Brass clamping piece
3
231
BD11LB-231
Socket head screw ISO 4028 - M6 x 10
3
232
BD11LB-232
Washer DIN 6340-8
233
BD11LB-233
Lock washer DIN 6340-10
4
234
BD11LB-234
Hex head cap screw DIN 912-M10X35
4
235
BD11LB-235
Machine bed
1
236
BD11LB-236
Rack
1
237
BD11LB-237
Hex head cap screwDIN 912-M6X16
6
238
BD11LB-238
Lead screw
1
239
BD11LB-239
Hex head cap screw DIN 912-M8X20
2
240
BD11LB-240
Lubricating nipple
1
241
BD11LB-241
Bearing 51102
2
242
BD11LB-242
Bracket
1
243
BD11LB-243
Round nut M12X1.25
2
244
BD11LB-244
Shaft sleeve
1
245
BD11LB-245
Spiral spring
1
246
BD11LB-246
Shaft sleeve
1
247
BD11LB-247
Eccentric sha
1
248
BD11LB-248
Locking handle
1
249
BD11LB-249
Motor
230V
1
250
BD11LB-250
Set Screw
4
251
BD11LB-251
Washer
4
252
BD11LB-252
Nut
4
253
BD11LB-253
Spring pin ISO 8752 - A4 x 24
1
254
BD11LB-254
Handle
1
Summary of Contents for 50000915M
Page 31: ......
Page 32: ...6 4 Exploded view of top slide ...
Page 34: ...6 5 Exploded view of cross slide ...
Page 36: ...6 6 Exploded view of apron ...
Page 38: ...6 7 Exploded view of lathe bed ...
Page 40: ...6 8 Exploded view of feed gear ...
Page 42: ...6 9 Exploded view of headstock ...
Page 44: ...6 10 Exploded view of change gear ...