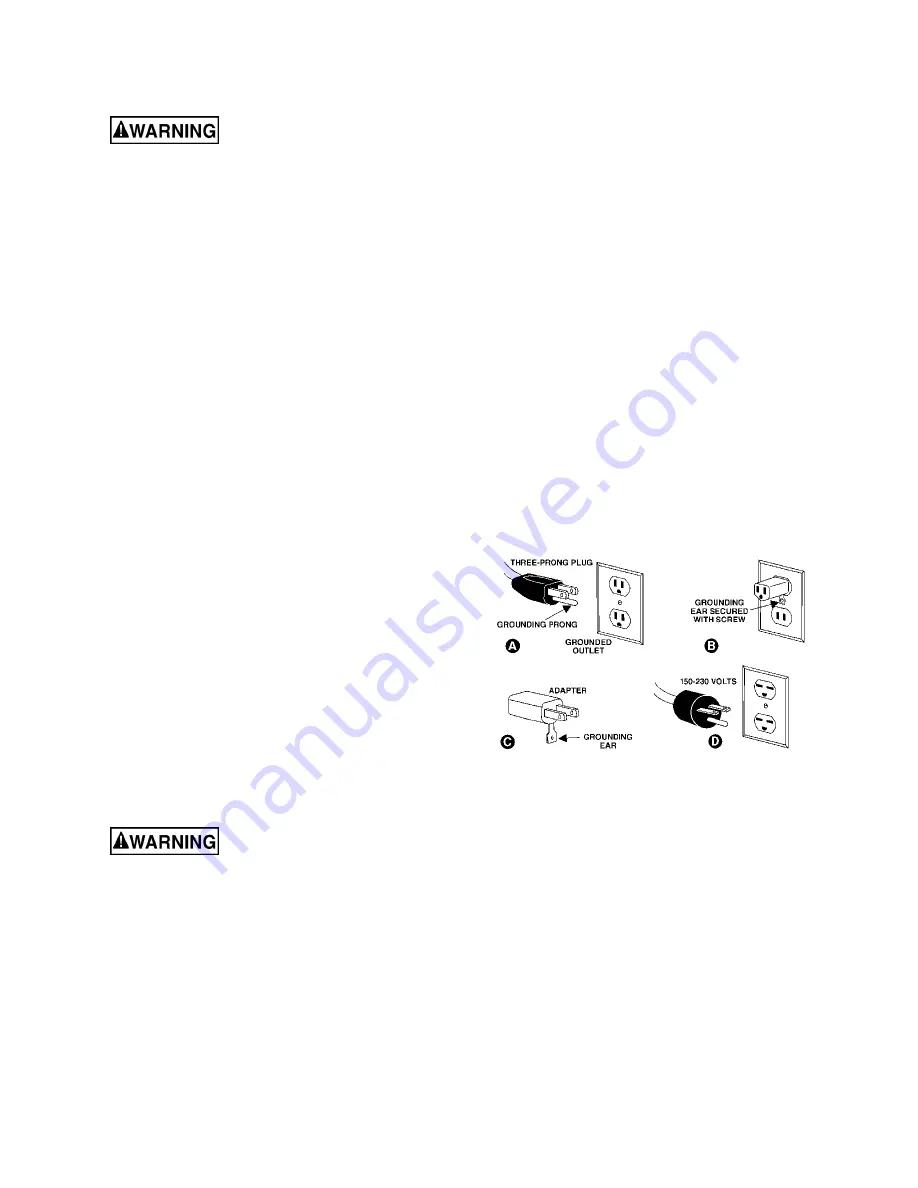
9
6.0
Electrical connections
Electrical connections must be
made by a qualified electrician in compliance
with all relevant codes. This machine must be
properly grounded to help prevent electrical
shock and possible fatal injury.
The SWG-272 and 272VS Square Wheel Grinder is
pre-wired for 115V power. It may be converted to
230V power; see
sect. 6.2.
It is recommended that the grinder be connected to
a dedicated minimum 15-amp circuit with circuit
breaker or fuse. If connected to a circuit protected
by fuses, use time-delay fuse marked “D”.
Local
codes take precedence over recommendations.
6.1
GROUNDING INSTRUCTIONS
1. All Grounded, Cord-connected Tools:
This machine must be grounded. In the event of a
malfunction or breakdown, grounding provides a
path of least resistance for electric current to reduce
the risk of electric shock. This tool is equipped with
an electric cord having an equipment-grounding
conductor and a grounding plug. The plug must be
plugged into a matching outlet that is properly
installed and grounded in accordance with all local
codes and ordinances.
Do not modify the plug provided - if it will not fit the
outlet, have the proper outlet installed by a qualified
electrician.
Improper connection of the equipment-grounding
conductor can result in a risk of electric shock. The
conductor with insulation having an outer surface
that is green with or without yellow stripes is the
equipment-grounding conductor. If repair or
replacement of the electric cord or plug is
necessary, do not connect the equipment-grounding
conductor to a live terminal.
Before connecting to power source, be sure the
switch is in
off
position.
Check with a qualified
electrician or service pe
r
sonnel if the grounding
instructions are not completely understood, or if
in doubt as to whether the tool is properly
grounded. Failure to comply may cause serious
or fatal injury.
Use only 3-wire extension cords that have 3-prong
grounding plugs and 3-pole receptacles that accept
the tool's plug.
Repair or replace damaged or worn cord
immediately.
2. Grounded, cord-connected tools intended for use
on a supply circuit having a nominal rating
less than
150
volts:
This tool is intended for use on a circuit that has an
outlet that looks like the one illustrated in
A,
Figure
6-1. An adapter, shown in
B
and
C
, may be used to
connect this plug to a 2-pole receptacle as shown in
B
if a properly grounded outlet is not available. The
temporary adapter should be used only until a
properly grounded. The green-colored rigid ear, lug,
and the like, extending from the adapter must be
connected to a permanent ground such as a
properly grounded outlet box.
In Canada, the use of a temporary adaptor is not
permitted by the Canadian Electrical Code, C22.1.
3. Grounded, cord-connected tools intended for use
on a supply circuit having a nominal rating between
150 - 250 volts
, inclusive:
This tool is intended for use on a circuit that has an
outlet that looks like the one illustrated in
D,
Figure
6-1. The tool is intended to be used with a grounding
plug that looks like the plug illustrated in
D
. Make
sure the tool is connected to an outlet having the
same configuration as the plug. No adapter is
available or should be used with this tool. If the tool
must be reconnected for use on a different type of
electric circuit, the reconnection should be made by
qualified service personnel; and after reconnection,
the tool should comply with all local codes and
ordinances.
Figure 6-1
6.2
Voltage conversion
The grinder is prewired for 115 volt input power, but
can be converted to 230 volt input, as follows.
6.2.1
Single speed model (SWG-272)
1. Open motor junction box cover, and reconnect
the leads according to diagram inside cover.
See
sect. 14.0
for similar diagram. (Note: In
case of discrepancy, diagram on junction cover
takes precedence.)
2. Remove existing plug from power cable and
attach a UL/CSA listed plug designed for 230V
power; or “hardwire” the machine directly to a
panel. If hardwiring make sure a disconnect is
provided for the operator.