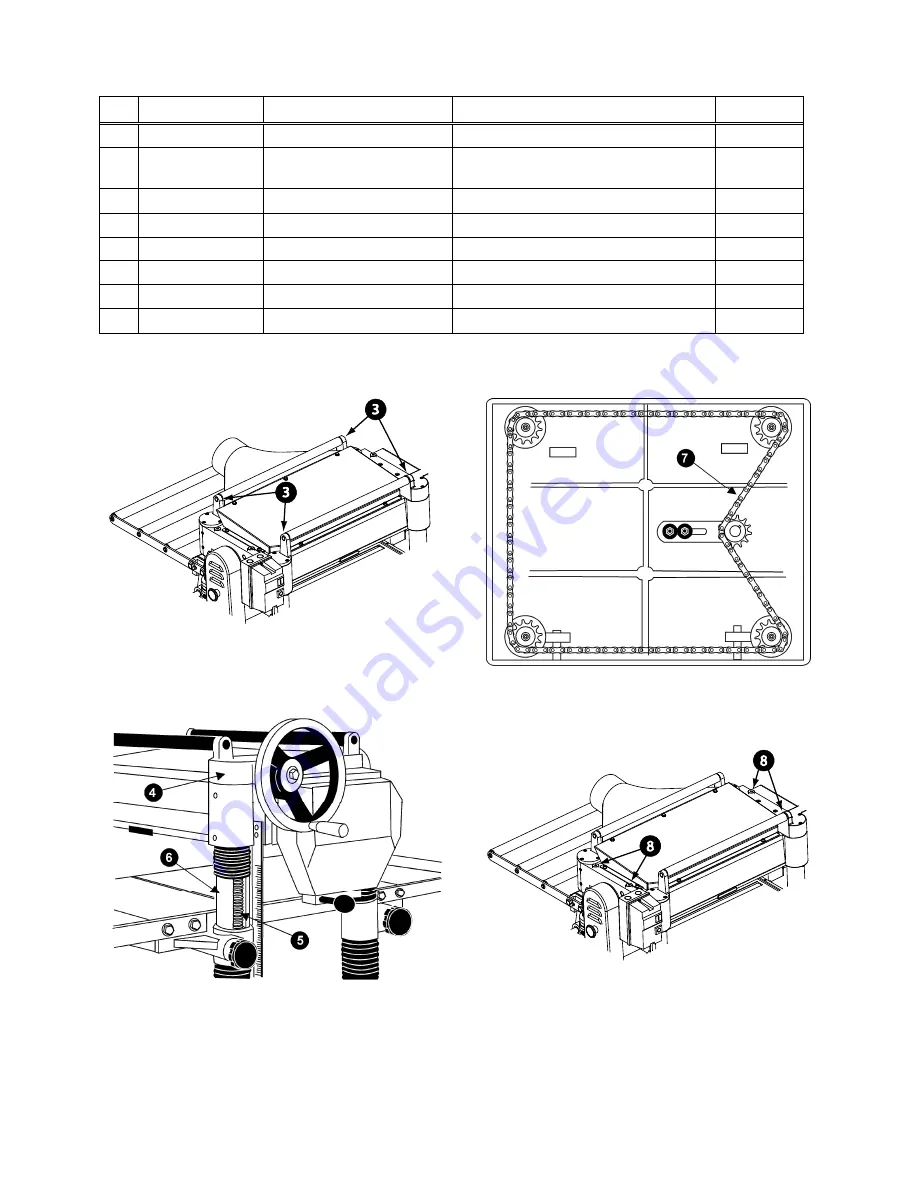
19
[The item numbers on this chart are referenced with the accompanying illustrations.]
No. Position
Interval
Suitable Types of Lubricant
Fig. No.
1
Drive Chain
Frequently
Grease
30
2
Gear Box
When operated more than
2,500 hours
70 to 90 weight gear oil
30
3
Return Rollers
Frequently
SAE-30
32
4
Worm Gear
Frequently
Grease
33
5
Lead Screw
Frequently
Grease
33
6
Column
Frequently
Clean and SAE-30
33
7
Table Chain
Frequently
Grease
34
8
Feed Rollers
Frequently
SAE-30
35
2
Figure. 31
Figure 32
Figure 33
Figure 34
Figure 35
Summary of Contents for 708528
Page 25: ...25 Head Assembly Exploded View ...
Page 29: ...29 Base and Column Assembly ...
Page 31: ...31 Gearbox Assembly ...
Page 33: ...33 230V 5HP Single Phase A2 14NO 17 13NO O ManAuto 97 95 96 98 R R 4T2 6T3 2T1 3L2 5L3 1L1 A1 ...
Page 34: ...34 230V 5HP Three Phase 4T2 ManAuto 97 A2 95 R 96 O R 14NO 6T3 17 98 2T1 3L2 13NO 5L3 1L1 A1 ...
Page 35: ...35 460V 5HP Three Phase 4T2 ManAuto 97 A2 95 R 96 O R 14NO 6T3 17 98 2T1 3L2 13NO 5L3 1L1 A1 ...
Page 36: ...36 427 New Sanford Road LaVergne Tennessee 37086 Phone 800 274 6848 www jettools com ...