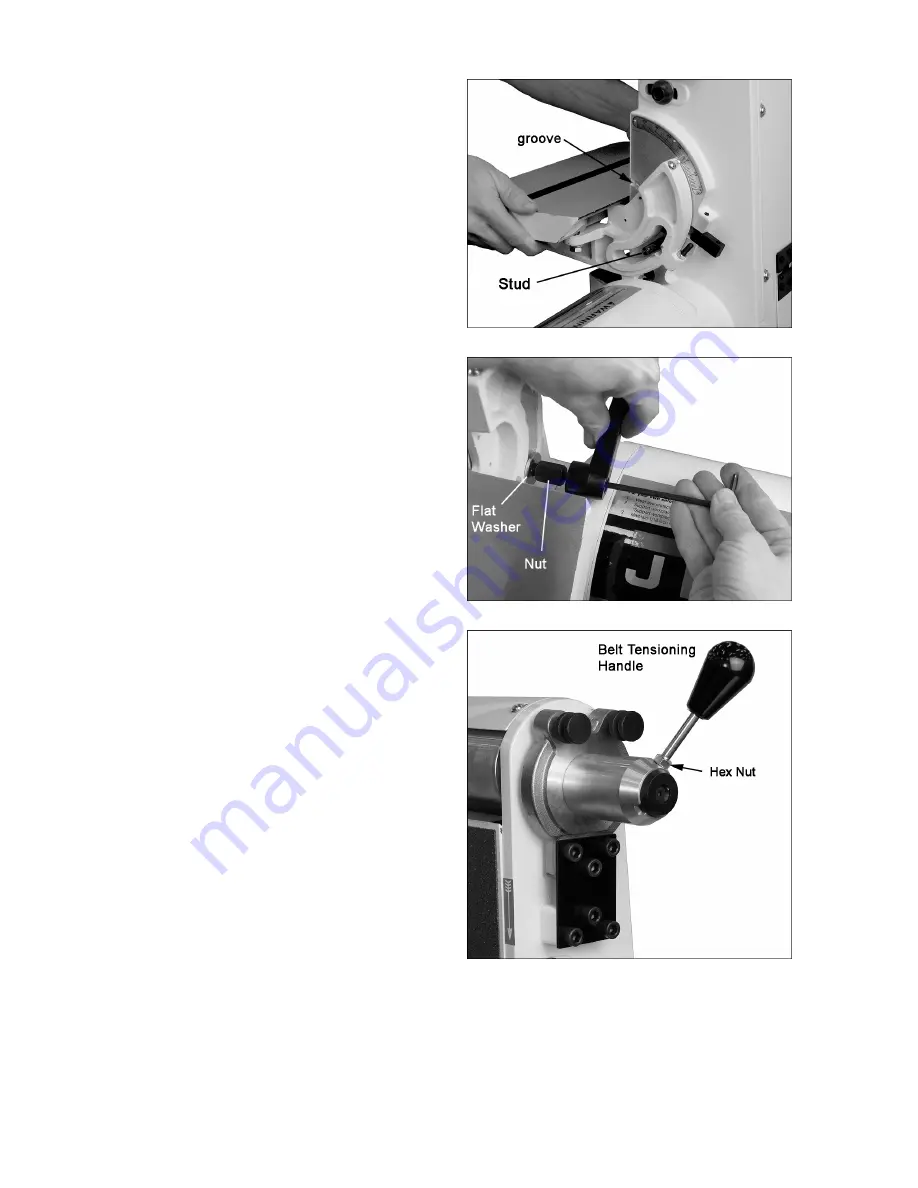
13
5. See “Adjustments” section for further
instruction on adjusting the disc table.
Belt Table
1. Loosen the sanding platen lock screw (E,
Figure 13) with a 6mm hex wrench, and tilt the
belt arm to a vertical position. Re-tighten the
lock screw.
2. Guide the belt table trunnion onto the stud, as
shown in Figure 14. The raised track on the
trunnion must fit into the groove on the belt
arm.
3. Place the remaining M10 flat washer onto the
stud (Figure 15).
4. Thread the nut of the table lock handle (Figure
15) onto the stud. To do this quickly, pull out
on the handle, while tightening the nut with a
4mm hex wrench. When the nut is fully
tightened onto the stud, release the handle,
making sure it seats itself back onto the nut.
Note:
The table lock handle can be
repositioned at any time for convenience by
pulling out on the handle, rotating it to new
position, then releasing it. Make sure it re-
seats itself on the nut.
5. Screw the belt tensioning handle (Figure 16)
into the threaded hole in the belt tracking
assembly, and tighten the hex nut against the
shaft with a 13mm wrench.
6. See “Adjustments” section for further
instruction on adjusting the belt table.
Installing Abrasives
Abrasive Disc
Note: You may wish to check the angle setting of
the table before installing the abrasive disc. See
“Disc Table Adjustment”.
To install the abrasive disc:
1. Disconnect machine from power source.
2. Make sure the aluminum disc is clean and dry.
3. Peel the backing from the abrasive and
carefully insert it between disc and table; align
and press into place.
4. Rotate disc a half turn and press other half of
abrasive into place. Make sure to remove any
entrapped air by pressing all parts of the
abrasive against the disc.
Figure 13
Figure 14
Figure 15
Figure 16