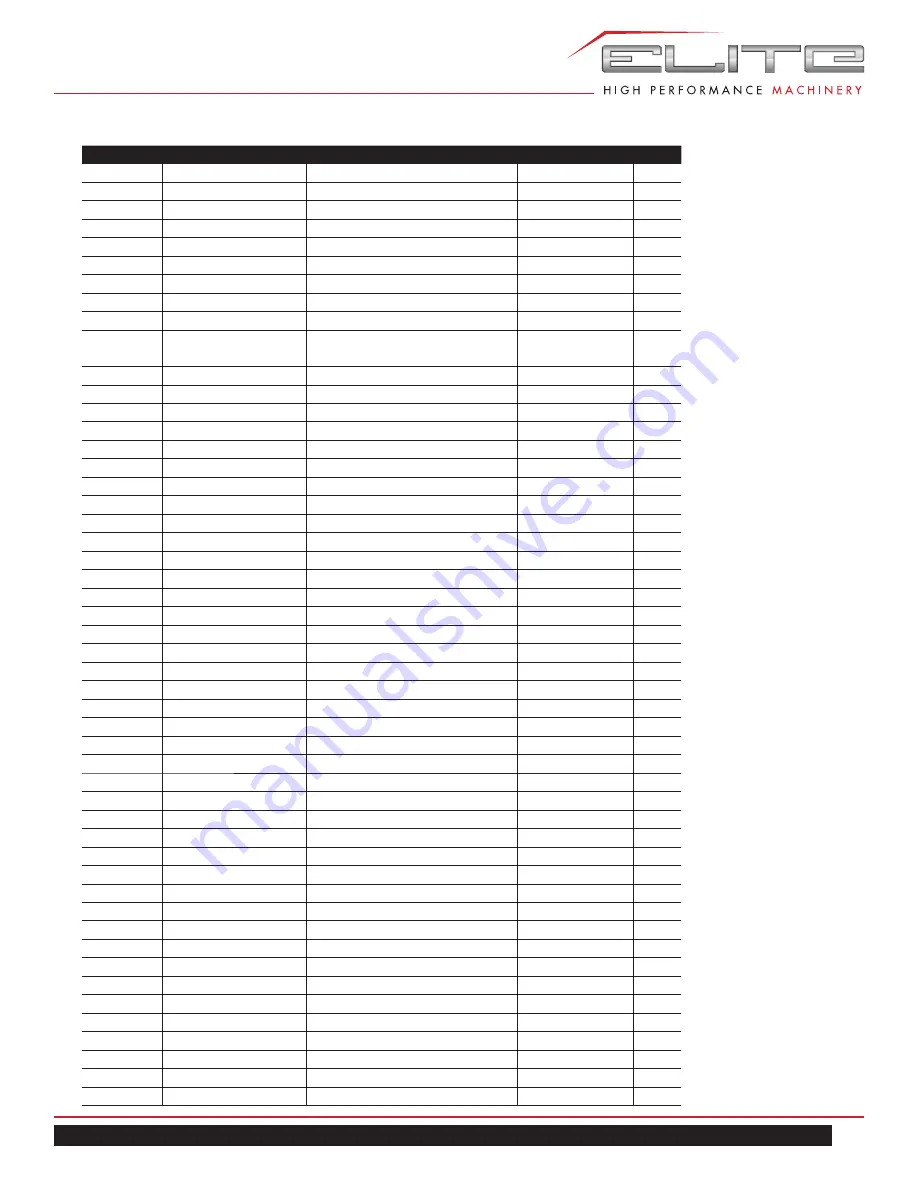
27
EVBS-20
Index No. Part No.
Description
Size
Qty.
48
EVBS20-1320
Blade Guide
4
49
EVBS20-1331
Blade Stopper, Upper
1
50
EVBS20-1332
Blade Stopper, Lower
1
51
VBS2012-1333
Eccentric Shaft
1
52
EVBS20-1350
Blade Guide Post
1
53
EVBS20-1360
Guide Post Housing
1
54
EVBS20-1361
Post Clamping Spring
1
55
EVBS20-1370
Blade Guard, Left
1
56
EVBS20-1381
Blade Guard, Right
1
56N
EVBS26-1380
Blade Guard Assembly (s/n
13082031 and higher)
1
57
EVBS20-1390
Post Housing Pin
1
58
EVBS20-9017
Guide Post Lock
1
59
EVBS20-9211
Handle Knob
1
60
BB-6201
Ball Bearing
1
61
VBS2012-2000
Main Drive Motor
1
61-1
EVBS20-2001
Air Pump
2HP 230V 3Ph 1
EVBS20-2001N
Air Pump
115V
1
62
EVBS20-2010
Motor Pulley
1
63
EVBS20-2020
Motor Seat
1
64
VB-A56
V-Belt, 7071+2010
A56
2
65
VBS2012A-301
Lower Wheel
1
66
VBS2012A-302
Rubber Tire
2
67
VBS2012-3030
Taper Sleeve
1
68
VBS2012-3040
Wheel Locking Nut
1
69
VBS2012A-305
Upper Wheel
1
70
VBS2012-3060
Upper Wheel Lock
1
71
VBS2012-3080
Slide Block Housing
1
72
VBS2012-3090
Slide Block Seat
1
73
VBS2012-3100
Slide Block Guide
2
74
VBS2012-3110A
Upper Wheel Slider
1
75
EVBS20-3116
Slider Screw Shaft
1
76
VBS2012-3120
Wheel Elevate Shaft
1
77
VBS2012-3121
Spring
1
78
VBS2012-3150
Washer
1
79
VBS2012-3180
Indicator Ring
3
80
VBS2012-3190
Tension Indicator
1
81
VBS2012-3200
Wheel Tilt Adjuster
1
82
VBS2012-3220
Wheel Tilt Connecter
1
83
VBS2012-3240
Connecter Washer
1
84
EVBS20-3251
Connecter Housing
1
85
VBS2012-8712
Indicator Plate
1
86
EVBS20-9031
Handwheel
1
87
EVBS20-9061
Tilt Adjust Handwheel
1
88
BB6305
Ball Bearing
6305
2
89
EVBS20-4011
Air Pump Housing
1
90
EVBS20-4021
Air Pump Cover
1
91
EVBS20-4031
Air Pump Rotator
1
92
EVBS20-4050
Air Pump Leave
4
93
EVBS20-4071
Connect Shaft
1
94
VBS2012-4140
Air Outlet
1
Summary of Contents for 891100
Page 34: ...34 Vertical Band Saw 19 0 WIRING DIAGRAM ...
Page 35: ...35 EVBS 20 NOTES ...
Page 36: ...36 Vertical Band Saw NOTES ...