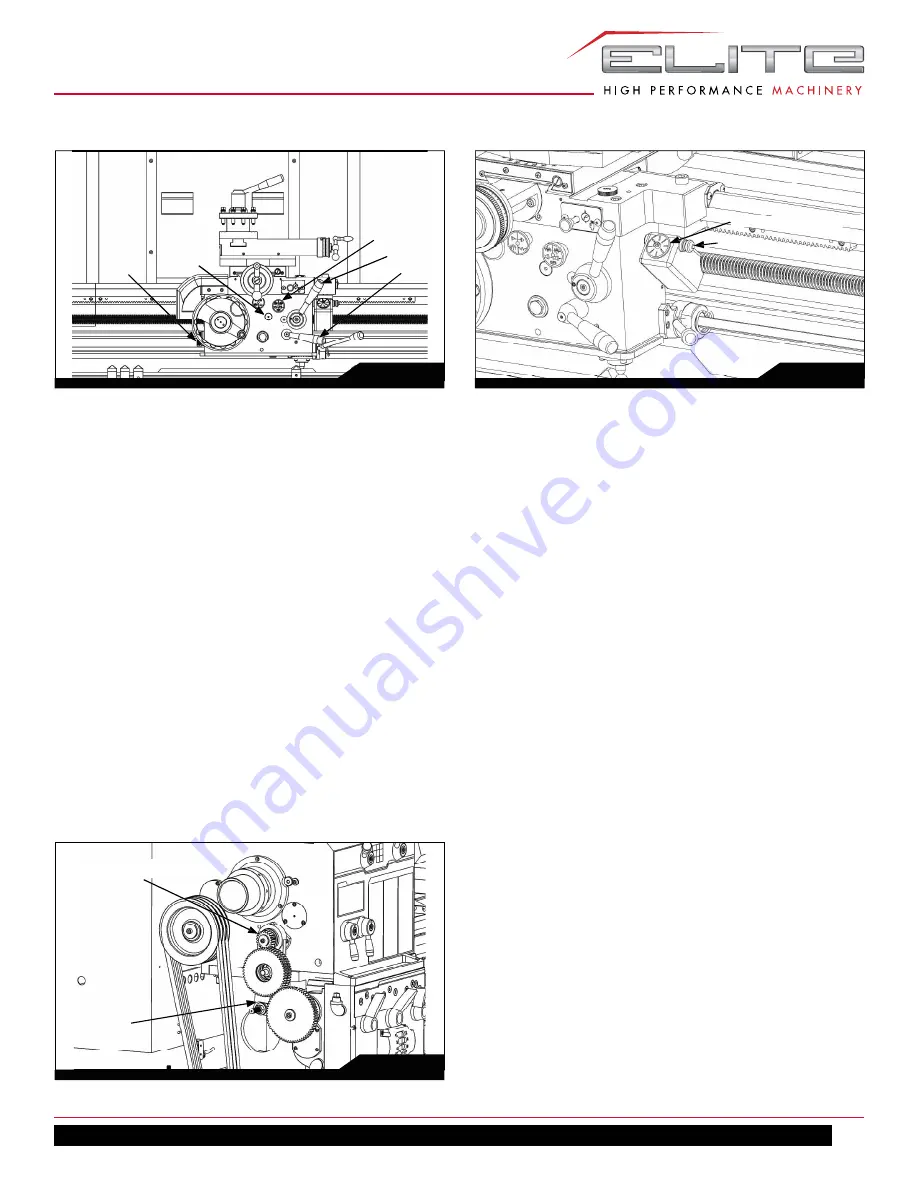
17
EGH1740 | EGH1760
Fig. 18
9.6 THREADING DIAL INDICATOR
For threads cutting:
• Tighten the handnut to retain indicator in when
engaging the indicator with the leadscrew. When not
required, release hand-nut and swing indicator out of
engagement.
•
To cut threads with an even number per inch, the
leadscrew nut can be closed as any line on the dial
passes the datum mark.
• To cut threads with an odd number per inch, close
the leadscrew nut at any NUMBERED line.
• Fractional threads of 1/2 or 1/4 T.P.I. may be cut by
closing the nut at the SAME NUMBERED LINE on
each pass of the tool.
• This dial can not be used with an IMPERIAL
leadscrew to cut metric threads, D.P., M.P. which are
shown on gear box data plate. For the threads being
shown, the leadscrew nut must be kept closed. Use
apron control lever after each thread cutting when
the tool is withdrawn to original start of thread cutting
operation.
Fig. 19
Multi-start threads can be cut on a lathe in three ways:
1. By repositioning the compound (top) slide one pitch
forward for each start. Note that the slide is normally
set at 90º to the axis of the machine cross-slide. The
accuracy of this method depends upon the skill of
the operator.
2. By using an accurately divided driver plate and
turning the work-piece one division forward for each
start.
3. By advancing the driver gear a calculated number
of turns to advance the spindle by one pitch of the
thread to be cut. The accuracy of this method is
that of the machine.
• With all series lathes, two ratios exist between
the spindle and driver gear shift, i.e. the LOW
range where the ratio is 1:2 and the HIGH range
where the ratio is 2:1
• In order to use this method, the number of
teeth on the driver gear must be divisible by
the number of starts being cut. The driver gear
is then advanced by half this number of teeth
when in LOW range. And conversely, by twice
the number of teeth when in HIGH range.
• On the standard end gear train for this machine
the driver gear has 24 teeth; so that two, three
or four start threads, can readily be cut. For
other odd numbers of start a choice must be
made of methods 1 or 2.
9.7 CROSS SLIDE AND TOP SLIDE
•
A solid topslide is fitted as standard equipment to
the cross-slide mounted on a swivel base which is
marked 0-90-0-90º for accurate indexing.
•
Handwheel dials are graduated in inch or metric
divisions to suit the operation.
A
D
C
Fig. 20
Handnut
Threading dial indicator
F
Gear 24T for Imperial leadscrew
(Gear 28T/22T for Metric leadscrew)
End Gear Train
Summary of Contents for 892100
Page 21: ...21 EGH1740 EGH1760 HEADSTOCK ASSEMBLY ...
Page 22: ...22 1700 Series Lathe HEADSTOCK ASSEMBLY ...
Page 23: ...23 EGH1740 EGH1760 HEADSTOCK ASSEMBLY ...
Page 24: ...24 1700 Series Lathe HEADSTOCK ASSEMBLY ...
Page 28: ...28 1700 Series Lathe GEARBOX ASSEMBLY ...
Page 29: ...29 EGH1740 EGH1760 GEARBOX ASSEMBLY ...
Page 33: ...33 EGH1740 EGH1760 APRON L H ASSEMBLY ...
Page 34: ...34 1700 Series Lathe APRON L H ASSEMBLY ...
Page 39: ...39 EGH1740 EGH1760 4 WAY TOOL POST ...
Page 41: ...41 EGH1740 EGH1760 SADDLES ASSEMBLY ...
Page 42: ...42 1700 Series Lathe SADDLES ASSEMBLY 2 ...
Page 45: ...45 EGH1740 EGH1760 BED AND SHAFTS ASSEMBLY ...
Page 48: ...48 1700 Series Lathe END GEAR ASSEMBLY ...
Page 50: ...50 1700 Series Lathe MAIN MOTOR ASSEMBLY ...
Page 52: ...52 1700 Series Lathe CABINET AND PANEL ASSEMBLY FRONT MOVEABLE CHIP TRAY OPTIONS ...
Page 56: ...56 1700 Series Lathe CONVENTIONAL TAILSTOCK ASSEMBLY ...
Page 58: ...58 1700 Series Lathe STEADY REST ASSEMBLY ...
Page 62: ...62 1700 Series Lathe 892156 5C COLLET CLOSER OPTIONAL ...
Page 64: ...64 1700 Series Lathe 892157 TAPER ATTACHMENT OPTIONAL ...