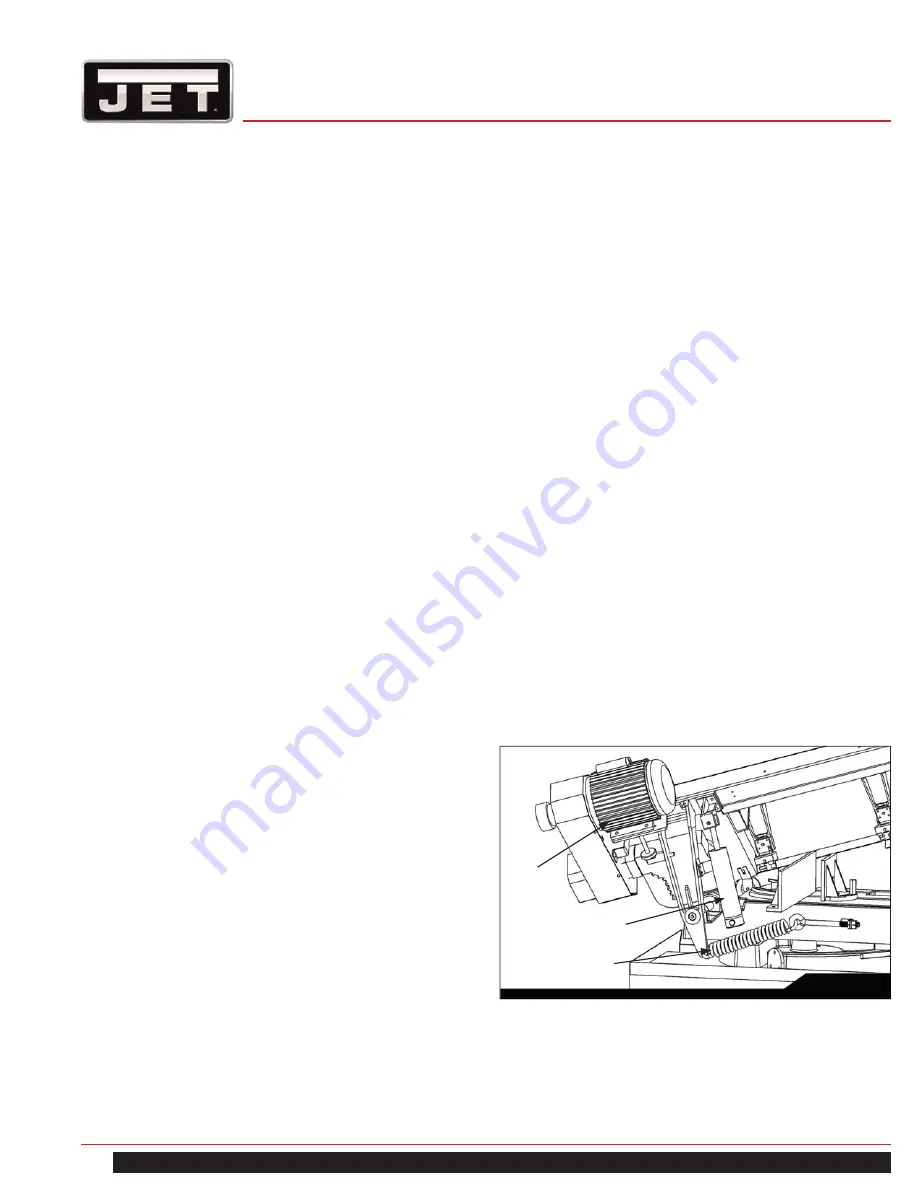
10
8-in x 13-in Horizontal Cut-Off Bandsaw
11.1 HYDRAULIC FEED CONTROL
The weight of the saw head provides the force needed to
cut through the workpiece. The cut-off saw has a hydraulic
cylinder that controls the feed rate of the saw.
The hydraulic feed control circuit consists of a single acting
hydraulic cylinder (Figure 7) and a feed rate control (Figure
4). The feed control cylinder resists motion in the downward
direction to control the feed rate. The control cylinder offers
no resistance when raised upward.
The feed rate control knob (Figure 4) controls the rate at
which the saw head is lowered. The control knob (needle
valve) controls the rate at which the hydraulic fluid is
released from the hydraulic cylinder. When the needle
valve is closed, the cylinder is locked. With the needle valve
slightly open, the cylinder permits slow, or light, downward
force. Opening the needle valve further increases the feed
rate and applies more force to the saw blade and workpiece.
The needle valve is adjusted until the saw is operating ef-
ficiently. The efficiency of operation is usually evaluated
by observing chip formation. Blade efficiency is further de-
scribed on the following page.
11.0 OPERATIONS
10.0 BLADE SELECTION
The cut-off saw is delivered with a saw blade that is
adequate for a variety of cut-off jobs on a variety of common
materials.
Refer to Figure 6 for the speeds recommended for various
materials. These speeds, while appropriate for many
common shop cutting needs, do not encompass the wide
variety of special blade configurations (tooth pitch and set)
and special alloys for cutting unusual or exotic materials.
A coarse blade could be used for a solid steel bar, but a
finer tooth blade would be used on a thin-wall steel tube.
In general, the blade choice is determined by the thickness
of the material; the thinner the materials; the finer the tooth
pitch.
A minimum of three teeth should be on the workpiece at all
times for proper cutting. The blade and workpiece can be
damaged if the teeth are so far apart that they straddle the
workpiece.
For very high production on cutting of special materials, or
difficult to cut materials such as stainless steel, tool steel,
or titanium, you can ask your industrial distributor for more
specific blade recommendations. The supplier that provides
the workpiece material should be able to provide you with
very specific instructions regarding the best blade (and
coolant or cutting fluid, if needed) for the material or shape
supplied.
10.1 BLADE BREAK-IN PROCEDURES
New blades are very sharp and, therefore, have a tooth
geometry that is easily damaged if a careful break-in
procedure is not followed. Consult the blade manufacturer’s
literature for break-in of specific blades on specific materials.
However, the following procedure will be adequate for break-
in of Jet-supplied blades on lower alloy ferrous materials:
1. Clamp a section of round stock in the vise. The stock
should be 2 inches or larger in diameter.
2. Operate the saw at low speed. Start the cut with a
very light feed rate.
3. When the saw has completed 1/3 of the cut, increase
the feed rate slightly and allow the saw to complete
the
cut.
4. Keep the hydraulic cylinder needle valve in the same
position and begin a second cut on the same or
similar
workpiece.
5. When the blade has completed about 1/3 of the cut,
increase the feed rate.
Watch the chip formation until cutting is at its most
efficient rate and allow the saw to complete the cut
(refer
to
Evaluating Cutting Efficiency
section 11.2).
The blade is now considered ready for use.
Fig. 7
Counterweight Spring
Hydraulic Cylinder
Drive
Motor