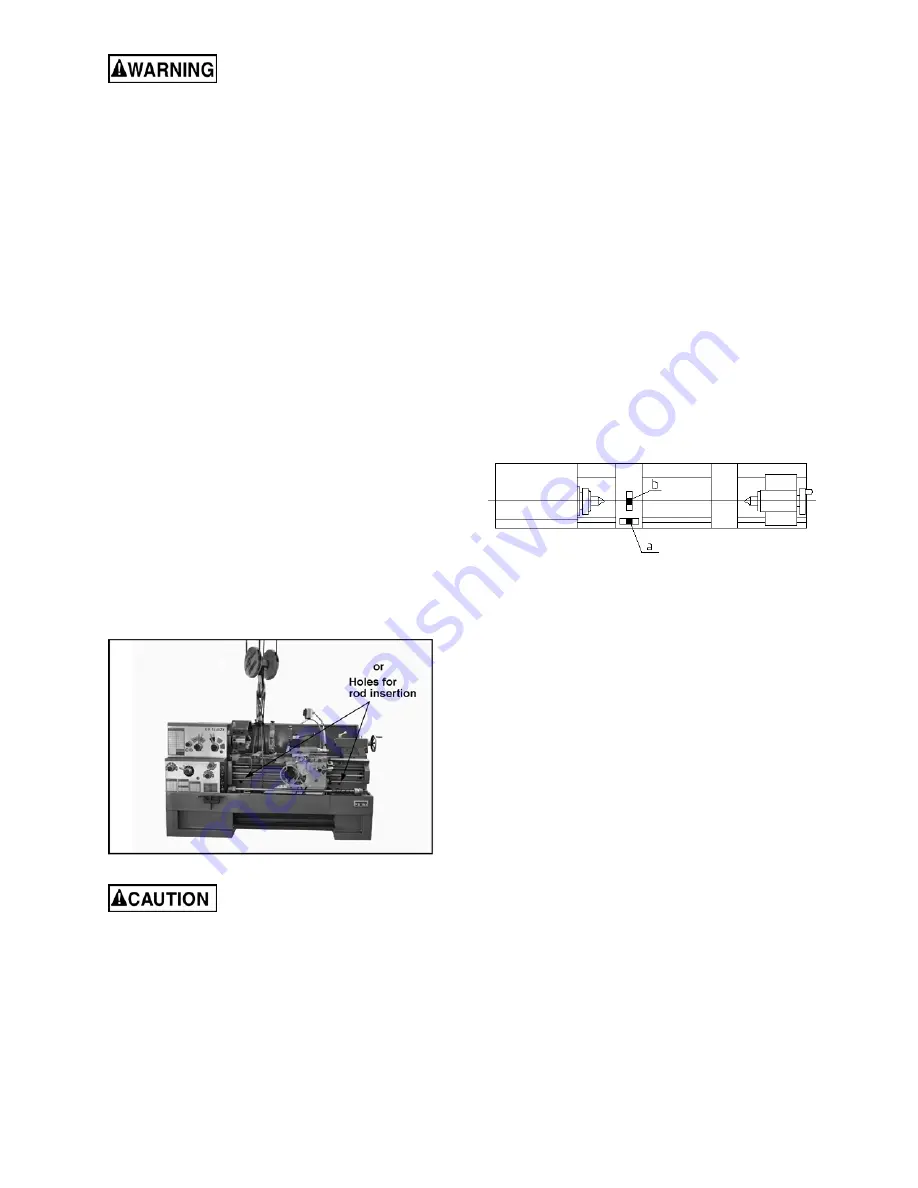
13
Read and understand the
entire contents of this
manual before attempting set-up or operation!
Failure to comply may cause serious injury.
8.0
Installation
1. Finish removing all crate material from around
the lathe.
2. Unbolt lathe from shipping pallet.
3. Choose a location for the lathe that is dry and
has sufficient illumination (consult OSHA or
ANSI standards for recommended lighting
levels in workshop environments).
4. Allow enough room to service the lathe on all
four sides, and to load and off-load work
pieces. In addition, if bar work is to be
performed, allow enough space for stock to
extend out the headstock end. If used in
production operations, leave enough space for
stacking unfinished and finished parts.
5. The foundation must be solid to support the
weight of the machine and prevent vibration,
preferably a solid concrete floor.
6. Sling the lathe as shown in Figure 4; either
below the bed at center of gravity area, or
around steel rods or pipes of sufficient strength
inserted through the holes in the bed casting.
Do not lift lathe by the spindle.
With
adequate lifting equipment, slowly raise the
lathe off the shipping pallet. Make sure lathe is
balanced before moving.
Figure 4: Lifting the lathe
Confirm that all suspension
equipment is properly rated and in good
condition for lifting lathe. Do not allow anyone
beneath or near load while lifting.
7. The lathe can be placed upon the cast iron
leveling pads under each foot hole, and
adjusted using the adjusting bolts with hex
nuts. Or, it may be secured to the floor using
bolts placed head-down in the concrete, and
using shims where needed to level the
machine. Refer to Figure 1 for mounting hole
dimensions.
8.1
Leveling the lathe
It is imperative that the lathe be on a level plane;
that is, where headstock and tailstock center points
remain aligned throughout the tailstock travel, with
the bed ways absent of twist and thus parallel to
the operational center line.
A lathe which is not properly leveled will be
inaccurate,
producing tapered cuts. Also, the
center point of the tailstock will vary as it is
positioned along the bed, thus requiring constant
readjustment of the set of the tailstock.
8. Use a machinist’s precision level on the bed
ways both front to back and side to side, as
shown in Figure 5. Take the reading in one
direction every ten inches. Make sure the ways
are clean and free of any debris before placing
a level upon them.
9. Deviation over bed length
(see Figure 5)
:
a) Maximum
0.02/1000mm
b) Maximum
0.04/1000mm
Figure 5: Leveling
10. Tighten foot screw nuts evenly to avoid
distortion.
11. Leveling should be inspected occasionally,
and especially if the accuracy of the lathe
begins to diminish.
8.2
Completing installation
12. Clean all rust protected surfaces using a mild
commercial solvent, kerosene or diesel fuel.
Do not use paint thinner, gasoline, or lacquer
thinner. These will damage painted surfaces.
Cover all cleaned surfaces with a light film of
20W machine oil.
13.
Open the end gear cover. Clean all
components of the end gear assembly and
coat all gears with a heavy, non-slinging
grease. Close the end gear cover.
Summary of Contents for GH-1440ZX
Page 26: ...26 T H R E A D I N G C H A R T I N I N C H ...
Page 27: ...27 m m M E T R I C T H R E A D I N G C H A R T M P M O D U L E P I T C H ...
Page 31: ...3 1 1 Stand Assembly Exploded View ...
Page 34: ...6 2 1 Brake Assembly Exploded View ...
Page 36: ...8 3 1 Bed Assembly Exploded View ...
Page 39: ...11 4 1 Headstock Assembly I Exploded View ...
Page 43: ...15 5 1 Headstock Assembly II Exploded View ...
Page 46: ...18 6 1 Headstock Assembly III Exploded View ...
Page 48: ...20 7 1 Headstock Assembly IV Exploded View ...
Page 50: ...22 8 1 Change Gear Box Assembly I Exploded View ...
Page 52: ...24 9 1 Change Gear Box Assembly II Exploded View ...
Page 54: ...26 10 1 Quick Change Gear Box I Exploded View ...
Page 57: ...29 11 1 Quick Change Gear Box II Exploded View ...
Page 59: ...31 12 1 Quick Change Gear Box III Exploded View ...
Page 61: ...33 13 1 Apron Assembly I Exploded View ...
Page 64: ...36 14 1 Apron Assembly II Exploded View ...
Page 67: ...39 15 1 Apron Assembly III Exploded View ...
Page 69: ...41 16 1 Carriage Assembly Exploded View ...
Page 73: ...45 18 1 Carriage Stop Assembly Exploded View ...
Page 75: ...47 19 1 Quick Change Tool Post Exploded View ...
Page 77: ...49 20 1 Tailstock Assembly I Exploded View ...
Page 79: ...51 21 1 Tailstock Assembly II Exploded View ...
Page 81: ...53 22 1 Steady Rest Assembly Exploded View ...
Page 83: ...55 23 1 Follow Rest Assembly Exploded View ...
Page 85: ...57 24 1 Coolant Work Light Assembly Exploded View ...
Page 89: ...61 26 2 Electrical Cabinet Breakdown 6 7 8 12 11 10 17 22 21 23 13 9 9a 20 18 3a 1 2 4 19 3 ...
Page 90: ...62 27 0 Wiring Diagram ...
Page 94: ...66 427 New Sanford Road LaVergne Tennessee 37086 Phone 800 274 6848 www jettools com ...