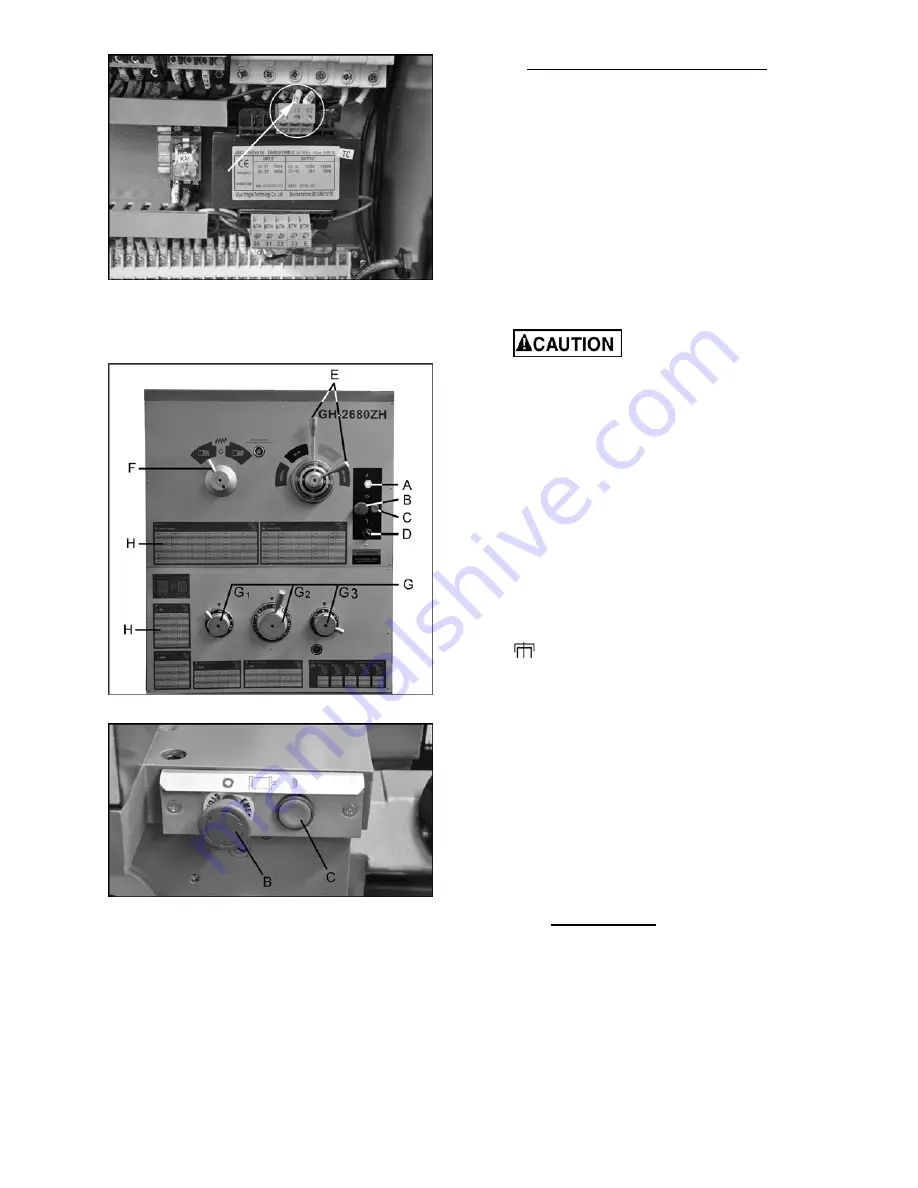
18
Figure 21 – Transformer rewiring
11.0
Basic Controls
Figure 22 – Headstock Controls
Figure 23 – Alternate controls
1.
Control Panel:
Located on front of headstock.
An abbreviated control panel is also mounted
to front of carriage.
•
Power Indicator Light
(A, Figure 22).
Illuminates whenever lathe is receiving
power.
•
Emergency Stop Button
(B, Figure 22 and
23). Shuts down all machine functions.
NOTE:
Lathe will still have power.
Twist
button clockwise to reset.
•
ON Button
(C, Figure 22 and 23). Activates
motor.
•
Coolant On-Off Switch
(D, Figure 22).
Activates coolant pump.
2.
Speed Selection Levers
(E, Figure 22):
Located on front of headstock. Move levers left
or right to desired spindle speed, according to
accompanying chart on the dial.
3.
Feed Direction Lever
(F, Figure 22): Located
on front of headstock. Moving the lever
changes direction of feed. Center position is
neutral.
Do not move feed direction
lever while machine is running.
4.
Thread Pitch and Feed Selector Levers
(G,
Figure 22): Located on front of headstock, are
used conjunctively to set up for threading or
feeding, according to the accompanying chart
(H).
Lever G
1
is used to control/change between
the different thread styles, and is also used for
altering the feed setting.
The symbols on the dial are identified as
follows:
mm
= metric threads
IN
= inch threads
MP
= module pitch
DP
= diametral pitch
= when this position is selected, the
input shaft of the gearbox is directly
connected to the lead screw, and will
bypass the gearbox.
This function is available for cutting special
thread forms or nonstandard thread forms,
which are not covered by the standard
gearbox drive train set-up.
Note: Control dial
G
3
must be set to position
○
for this operation.
Example:
The current standard set of gears
installed with the machine are 82, 97, and
81. This will give a thread pitch equal to
0.506” (12.857mm).
Calculating pitch:
P=(82/97) x (97/81) = 0.6061” (12.857mm)
2
Nonstandard threads are attained by
changing gears in the gear train, based on
this calculation.
Lever G
2
selects the pitch of the thread and the
feed/revolution.
Lever G
3
doubles the thread pitch or
feeddependent on the following positions:
Summary of Contents for GH-26120ZH
Page 34: ...34 18 0 Change Gear Diagram Figure 54 ...
Page 35: ...35 This page intentionally left blank ...
Page 40: ...4 1 1 Bed Assembly I Exploded View ...
Page 41: ...5 1 2 Bed Assembly I for 120 ZH only Exploded View ...
Page 44: ...8 2 1 Bed Assembly II Exploded View ...
Page 45: ...9 2 2 Bed Assembly II for 120 ZH only Exploded View ...
Page 48: ...12 3 1 Headstock Assembly I Exploded View Ⅲ Ⅳ Ⅴ Ⅶ Ⅵ Ⅱ Ⅰ Ⅱb Ⅶb ZⅡ ZⅠ ZⅡ ...
Page 51: ...15 4 1 Headstock Assembly II Exploded View ...
Page 54: ...18 5 1 Headstock Assembly III Exploded View ...
Page 56: ...20 6 1 Headstock Assembly IV Exploded View Ⅰ Ⅱb Ⅱ Ⅲ Ⅳ Ⅴ ...
Page 59: ...23 7 1 Headstock Assembly V Exploded View Ⅶ Ⅶb Ⅵ ...
Page 62: ...26 9 1 Gear Box Assembly I Exploded View Ⅱ Ⅲ Ⅰ ...
Page 64: ...28 10 1 Gear Box Assembly II Exploded View ...
Page 67: ...31 11 1 Gear Box Assembly III Exploded View ...
Page 70: ...34 12 1 Brake Assembly Exploded View ...
Page 72: ...36 13 1 Saddle and Cross Slide Assembly Exploded View ...
Page 75: ...39 14 1 Tool Post and Compound Rest Assembly Exploded View ...
Page 77: ...41 15 1 Apron Assembly I Exploded View Ⅱ Ⅹ Ⅱ Ⅲ Ⅷ Ⅹ Ⅸ Ⅹ Ⅳ Ⅰ Ⅹ Ⅰ Ⅵ Ⅲ Ⅴ Ⅶ ...
Page 80: ...44 16 1 Apron Assembly II Exploded View Ⅺ Ⅹ Ⅲ Ⅻ Ⅸ Ⅹ Ⅶ ...
Page 83: ...47 17 1 Apron Assembly III Exploded View Ⅰ Ⅱ Ⅴ Ⅲ Ⅳ Ⅵ ...
Page 85: ...49 18 1 Apron Assembly IV Exploded View ...
Page 87: ...51 19 1 Tailstock Assembly I Exploded View ...
Page 89: ...53 20 1 Tailstock Assembly II Exploded View ...
Page 91: ...55 21 1 Steady Rest Assembly Small and Large Exploded View ...
Page 95: ...59 24 1 Travel Stop Assembly Exploded View ...
Page 100: ...64 27 2 Electrical Diagram ...