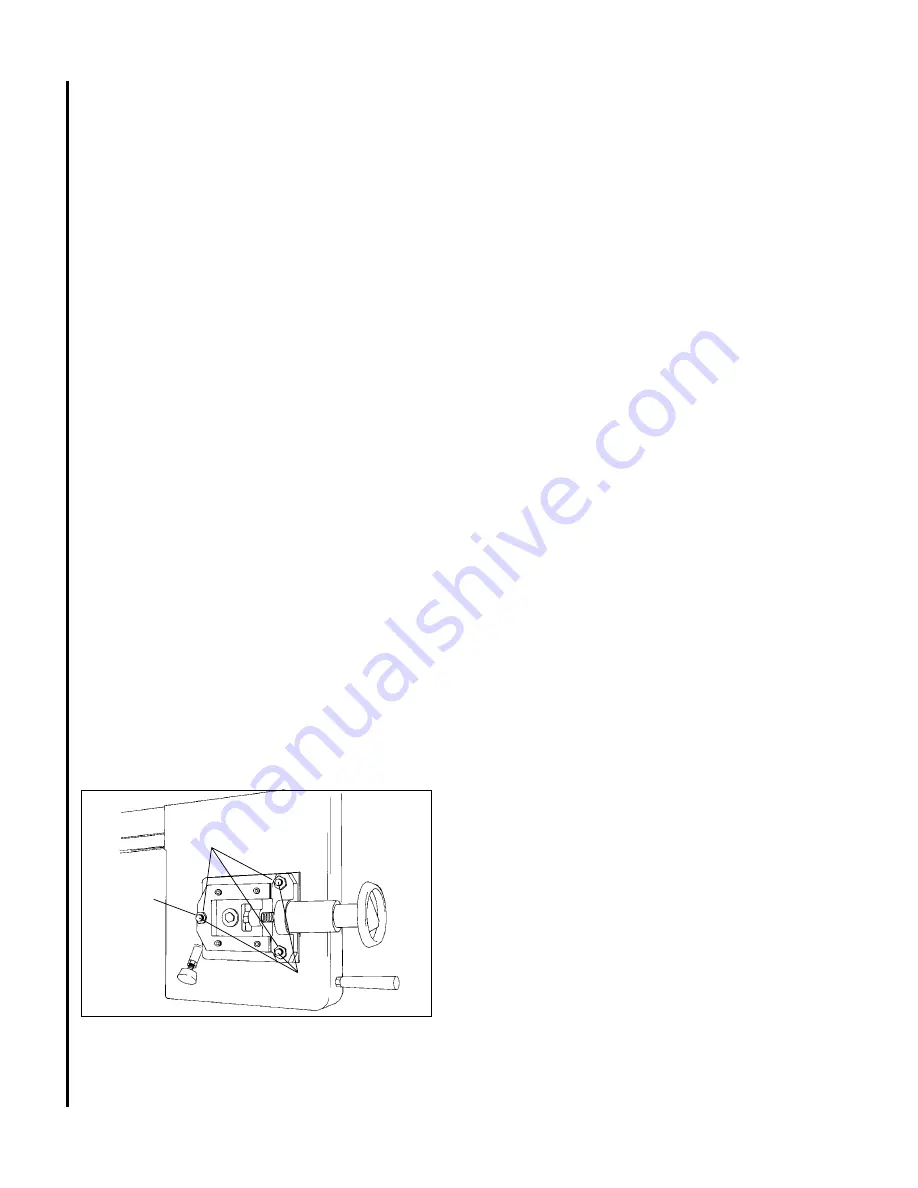
12
Coolant Mixture and Quantity
The general purpose coolant is a mixture of water
soluble oil and water. Mix one part of soluble oil
(TRIM SOL) to ten parts of water (one quart oil, ten
quarts of water). The eleven quarts of coolant is the
amount required for the coolant pump to operate
properly.
There are numerous coolants on the market that
are formulated for special applications. Consult your
local distributor for details in the event you have a long
range production task, or are required to cut some of
the more exotic materials.
Adjustments
The efficient operation of the cut-off saw is depen-
dent upon the condition of the saw blade. If the
performance of the saw begins to deteriorate, the first
item that you should check is the blade.
If a new blade does not restore the machine’s
cutting accuracy and quality, refer to the Trouble-
shooting section (or the blade manufacturer's guide)
for conditions to consider and adjustments that can be
made to increase the life of the blade.
To change the blade, refer to
Changing Blades
in
the Maintenance section. To adjust the blade track-
ing, refer to the following procedures.
Blade Tracking Adjustment
Blade tracking has been tested at the factory. Adjust-
ment is rarely required when the blade is used
properly or if the blade is correctly welded. (See
figure 12 for location of blade tracking adjustment
screws.)
Factory or Field Procedure
1. Raise the saw head enough to allow the saw
motor to operate.
2. Loosen four knobs securing the blade cover. Lift
the cover and swing it backward.
3. Remove the blade guard mounted on the left blade
guide support.
4. Remove both blade guide bearing brackets.
NOTE:
Maintain proper tension at all times using the
blade tensioning mechanism.
5. Loosen the center locking screws in all three hex
adjustment screws on the blade tensioning
mechanism (see figure 12).
CAUTION:
WHILE PERFORMING THE FOLLOW-
ING, KEEP THE BLADE FROM RUBBING EXCES-
SIVELY ON THE SHOULDER OF THE WHEEL.
EXCESSIVE RUBBING WILL DAMAGE THE WHEEL
AND/OR THE BLADE.
6. Start the saw. Slowly turn the single hex adjust-
ment screw at the rear of the tracking mechanism
to tilt the idler wheel. Do not turn either of the
other two adjustment screws. Turn the adjust-
ment screw until the blade is touching the shoul-
der of the idler wheel.
NOTE:
Turning the screw inward causes the blade to
move toward the shoulder of the wheel. Turning the
screw outward causes the blade to move away from
the shoulder.
7. Turn the single hex adjustment screw so the blade
starts to move away from the shoulder of the
wheel — then immediately turn the single hex
adjustment screw in the other direction so the
blade stops, then moves slowly toward the
shoulder.
WARNING:
KEEP FINGERS CLEAR OF THE
BLADE AND WHEEL TO AVOID INJURY.
8. Turn the single hex adjustment screw to stop the
motion of the blade on the wheel as it gets closer
to the wheel shoulder. Put a 6-inch length of
paper between the blade and the wheel as shown
in figure 13. The paper should not be cut as it
passes between the wheel shoulder and blade.
9. Turn the single hex adjustment screw a small
amount. Repeat the insertion of the paper be-
tween the wheel shoulder and the blade until the
paper is cut in two pieces.
NOTE:
You may have to repeat the check with the
paper several times before the blade and the shoulder
cuts the paper into two pieces. Do not hurry the
adjustment. Patience and accuracy here will pay off
with better, more accurate, quieter cutting and much
longer machine and blade life.
10. When the paper is cut, turn the hex adjustment
screw slightly in the counterclockwise direction.
Figure 12: Blade tracking and tensioning
Blade Tracking
Hex Adjustment
Screws
Center
Locking
Screws
Single
Adjustment
Screw