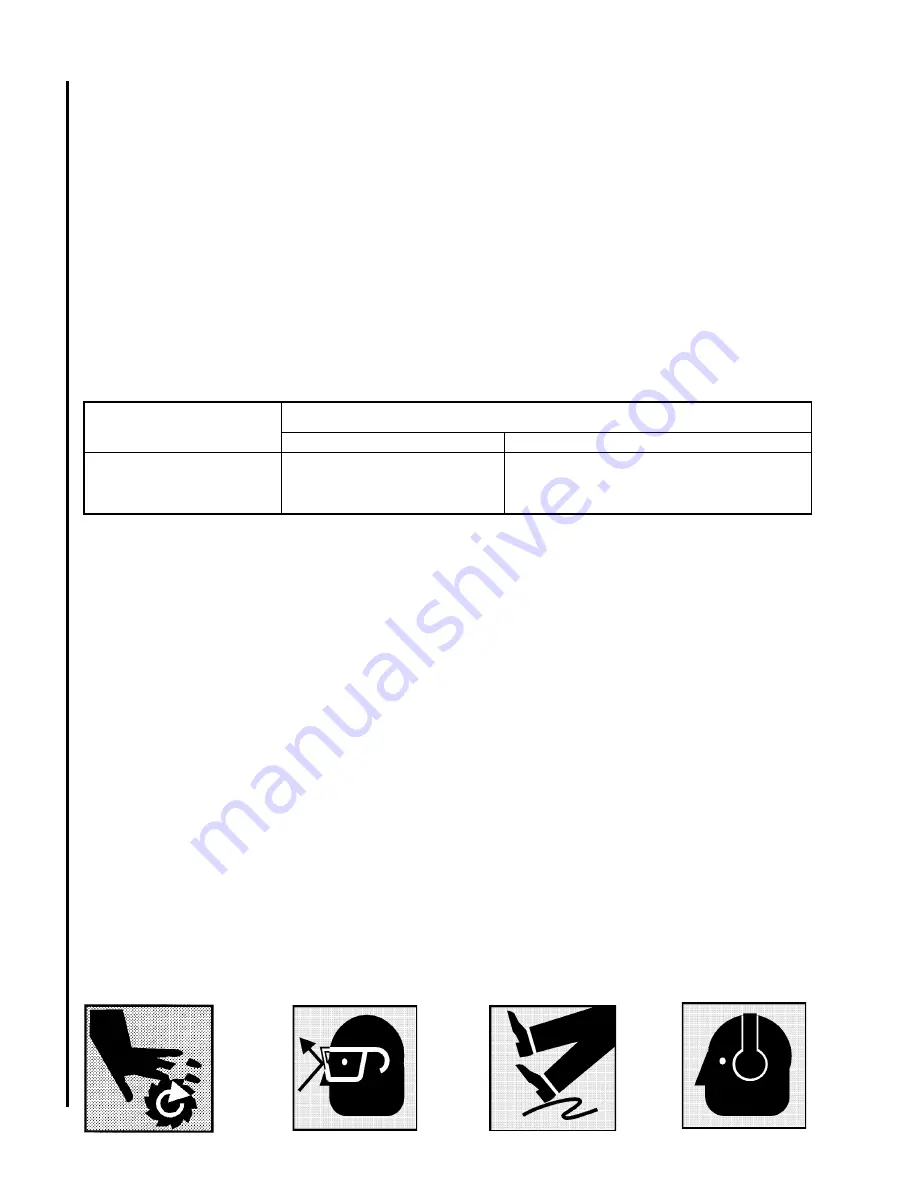
6
Safety Instructions on Sawing Systems
B
C
D
8. Bring adjustable saw guides and guards as close
as possible to the workpiece.
9. Always wear protective eye wear when operating,
servicing, or adjusting machinery. Eyewear shall
be impact resistant, protective safety glasses
with side shields complying with ANSI Z87.1
specifications. Use of eye wear which does not
comply with ANSI Z87.1 specifications could
result in severe injury from breakage of eye
protection.
See Figure B.
10. Nonslip footwear and safety shoes are recom-
mended.
See Figure C.
11. Wear ear protectors (plugs or muffs) during
extended periods of operation.
See Figure D.
12. The workpiece, or part being sawed, must bese-
curely clamped before the saw blade enters the
workpiece.
13. Remove cut off pieces carefully, keeping hands
away from saw blade.
14. Saw must be stopped and electrical supply cut
off or machine unplugged before reaching into
cutting area.
15. Avoid contact with coolant, especially guarding
your eyes.
A
1. Always wear leather gloves when handling saw
blade. The operator shall not wear gloves when
operating the machine.
2. All doors shall be closed, all panels replaced, and
other safety guards in place prior to the machine
being started or operated.
3. Be sure that the blade is not in contact with the
workpiece when the motor is started. The motor
shall be started and you should allow the saw to
come up to full speed before bringing the saw
blade into contact with the workpiece.
4. Keep hands away from the blade area.
See
Figure A.
5. Remove any cut off piece carefully while keeping
your hands free of the blade area.
6. Saw must be stopped and electrical supply must
be cut off before any blade replacement or
adjustment of blade support mechanism is done,
or before any attempt is made to change the
drive belts or before any periodic service or
maintenance is performed on the saw.
7. Remove loose items and unnecessary
workpieces from area before starting machine.
20. Some dust created by power sanding, sawing,
grinding, drilling and other construction activities
contains chemicals known to cause cancer, birth
defects or other reproductive harm. Some ex
amples of these chemicals are:
Lead from lead based paint
Crystalline silica from bricks and cement
and other masonry products, and
arsenic and chromium from chemically-
treated lumber.
21. Your risk from those exposures varies, depending
on how often you do this type of work. To reduce
your exposure to these chemicals: work in a well
ventilated area, and work with approved safety
equipment, such as those dust masks that are
specifically designed to filter out microscopic
particles.
General Electrical Cautions
This saw should be grounded in accordance with
the National Electrical Code and local codes and
ordinances. This work should be done by a qualified
electrician. The saw should be grounded to protect
the user from electrical shock.
Wire SizesCaution:
For circuits which are far away from the electrical
service box, the wire size must be increased in order
to deliver ample voltage to the motor. To minimize
power losses and to prevent motor overheating and
burnout, the use of wire sizes for branch circuits or
electrical extension cords according to the following
table is recommended.
Conductor Length
AWG (American Wire Gauge) Number
240 Volt Lines
120 Volt Lines
0 - 50 Feet
No. 14
No. 14
50 - 100 Feet
No. 14
No. 12
Over 100 Feet
No. 12
No. 8