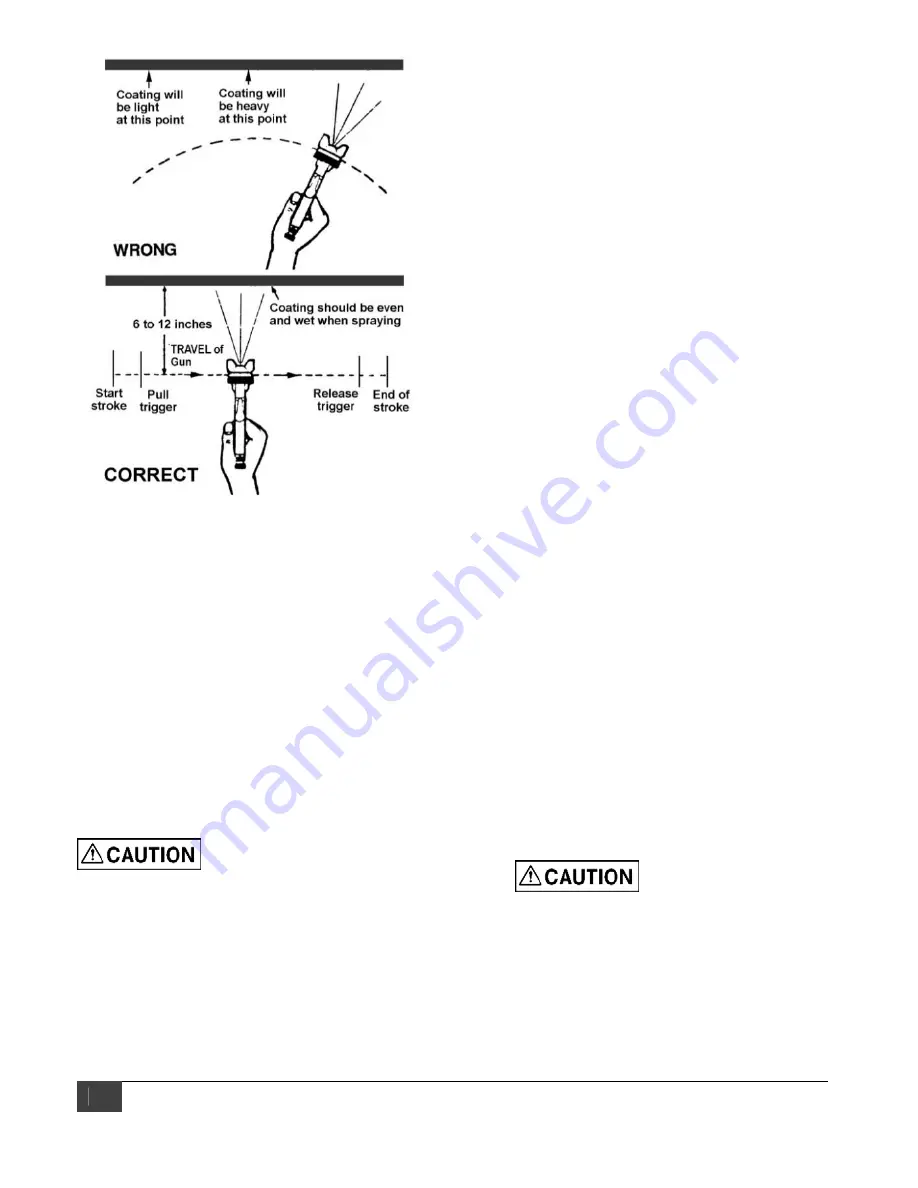
8
JAT-501 Mini HVLP Spray Gun
Figure 2
Maintenance
Note: All parts on a spray gun should be screwed
in hand tight at first; this will avoid the possibility
of cross threading the parts. If parts cannot be
turned by hand easily, make sure you have the
correct parts, unscrew, realign and try again.
Never use undue force in mating parts.
All nozzles and needles are precision made – they
should be handled carefully. When changing to a
different nozzle size, make sure that complete
nozzle set is exchanged (air cap/nozzle/needle).
Adjust fluid control knob so that when gun is
triggered, air-flow occurs before fluid-flow.
Do not probe any holes in
nozzle with metal instruments, as damage to
spray gun can affect proper operation.
Cleaning
1. After use, remove cup and drain residual
material. Rinse cup with a cleaning solution
or water, depending upon material used.
Place cleaning solution into cup and install
on gun. Spray solution through the gun until
it sprays clear. Do NOT immerse the entire
gun in solvent.
2.
Disconnect air hose from tool.
3.
Remove air cap and clean. Make sure holes
in horns are clean.
4. Use solvent and the provided brush to
remove any deposits around fluid nozzle.
5. For more detailed cleaning, use provided
spanner to remove fluid control knob, fluid
nozzle, and needle (in that order). Clean
nozzle and needle with brush and solution.
Reassemble parts by reversing above order.
6. Periodically lubricate the gun. Use a light
machine oil (Air Tool Oil or SAE #10) on the
following areas. Do not
use lubricants
containing silicone.
•
Fluid needle packing (to prevent needle
from sticking)
•
Air valve packing
•
Trigger
pivot
point
•
Threaded
parts
Storage
Hang the spray gun by its hook when not in use,
to prevent leaks or blockages. Disconnect air
hose before storage.
Air system requirements
1. Use proper air hose size (refer to tool
specifications). The hose should be just long
enough to serve the working area. Excessive
hose length will cause pressure drop.
2. Make sure air compressor supplies clean,
dry air at correct CFM for tool.
3. Set air pressure according to tool
specifications.
Excess air pressure
and/or unclean air will shorten the tool’s
life and may create a hazardous situation.
4.
Drain water from air compressor tank daily,
as well as any condensation from air lines.
Water in the air line may enter the tool and
cause damage.
5.
Change filters on the air system on a regular
basis.