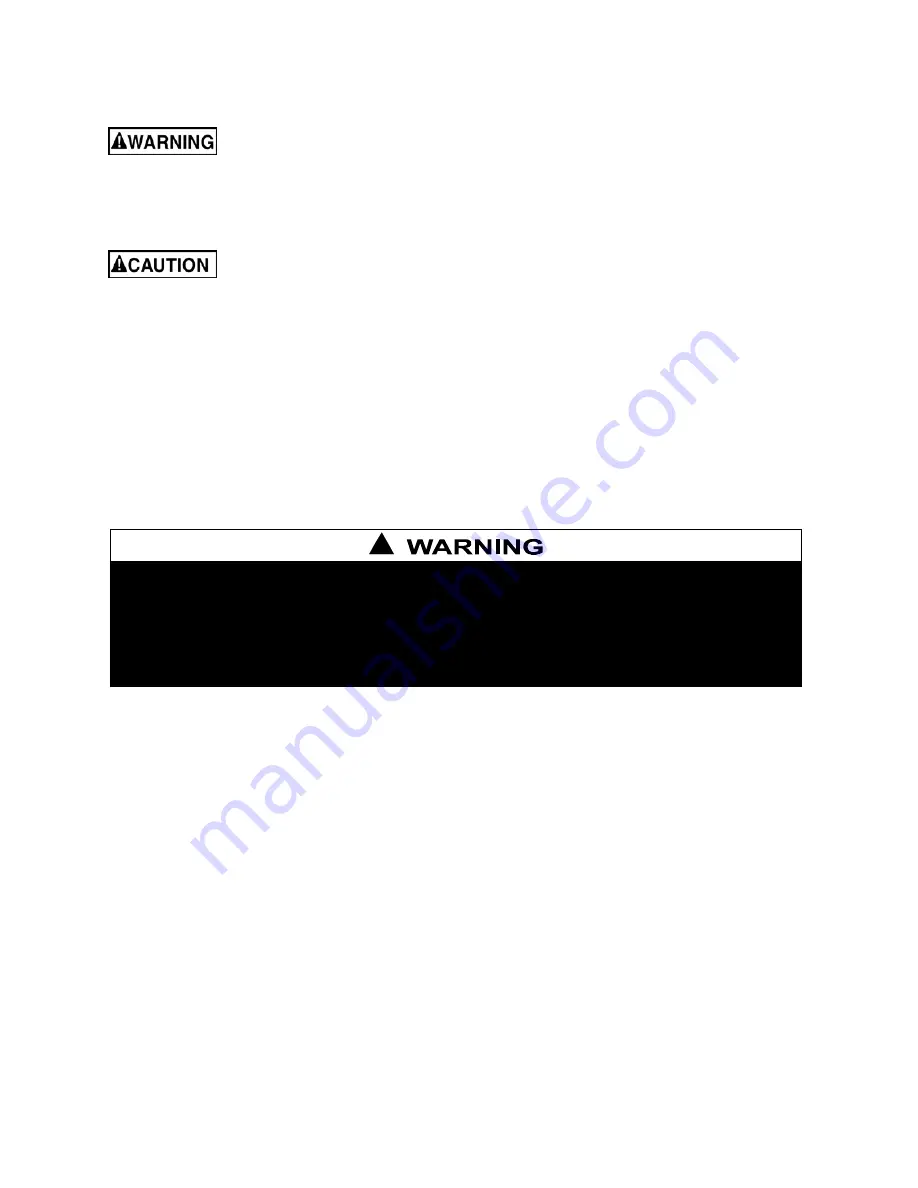
6
Familiarize yourself with the following safety notices used in this manual.
This means that if precautions are not heeded, it may result in serious injury or possibly even
death
.
This means that if precautions are not heeded, it may result in minor or moderate injury and/or
possible machine damage
.
Safety Decals
Familiarize yourself with the location and content of these decals on your planer.
!
1. Read instruction manual before operating machine.
2. Do not operate without all guards properly installed.
3. Remove or fasten loose articles of clothing such as neckties, etc.
Contain long hair.
4. Remove jewelry such as finger rings, watches, bracelets, etc.
5. Use approved safety glasses and/or face shield to protect eyes, and
use other personal safety equipment as required. Do not wear
gloves.
6. Disconnect machine from power source before making any
adjustments or cleaning chips away from machine.
7. Keep the floor around machine clean and free from scraps,
sawdust, oil and grease to minimize the danger of slipping.
8. Do not operate this machine while under the influence of alcohol
or drugs.
9. Failure to comply with these warnings may result in serious
personal injury.
DO NOT REMOVE OR OBSCURE THIS LABEL