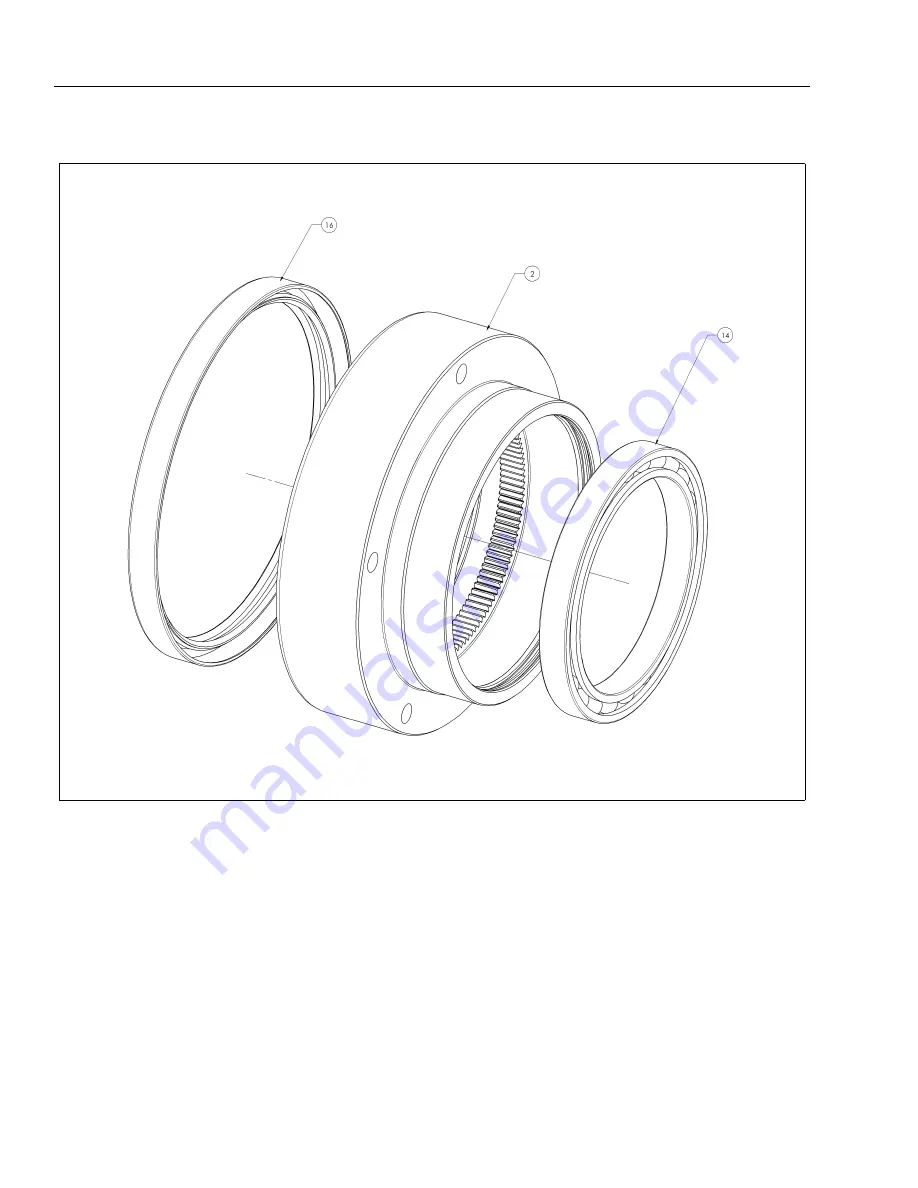
SECTION 4 - BASE COMPONENTS
4-24
– JLG Lift –
3121222
Hub Sub-Assembly
Hub Sub-Assembly
1.
Put Hub (2) on a table with the tapped holes facing down.
2.
Using a flat plate in conjunction with a pressing tool, press in the Seal (16) so it is flush with the edge of the
hub.
NOTE:
NOTE: The Seal has a thin outer shell that can be easily damaged if not installed with care. It is a good idea to start
the Seal into the bore with a rubber mallet before pressing.
3.
Flip the Hub (2) over
4.
Using the appropriate pressing tool (T-174356), press the Main Bearing (15) into the bore until it bottoms
out.
Summary of Contents for 1230ES
Page 1: ...AS NZS Service and Maintenance Manual Model s 1230ES P N 3121222 June 22 2017 ...
Page 2: ...NOTES ...
Page 24: ...SECTION 1 MACHINE SPECIFICATIONS 1 12 JLG Lift 3121222 NOTES ...
Page 32: ...SECTION 2 GENERAL SERVICE INFORMATION 2 8 JLG Lift 3121222 NOTES ...
Page 78: ...SECTION 4 BASE COMPONENTS 4 40 JLG Lift 3121222 NOTES ...
Page 104: ...SECTION 5 CONTROL COMPONENTS 5 26 JLG Lift 3121222 NOTES ...
Page 158: ...SECTION 8 DIAGNOSTIC TROUBLE CODES 8 22 JLG Lift 3121222 NOTES ...
Page 198: ...SECTION 9 GENERAL ELECTRICAL INFORMATION SCHEMATICS 9 40 JLG Lift 3121222 ...
Page 199: ...SECTION 9 GENERAL ELECTRICAL INFORMATION SCHEMATICS 3121222 JLG Lift 9 41 ...
Page 200: ...SECTION 9 GENERAL ELECTRICAL INFORMATION SCHEMATICS 9 42 JLG Lift 3121222 ...
Page 202: ...SECTION 9 GENERAL ELECTRICAL INFORMATION SCHEMATICS 9 44 JLG Lift 3121222 NOTES ...