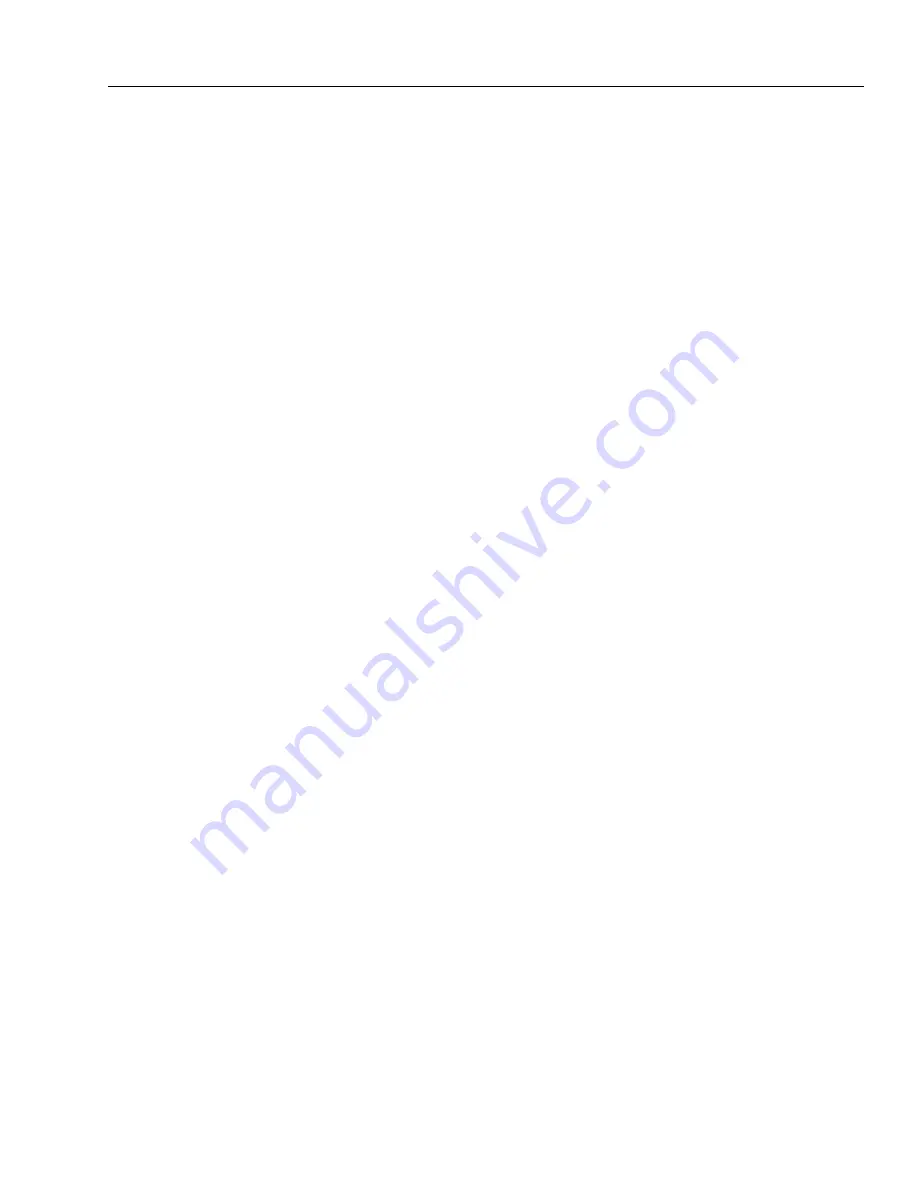
SECTION 4 - BOOM & PLATFORM
3121619
4-1
SECTION 4. BOOM & PLATFORM
4.1
BOOM SYSTEMS
Broken Cable Indicator System
The boom on this model is a 5 section proportionally driven
telescopic boom. Section #2 is driven directly by the telescope
cylinder. Section #3, #4, and #5 (fly boom) are each driven by
separate wire rope systems. Each rope system contains redun-
dant ropes that are capable of allowing the operator to
unknowingly continue use of the machine with a single rope
failure. These kinds of failures with the extend ropes are self
revealing to the operator so proper action can be taken. Fail-
ures within section #4 and section #5 extend ropes are self
revealing as they are exposed on the exterior of the boom
where a broken rope would be obvious. Failures within section
#3 ropes require the addition of the Broken Cable Indicator
System in order to be self-revealing to the operator. This sys-
tem uses proximity sensors to detect excessive movement of
the sensed ropes as would be expected with a rope failure. A
broken rope detection results in illuminating the Cable Break
indicator on the platform control panel. No restrictions are
made to the functionality of the control system. It is the
responsibility of the operator to take the appropriate action.
Transport Position Sensing System
The transport position sensing system uses the main boom
angle sensors, the main boom length sensor mounted in the
pivot end of the main section #1boom in addition to the boom
length switch mounted on the platform end of the main base
boom and transport proximity switches mounted to the jib fly
boom to sense when the main boom and jib boom are in the
position associated with high speed travel. Above transport
angle is recognized when the main boom (using the cylinder
angle sensors) is more than 5º with respect to the turntable
and resets to within transport position when both main boom
angle sensors read less than 3º with respect to the turntable.
Transport length is recognized when the main boom length
switch and main boom length sensor read less than 17" exten-
sion for the main boom. Transport position is also determined
when the jib boom length switches indicate the jib is fully
retracted. During failures of either the main boom length
transport switch or the main boom length sensor the main
boom transport length will be determined by the remaining
sensor or switch. In addition, for a failure of either jib transport
length switch, jib length will be determined by the remaining
switch.
This system is used to control the following systems:
• Beyond Transport - Drive Speed Cutback System
• Drive/Steer - Boom Function Interlock System - CE Only
• Jib Stow System
• Axle Extension System
Beyond Transport - Drive Speed Cutback System
When boom is positioned beyond the Transport Position, the
drive motors are automatically restricted to their maximum
displacement position (slow speed).
Drive/Steer - Boom Function Interlock System (CE/
AUS ONLY)
The Drive/Steer - Boom Function Interlock System uses the
Transport Position Sensing System (item 14) to sense when the
boom and jib are out of the transport position. All controls are
simultaneously functional when the booms are within the
transport position as on the standard machine. When the
boom/jib are beyond the transport position, the control func-
tions are interlocked to prevent simultaneous operation of any
boom function with drive/steer. The first function set to be
operated in this mode, becomes the master function set. In
other words, while operating drive/steer functions the boom
functions are inoperable. Likewise, while operating boom
functions drive/steer functions are inoperable.
Jib Stow System
The machine's stowed length can be reduced to facilitate
transportation on standard trailers by swinging the jib to the
right using the hydraulic power of the jib stow rotator. The
control system will prevent swinging the jib unless the axles
are retracted, the boom and jib are in the transport position. If
the transport criteria are met and the operator commands jib
swing right via the jib swing function switch. The control sys-
tem will retract the jib lock pin and begin to swing the jib into
the stowed position. When the jib is stowed, automatic plat-
form leveling is disabled, the boom is restricted to the trans-
port position, and axle extension is disabled. This system is
functional only in the 500# mode of the Dual Capacity System.
Jib telescope function will resume when the jib is nearly fully
stowed alongside the main boom. Conversely, the jib must be
retracted into the transport position before the jib is allowed
to swing left into the locked position. Once the jib reaches the
inline position, and the operator is maintaining the jib swing
left function switch the control system will attempt to lock the
jib lock pin. If successful, the jib lock pin lamp will illuminate
continuously after the operator releases jib swing function
switch.
Summary of Contents for 1850SJ
Page 1: ...Service and Maintenance Manual Model 1850SJ 3121619 June 29 2018 Rev J AS NZS...
Page 2: ......
Page 21: ...3121619 xvii LIST OF FIGURES FIGURE NO TITLE PAGE NO Thispageleftblankintentionally...
Page 24: ...xx 3121619 LIST OF TABLES TABLE NO TITLE PAGE NO Thispageleftblankintentionally...
Page 50: ...SECTION 2 GENERAL 2 12 3121619 NOTES...
Page 55: ...SECTION 3 CHASSIS TURNTABLE 3121619 3 5 This page left blank intentionally...
Page 56: ...SECTION 3 CHASSIS TURNTABLE 3 6 3121619 Figure 3 4 Axle Hose Routing Sheet 1 of 2...
Page 57: ...SECTION 3 CHASSIS TURNTABLE 3121619 3 7 Figure 3 5 Axle Hose Routing Sheet 2 of 2...
Page 58: ...SECTION 3 CHASSIS TURNTABLE 3 8 3121619 Figure 3 6 Steering Axle Hydraulic Circuit...
Page 61: ...SECTION 3 CHASSIS TURNTABLE 3121619 3 11 Figure 3 9 Turntable Hydraulic System...
Page 92: ...SECTION 3 CHASSIS TURNTABLE 3 42 3121619 Figure 3 39 Swing Bearing Wear Tolerance...
Page 94: ...SECTION 3 CHASSIS TURNTABLE 3 44 3121619 Figure 3 41 Swing Bearing Removal Sheet 2 of 4...
Page 110: ...SECTION 3 CHASSIS TURNTABLE 3 60 3121619 Figure 3 54 Engine Electrical Circuit...
Page 169: ...SECTION 4 BOOM PLATFORM 3121619 4 7 Figure 4 1 Boom Hydraulic System...
Page 173: ...SECTION 4 BOOM PLATFORM 3121619 4 11 Figure 4 2 Boom Assembly Sheet 1 of 9...
Page 174: ...SECTION 4 BOOM PLATFORM 4 12 3121619 Figure 4 3 Boom Assembly Sheet 2 of 9...
Page 175: ...SECTION 4 BOOM PLATFORM 3121619 4 13 Figure 4 4 Boom Assembly Sheet 3 of 9...
Page 176: ...SECTION 4 BOOM PLATFORM 4 14 3121619 Figure 4 5 Boom Assembly Sheet 4 of 9...
Page 177: ...SECTION 4 BOOM PLATFORM 3121619 4 15 Figure 4 6 Boom Assembly Sheet 5 of 9...
Page 178: ...SECTION 4 BOOM PLATFORM 4 16 3121619 Figure 4 7 Boom Assembly Sheet 6 of 9...
Page 179: ...SECTION 4 BOOM PLATFORM 3121619 4 17 Figure 4 8 Boom Assembly Sheet 7 of 9...
Page 180: ...SECTION 4 BOOM PLATFORM 4 18 3121619 Figure 4 9 Boom Assembly Sheet 8 of 9...
Page 181: ...SECTION 4 BOOM PLATFORM 3121619 4 19 Figure 4 10 Boom Assembly Sheet 9 of 9...
Page 187: ...SECTION 4 BOOM PLATFORM 3121619 4 25 Figure 4 16 Boom Assembly Torque Values Sheet 1 of 4...
Page 188: ...SECTION 4 BOOM PLATFORM 4 26 3121619 Figure 4 17 Boom Assembly Torque Values Sheet 2 of 4...
Page 189: ...SECTION 4 BOOM PLATFORM 3121619 4 27 Figure 4 18 Boom Assembly Torque Values Sheet 3 of 4...
Page 190: ...SECTION 4 BOOM PLATFORM 4 28 3121619 Figure 4 19 Boom Assembly Torque Values Sheet 4 of 4...
Page 201: ...SECTION 4 BOOM PLATFORM 3121619 4 39 Figure 4 20 Hose Adjustment...
Page 202: ...SECTION 4 BOOM PLATFORM 4 40 3121619 Figure 4 21 Section 3 Boom Cables...
Page 203: ...SECTION 4 BOOM PLATFORM 3121619 4 41 Figure 4 22 Section 4 Boom Cables...
Page 204: ...SECTION 4 BOOM PLATFORM 4 42 3121619 Figure 4 23 Section 5 Boom Cables...
Page 205: ...SECTION 4 BOOM PLATFORM 3121619 4 43 Figure 4 24 Jib Hydraulics Sheet 1 of 7...
Page 234: ...SECTION 4 BOOM PLATFORM 4 72 3121619 Figure 4 44 Powertrack Shimming Instructions...
Page 239: ...SECTION 4 BOOM PLATFORM 3121619 4 77 Figure 4 49 Powertrack Hose Installation Sheet 1 of 4...
Page 240: ...SECTION 4 BOOM PLATFORM 4 78 3121619 Figure 4 50 Powertrack Hose Installation Sheet 2 of 4...
Page 241: ...SECTION 4 BOOM PLATFORM 3121619 4 79 Figure 4 51 Powertrack Hose Installation Sheet 3 of 4...
Page 242: ...SECTION 4 BOOM PLATFORM 4 80 3121619 Figure 4 52 Powertrack Hose Installation Sheet 4 of 4...
Page 252: ...SECTION 4 BOOM PLATFORM 4 90 3121619 NOTES...
Page 432: ...SECTION 5 BASIC HYDRAULIC INFORMATION HYDRAULIC SCHEMATICS 5 180 3121619 NOTES...
Page 527: ...SECTION 6 JLG CONTROL SYSTEM 3121619 6 95 Figure 6 36 LSS Installation Sheet 1 of 4...
Page 528: ...SECTION 6 JLG CONTROL SYSTEM 6 96 3121619 Figure 6 37 LSS Installation Sheet 2 of 4...
Page 529: ...SECTION 6 JLG CONTROL SYSTEM 3121619 6 97 Figure 6 38 LSS Installation Sheet 3 of 4...
Page 530: ...SECTION 6 JLG CONTROL SYSTEM 6 98 3121619 Figure 6 39 LSS Installation Sheet 4 of 4...
Page 710: ...SECTION 7 BASIC ELECTRICAL INFORMATION ELECTRICAL SCHEMATICS 7 118 3121619 NOTES...
Page 711: ......