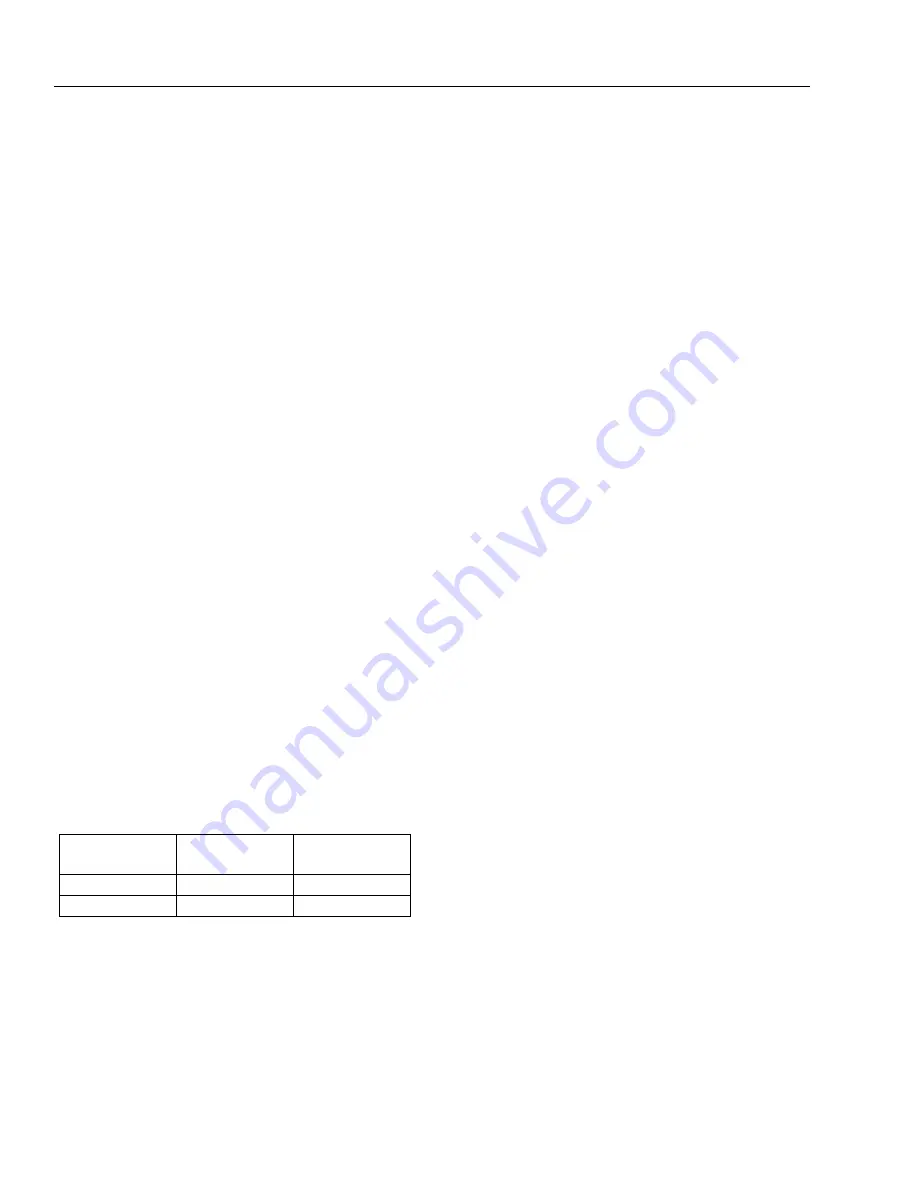
SECTION 2 - SERVICE PROCEDURES
2-6
31215808
Lubrication and Servicing
Components and assemblies requiring lubrication and servic-
ing are shown on the Lubrication Chart in Section 1. Service
applicable components with the amount, type, and grade of
lubricant recommended in this manual, at the specified inter-
vals. When recommended lubricants are not available, consult
your local supplier for an equivalent that meets or exceeds the
specifications listed.
Batteries
Clean batteries, using a non-metallic brush and a solution of
baking soda and water. Rinse with clean water. After cleaning,
thoroughly dry batteries and coat terminals with an anti-cor-
rosion compound.
Mast Chain Inspection Procedure
Inspect mast chains for the following conditions:
Wear:
Always inspect that segment of chain that operates
over a sheave. As the chain flexes over the extend/retract
sheaves, joints and plate edges very gradually wear. Chain
“stretch” can be measured using a manufacturers wear scale or
steel tape. When chains have elongated 3% they must be
removed and replaced. Refer to Table 2-3 for proper chain
specifications and allowable stretch tolerances. Peening and
wear of chain plate edges are caused by sliding over a chain
worn contact face of a sheave, or unusually heavy loads. All of
the above require replacement of the chain and correction of
the cause. Chain side wear, noticeable when pin heads and
outside plates show a definite wear pattern, is caused by mis-
alignment of the sheave/chain anchors and must be corrected
promptly. Do not repair chains; if a section of chain is dam-
aged, replace the entire chain set.
Rust and Corrosion:
Rust and corrosion will cause a major
reduction in the load carrying capacity of the chain, because
these are primary reasons for side plate cracking. The initial
lubrication at the factory is applied in a hot dip tank to assure
full penetration into the joint. Do not steam clean or degrease
chains. At time of chain installation, factory lube must be sup-
plemented by a maintenance program to provide a film of oil
on the chains at all times. If chains are corroded, they must be
inspected, especially the outside plates, for cracks in-line with
the pins. If cracks are found, replace the chain; if no cracks are
discovered, lubricate the chains by dipping in heated oil, and
reinstall on the machine. Keep chains lubricated.
Fatigue Cracks:
Fatigue is a phenomenon that affects most
metals, and is the most common cause of chain plate failures.
Fatigue cracks are found through the link holes, perpendicular
(90 degrees) from the pin in-line position. Inspect chains care-
fully after long time use and heavy loading for this type of
crack. If any cracks are discovered, replace all chains, as seem-
ingly sound plates are on the verge of cracking. Fatigue and
ultimate strength failures on JLG Lifts are incurred as a result of
severe abuse as design specs are well within the rated lifting
capacity of these chains.
Tight Joints:
All joints in the leaf chain should flex freely. On
leaf chain, tight joints are usually caused by rust/corrosion, or
the inside plates “walking” off the bushing. Limber up rusty/
corroded chains
(after inspecting care fully)
with a heavy appli-
cation of oil
(preferably a hot oil dip)
. Tap inside “walking”
plates inward; if “walking” persists, replace the chain. This type
of problem is accelerated by poor lubrication maintenance
practice, and most tight joint chains have been operated with
little or no lubrication. Tight joints on leaf chain are generally
caused by:
a. Bent pins or plates.
b. Rusty joints.
c. Peened plate edges.
Oil rusty chains, and replace chains with bent or peened chain
components. Keep chains lubricated.
Protruding or Turned Pins:
Chains operating with inade-
quate lube generate tremendous friction between the pin and
plates (pin and bushing on leaf chain). In extreme cases, this
frictional torque can actually turn the pins in the outside
press-fit plates. Inspect for turned pins, which can be easily
spotted as the “V” flats on the pin heads are no longer in line.
Replace all chains showing evidence of turned or protruding
pins. Keep chains lubricated.
Chain Anchors and Sheaves:
An inspection of the chain must
include a close examination of chain anchors and sheaves.
Check chain anchors for wear breakage and misalignment.
Anchors with worn or broken fingers should be replaced. They
should also be adjusted to eliminate twisting the chain for an
even load distribution.
Inspect the sheaves, sheave bearings, sheave grooves and pins
for extreme wear, replace as necessary. A worn sheave can
mean several problems, as follows:
a. Chains too tight.
b. Sheave bearings/pin bad.
c. Bent/misaligned chains.
Table 2-3. Chain Stretch Tolerance
Chain Size
Pin to Pin
Measurement
Allowable Stretch
0.50 in. pitch
12 in. or 24 pitches
0.24 in./12 in. span
0.625 in. pitch
15 in. or 24 pitches
0.30 in./15 in. span
Go
to
Discount-Equipment.com
to
order
your
parts