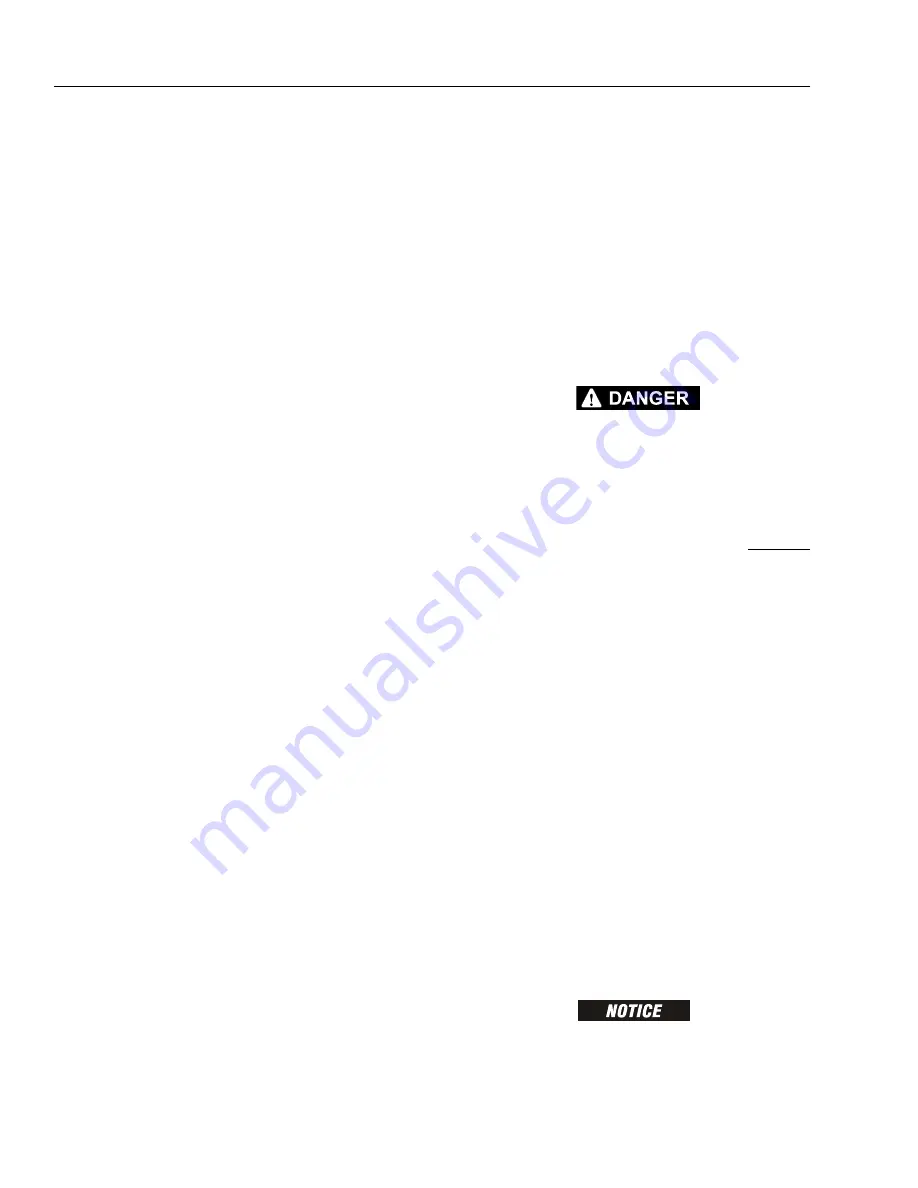
SECTION 3 - CHASSIS & TURNTABLE
3-216
3121160
Cooler Core Cleaning (Exterior)
Remove leaves, papers, etc. from outside face. Use com-
pressed air and carefully blow through the core from the
inside of the canopy (through fan assembly or remove fan
assembly).
DO NOT use high pressure air or pressure washer.
NOTE:
Oil cooler core
is aluminum, if this does at some point
require internal cleaning, this is best done by a suitable
equipped radiator shop. Internal cleaning is NOT a normal
maintenance item if the oil is maintained in good condi-
tion.
Adding/Changing Compressor Oil
Ensure all pressure is relieved from the system. Check oil level
with unit level, otherwise a false oil level indication will occur.
1.
Remove oil fill plug located on main compressor base
casting.
NOTE:
This can be done without lifting canopy.)
2.
Carefully add lubricant and monitor oil level, allow time
for oil to level out. A complete refill is approximately 5 1/
4 quarts (5 liters). Correct oil level is minimum to bottom
threads on oil fill port up until oil runs out of port. Over-
fill can only occur if unit is out of level.
3.
Refit oil fill cap tightly by hand.
4.
Run unit and recheck oil level after shutdown, allowing
time for oil to settle.
Oil drain is provided with short drain hose. This can be routed
to a more convenient location if required, dependent upon
installation. Use only Schedule 80 pipe or suitably rated hose.
NOTE:
Fill cap has a vent release hole as a safety feature and to
act as a ”tell-tale”. If air escapes while unscrewing the fill
cap, then the system still has pressure. Re-tighten the cap
and wait until all pressure is relieved.
Pressure Adjustments
Before adjusting the pressure control system it is necessary to
determine the rated full load pressure setting. These can be
found in the Specification Section.
PRESSURE SWITCH LOCATION:
The pressure switch is located directly behind the cooling fan
inside a black plastic box. Removing the one single screw from
the bottom of the plastic cover allows the cover to be removed
exposing the two adjustment screws at the top and also
exposes the electrical terminations.
ADJUSTMENTS SHOULD BE MADE WITH COMPRESSOR SWITCHED OFF SINCE
ELECTRICAL TERMINALS INSIDE PRESSURE SWITCH WILL BE EXPOSED AND
OPENING THE CANOPY EXPOSES BELT DRIVE SYSTEM.
PROCEDURE FOR SETTING:
1.
Start compressor and allow to warm up. NOTE - Pressure
reading on gauge with service valve closed. Switch off
compressor.
2.
Adjustment screws on pressure switch. Steel slotted
screw (L.H. side upper) will adjust both cut-out and cut-
in pressures together. Screw in clockwise to increase
screw out counter clockwise to decrease. Plastic head
slotted screw (R.H. side upper) will permit changes to
cut-out pressure (higher pressure) without affecting cut-
in pressure. (ie. changes differential pressure range)
screw in clockwise to increase and counterclockwise to
decrease upper pressure setting.
Nominal differential setting 25 to 30 psi (1.7 to 2.0 Bar).
This
is to reduce load/unload cycle in cases where mini-
mal air usage or leaks in hoses/connections may occur.
The recovery period from unload to load is rapid with
the screw compressor and this initial setting will suit
most applications.
It is suggest to make adjustments in
%
turn increments
then close canopy, restart and check pressure. Re-adjust
as necessary.
When desired pressure is set, replace switch cover and
close canopy for operation.
INCREASING AIR PRESSURE WILL INCREASE THE REQUIRED COMPRESSOR H.P.
BE SURE THE HYDRAULIC POWER SUPPLY IS CAPABLE (HYDRAULIC PRES-
SURE) OTHERWISE THE COMPRESSOR MAY STALL OUT DURING OPERATION
DUE TO INCREASED POWER REQUIREMENT.
Summary of Contents for 740AJ
Page 2: ......
Page 55: ...SECTION 3 CHASSIS TURNTABLE 3121160 3 3 This page left blank intentionally...
Page 116: ...SECTION 3 CHASSIS TURNTABLE 3 64 3121160 Figure 3 44 Swing Hub Prior to SN 0300074383...
Page 203: ...SECTION 3 CHASSIS TURNTABLE 3121160 3 151 Figure 3 77 EFI Component Location...
Page 206: ...SECTION 3 CHASSIS TURNTABLE 3 154 3121160 Figure 3 78 ECM EPM Identification ECM EPM...
Page 224: ...SECTION 3 CHASSIS TURNTABLE 3 172 3121160 Figure 3 83 Deutz EMR 2 Troubleshooting Flow Chart...
Page 228: ...SECTION 3 CHASSIS TURNTABLE 3 176 3121160 Figure 3 87 EMR 2 Engine Plug Pin Identification...
Page 229: ...SECTION 3 CHASSIS TURNTABLE 3121160 3 177 Figure 3 88 EMR 2 Vehicle Plug Pin Identification...
Page 230: ...SECTION 3 CHASSIS TURNTABLE 3 178 3121160 Figure 3 89 EMR2 Fault Codes Sheet 1 of 5...
Page 231: ...SECTION 3 CHASSIS TURNTABLE 3121160 3 179 Figure 3 90 EMR2 Fault Codes Sheet 2 of 5...
Page 232: ...SECTION 3 CHASSIS TURNTABLE 3 180 3121160 Figure 3 91 EMR2 Fault Codes Sheet 3 of 5...
Page 233: ...SECTION 3 CHASSIS TURNTABLE 3121160 3 181 Figure 3 92 EMR2 Fault Codes Sheet 4 of 5...
Page 234: ...SECTION 3 CHASSIS TURNTABLE 3 182 3121160 Figure 3 93 EMR2 Fault Codes Sheet 5 of 5...
Page 303: ...SECTION 4 BOOM PLATFORM 3121160 4 31 Figure 4 20 Rotator Assembly HELAC...
Page 460: ...SECTION 5 BASIC HYDRAULIC INFORMATION AND SCHEMATICS 5 116 3121160 NOTES...
Page 467: ...SECTION 6 JLG CONTROL SYSTEM 3121160 6 7 Figure 6 2 ADE Block Diagram...
Page 534: ...SECTION 6 JLG CONTROL SYSTEM 6 74 3121160 NOTES...
Page 580: ...SECTION 7 BASIC ELECTRICAL INFORMATION SCHEMATICS 7 46 3121160 NOTES...
Page 581: ......