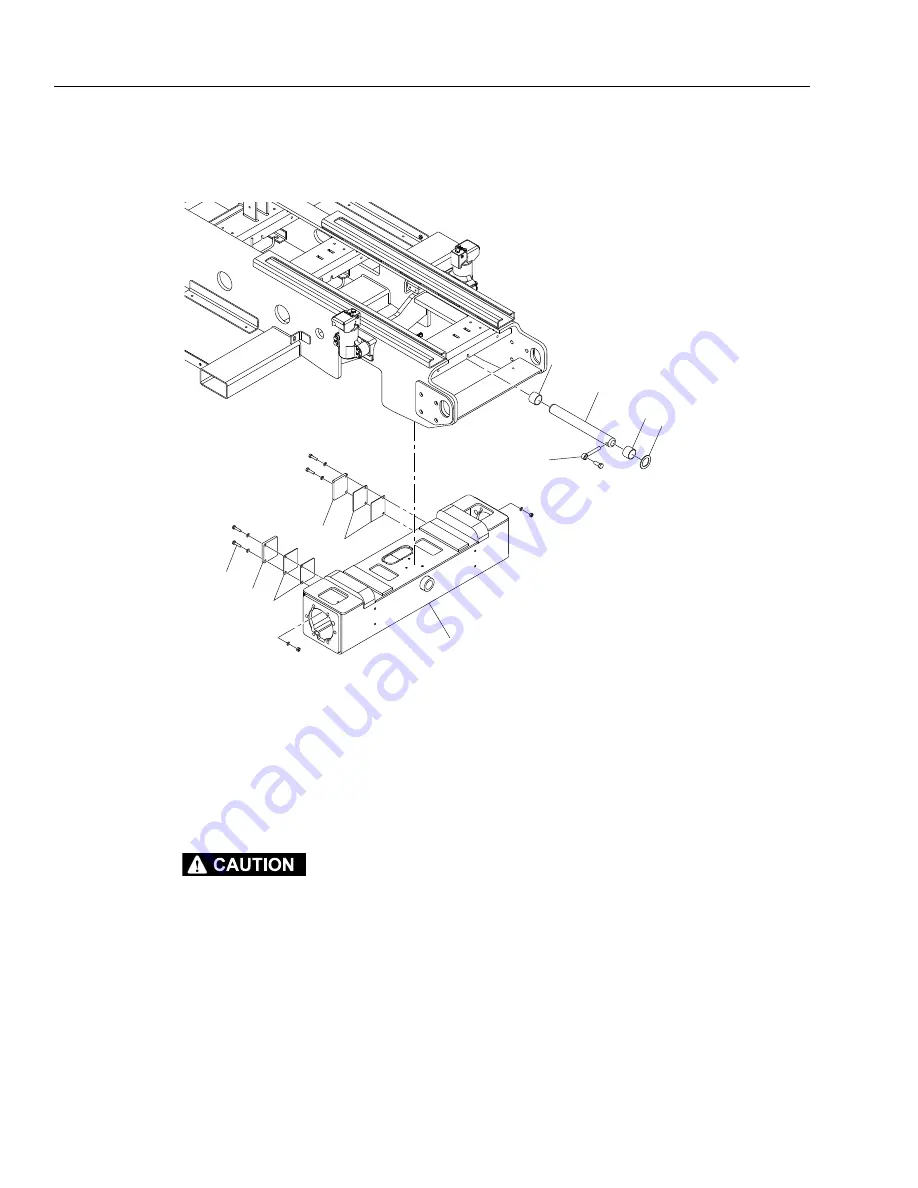
SECTION 3 - CHASSIS, PLATFORM, & SCISSOR ARMS
3-56
31215923
Removal
SUPPORT THE FRAME AND AXLE BEFORE ATTEMPTING ANY REMOVAL
AND/OR ASSEMBLY PROCEDURES.
1. Disable machine operation. Remove wheel and drive
assemblies.
2. Remove the bolt and pin keeper (5).
3. Push the axle pivot pin (2) out and remove the thrust
washer (4).
4. Axle (1) can now be moved away from the frame.
Assembly
1. When installing the axle assembly, follow Removal
Steps in reverse.
2. If removed, shim the wear pad to achieve a maxi-
mum gap of 0.06 in. (1.5 mm) between the pad and
the axle machined surface.
3. For Dual Oscillating Rear Axle If removed, shim the
wear pad to achieve a maximum gap of 0.12 in. (3
mm) between the pad and the axle machined sur-
face.
NOTE:
Apply Medium Strength Threadlocking Compound
to bolts (8) attaching wear pad (6) to the frame.
torque to 35 ft. lbs. (47 Nm).
Inspect bushing, replace if damaged.
1. Axle
2. Pivot Pin
3. Pivot Pin Bushing
4. Thrust Washer
5. Pin Keeper and Bolt
6. Wear Pad Shim
7. Wear Pad
8. Hex Head Screws
Figure 3-38. Axle Installation (Rear Axle)- For Dual Oscillating
MAF42460A
1
2
3
3
4
5
6
6
7
7
8
Summary of Contents for ERT2669
Page 2: ......
Page 4: ...INTRODUCTION A 2 31215923 REVISON LOG Original Issue A January 08 2021...
Page 12: ...viii 31215923 TABLE OF CONTENTS...
Page 40: ...SECTION 1 SPECIFICATIONS 1 22 31215923...
Page 58: ...SECTION 2 GENERAL 2 18 31215923...
Page 187: ...SECTION 4 BASIC HYDRAULIC INFORMATION SCHEMATICS 31215923 4 11...
Page 206: ...SECTION 4 BASIC HYDRAULIC INFORMATION SCHEMATICS 4 30 31215923...
Page 225: ...SECTION 4 BASIC HYDRAULIC INFORMATION SCHEMATICS 31215923 4 49...
Page 242: ...SECTION 4 BASIC HYDRAULIC INFORMATION SCHEMATICS 4 66 31215923...
Page 307: ...SECTION 5 JLG CONTROL SYSTEM 31215923 5 65...
Page 334: ...SECTION 6 LSS SETUP CALIBRATION SERVICE 6 12 31215923...
Page 362: ...SECTION 7 GENERAL ELECTRICAL INFORMATION SCHEMATICS 7 28 31215923...
Page 374: ...SECTION 7 GENERAL ELECTRICAL INFORMATION SCHEMATICS 7 40 31215923...
Page 375: ......